Which Wall Material Has the Best U Value?
What are the U values of different wall materials? Understand that, and you are well on your way to making your self build or renovation as thermally efficient as possible, says sustainable building expert Tim Pullen
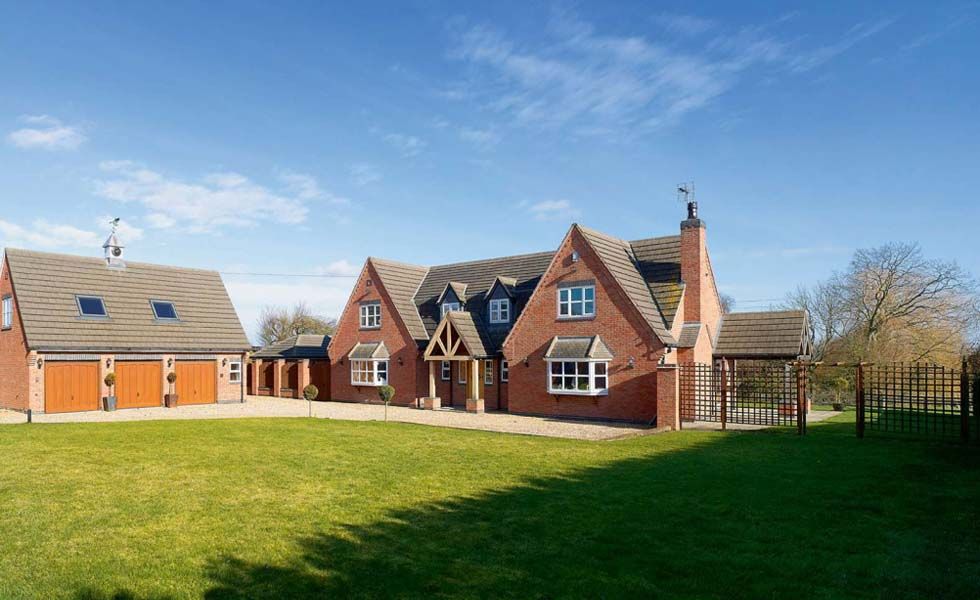
What exactly is a U value and why do architects, self builders and energy-efficiency experts get so excited about it?
Put simply, U values measure how easy it is for heat to pass through a structure (or its ‘thermal conductivity’), so the lower the number the better. To put it another way: low U values mean that only a small amount of heat is escaping through your walls, windows or floors.
To put that into context: a single-glazed window will have a U value of 5.0, a standard double-glazed window around 1.6 and triple glazed around 0.8. Building Regulations require a wall of no worse than 0.3, roof 0.16, and ground floor 0.22.
All of these U values are written as W/m2K. That is, Watts (of heat) passing through every square metre (m2) for each 1°C temperature difference (between the inside and outside of the building). The U value is therefore a measure of thermal efficiency. While that is important, it is only one measure of thermal efficiency and should not be considered on its own.
U Values of Different Wall Types
Each element of a wall will have an R value — the measure of its thermal resistance. To arrive at a U value we need to consider all the components. Taking a simple wall, and working from the inside to the outside, we might have 12mm plasterboard, 100mm concrete block, 90mm insulation in the cavity with a 110mm brick outer skin. Thickness matters, as the thicker the material the more it resists conducting heat.
If we take the R value of all those materials, at those thicknesses, and do some clever maths (there are websites that will do it for us) we get a U value for that wall of 0.3W/m2K — which is Building Regulations standard.
The wall described above is the standard for masonry construction, with the ‘cavity’ filled with mineral wool insulation, giving a wall thickness of 312mm. Clearly, then, this is a solid wall (the cavity is filled, so is no longer a cavity, which is fine with Building Regs).
- U Value = 0.3W/m2K
In recent years the timber frame industry has moved from a 90mm stud for external walls to a 140mm stud — partly to deliver a better U value. The standard construction includes 140mm mineral wool insulation, giving a U value of 0.29W/m2K. With an external skin of timber cladding, brick slips or render installed, the overall wall thickness could be just 225mm.
- U Value = 0.29W/m2K
SIPs are essentially two sheets of OSB (oriented strand board) sandwiching and bonded to insulation — normally polyurethane, polystyrene or, more rarely, mineral wool. Some SIPs offer hemp or other natural insulation options, but these are expensive and not common.
A 140mm standard SIPs panel will give a U value of 0.19W/m2K and an overall wall thickness of 220mm. The reason for the difference between SIPs and timber frame (which are otherwise very similar construction) is the difference between mineral wool and polyurethane. Interestingly, if the SIPs use expanded polystyrene in that same wall, the U value rises to 0.27W/m2K.
- U Value = 0.19W/m2K – 0.27W/m2K
These insulated blocks or panels are assembled on site and filled with reinforced concrete. The insulation is typically expanded polystyrene, and having insulation inside and out gives a U value of at least 0.2W/m2K, with a wall thickness of 250mm. Some systems offer the option to increase the internal insulation and can provide a U value as low as 0.11W/m2K, with a wall thickness of 335mm.
- U Value = 0.11W/m2K – 0.2W/m2K
Costs of Different Wall Types
Assuming the same outer wall finish, the average costs for different wall types will be:
- Brick and block: around £70/m2 with a U value of 0.3W/m2K
- ICF: around £65/m2 with a U value of 0.2W/m2
- Timber frame: around £65/m2 with a U value of 0.24W/m2
- SIPS: around £70/m2 with a U value of 0.19W/m2
ICF and SIPs give inherently better airtightness, so they give better thermal performance for around the same price as timber frame and brick and block.
How to Improve U values
Obviously, the insulation material will improve the U value. The best currently available is the Val-U-Therm system (available from Scotframe) with a U value of 0.09W/m2K from a wall thickness of 235mm, plus the outer skin. Changing the 140mm mineral wool in a timber frame to 140mm polyurethane would give the same U value as a SIPs panel.
Similarly, change the concrete block inner skin of a brick and block wall to an aerated block and use polyurethane instead of mineral wool in the cavity, and the U value will improve to 0.21W/m2K. In other words, the desired U value can be achieved by a bit of juggling.
On-site construction tends to be a less than perfect process. Materials will also have an impact: mineral wool tends to slump in a timber frame, leaving gaps; rigid insulation is seldom cut to be a perfect fit between the studs it is to fill; cavity-fill insulation may not be an airtight fit to the inner block skin.
It is impossible for design calculations to take these imperfections into account and houses tend to have a slightly worse U value than anticipated. The more that can be done off-site in a factory, the more likely it is that the design specification will be met, which is where SIPs and ICF score.
U Values and Building Regulations
The U values stated as ‘Building Regulations standard’ are the elemental U values and even if those figures are all met, the building will not pass the SAP (Standard Assessment Procedure) assessment for energy consumption and CO2 emissions.
The design has to do better than all of these figures to meet SAP requirements and a wall needs to be nearer 0.25W/m2K than 0.3W/m2K to comply. Achieving that in a brick and block wall will increase the wall thickness by at least 50mm, and costs will rise. With all other construction systems, that lower U value is met as standard.
A Final Note on U Values
U values are important but thermal efficiency – reducing the energy demand and the property’s running cost – is becoming increasingly important and means addressing airtightness and thermal bridges as well. A good U value will not compensate for a leaky, poor-quality build.
Starting with a construction system that gives a better U value and airtightness, as well as eliminating thermal bridges, makes obvious sense.
Useful Contacts
Get the Homebuilding & Renovating Newsletter
Bring your dream home to life with expert advice, how to guides and design inspiration. Sign up for our newsletter and get two free tickets to a Homebuilding & Renovating Show near you.
Tim is an expert in sustainable building methods and energy efficiency in residential homes and writes on the subject for magazines and national newspapers. He is the author of The Sustainable Building Bible, Simply Sustainable Homes and Anaerobic Digestion - Making Biogas - Making Energy: The Earthscan Expert Guide.
His interest in renewable energy and sustainability was first inspired by visits to the Royal Festival Hall heat pump and the Edmonton heat-from-waste projects. In 1979
this initial burst of enthusiasm lead to him trying (and failing) to build a biogas digester to convert pig manure into fuel, at a Kent oast-house, his first conversion project.
Moving in 2002 to a small-holding in South Wales, providing as it did access to a wider range of natural resources, fanned his enthusiasm for sustainability. He went on to install renewable technology at the property, including biomass boiler and wind turbine.
He formally ran energy efficiency consultancy WeatherWorks and was a speaker and expert at the Homebuilding & Renovating Shows across the country.
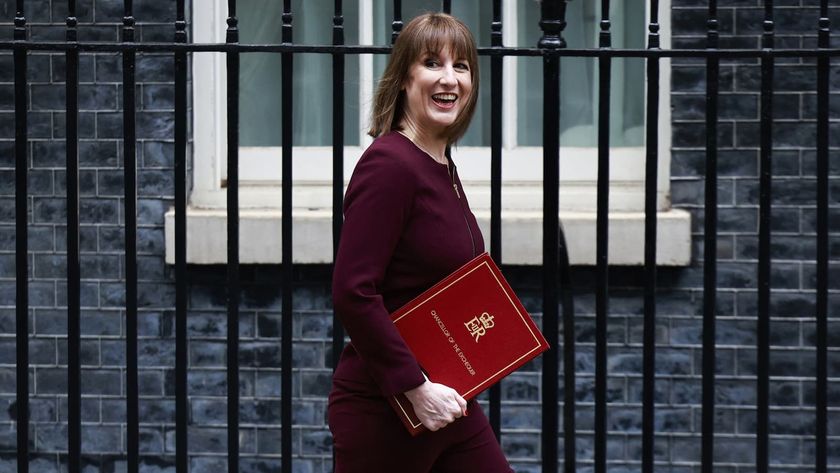
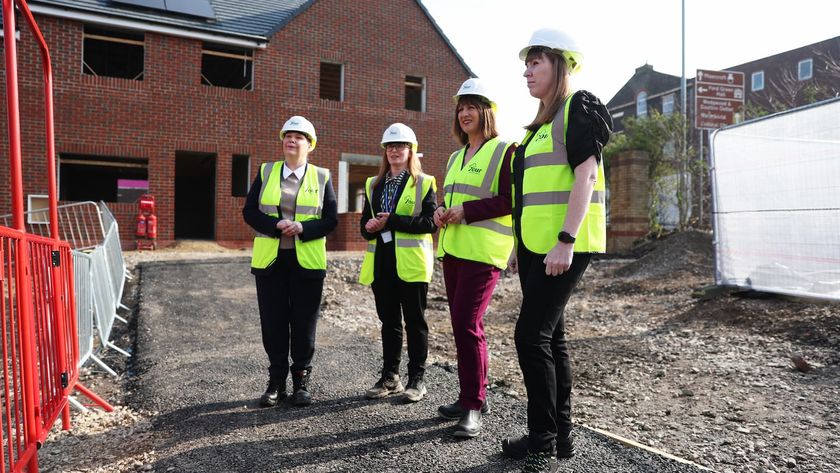
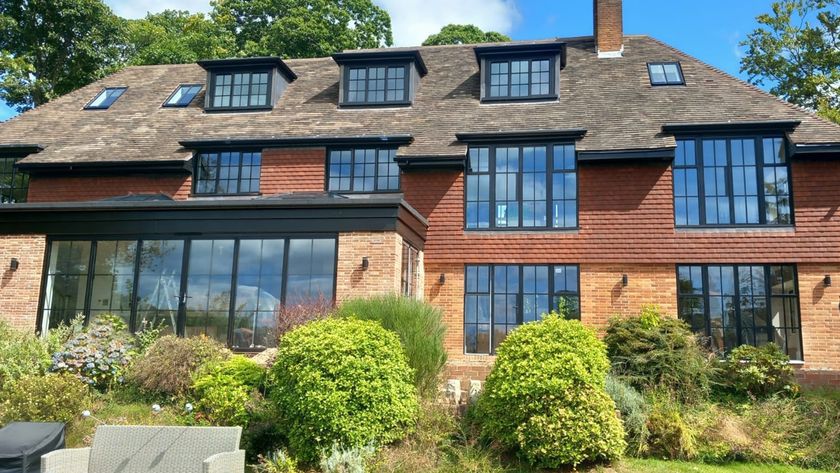
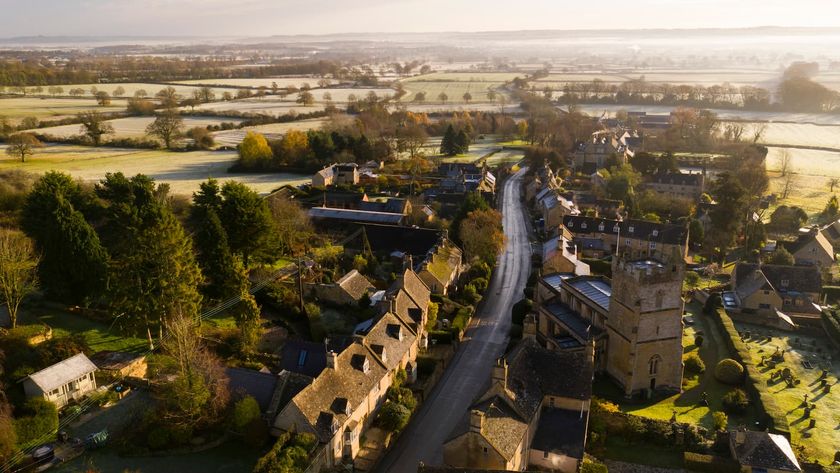
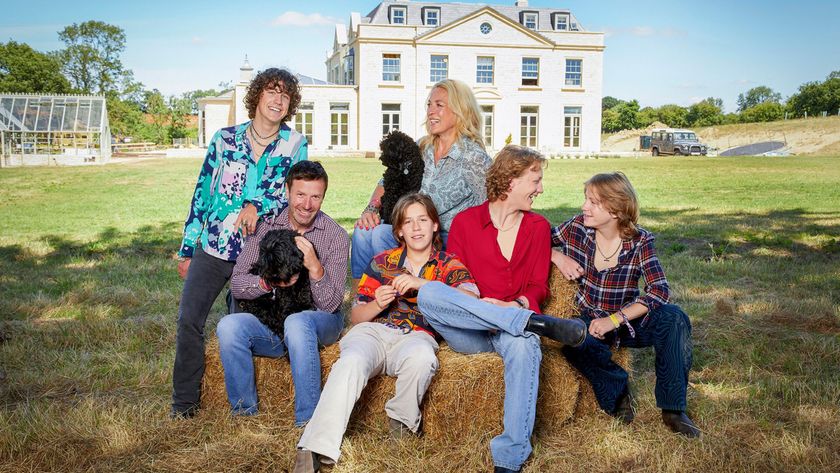
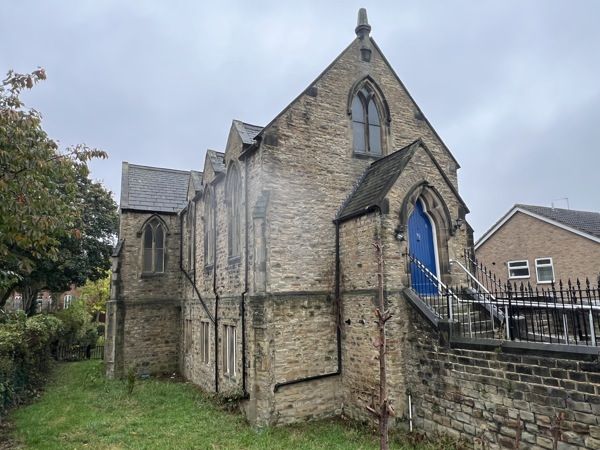
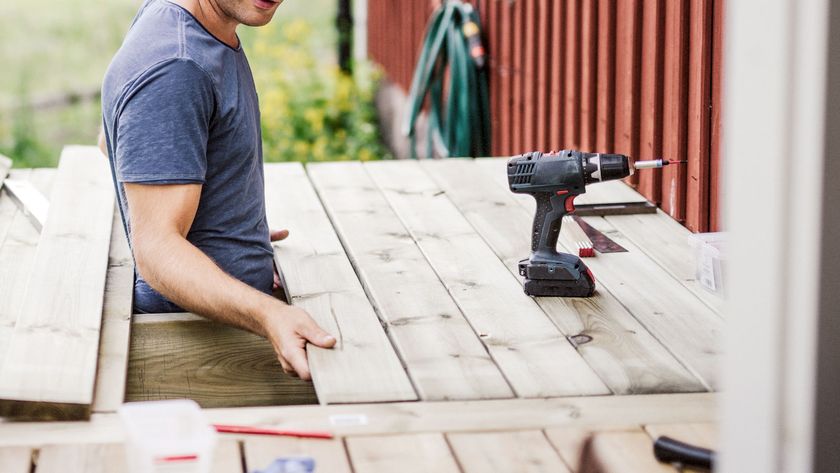
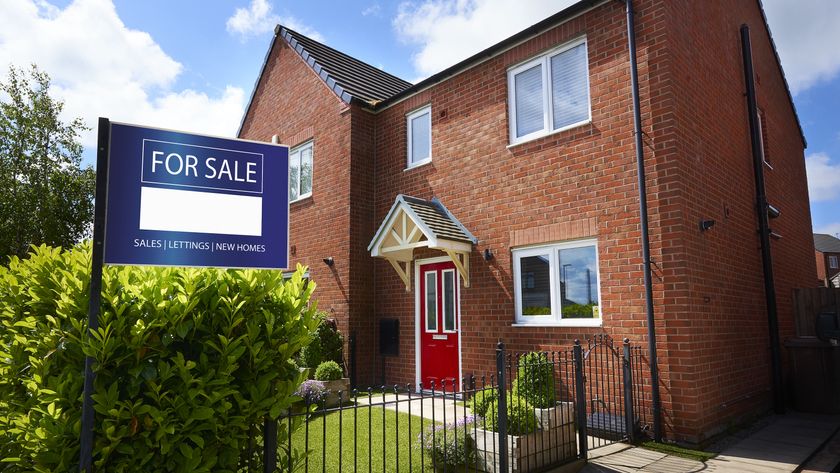
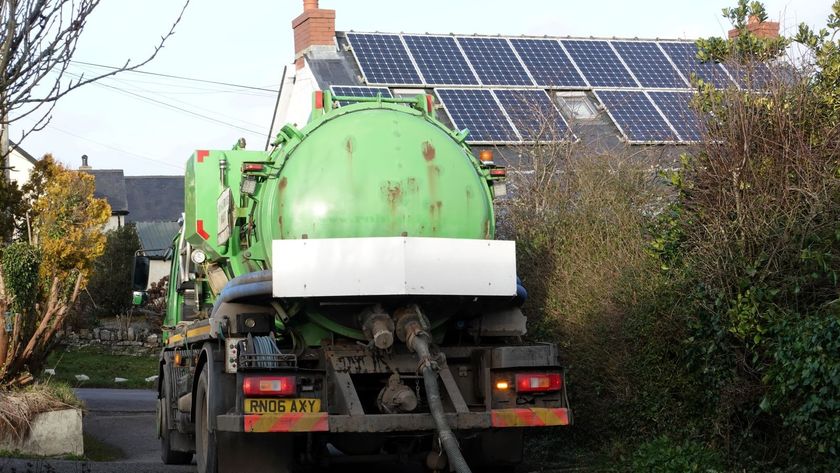
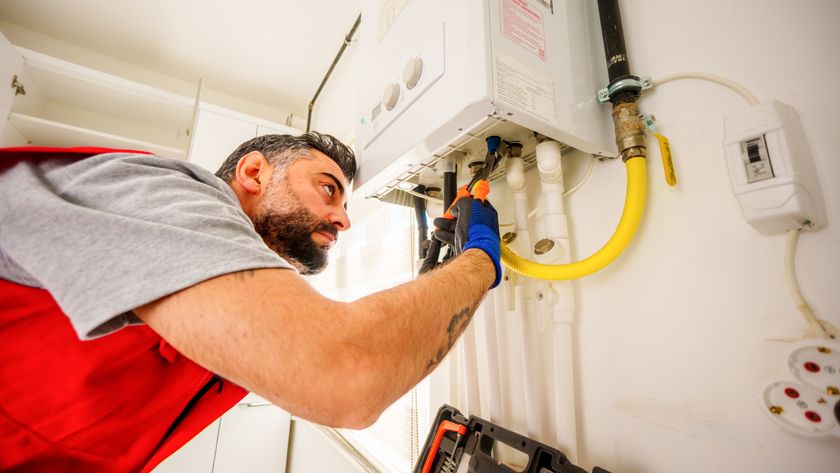
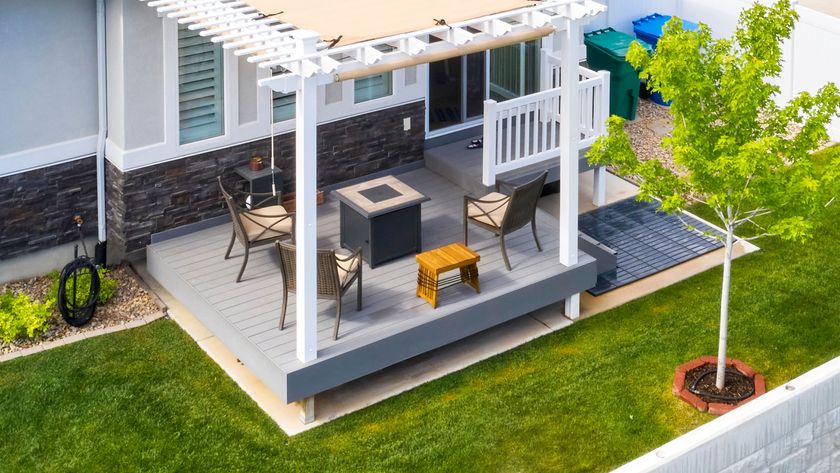
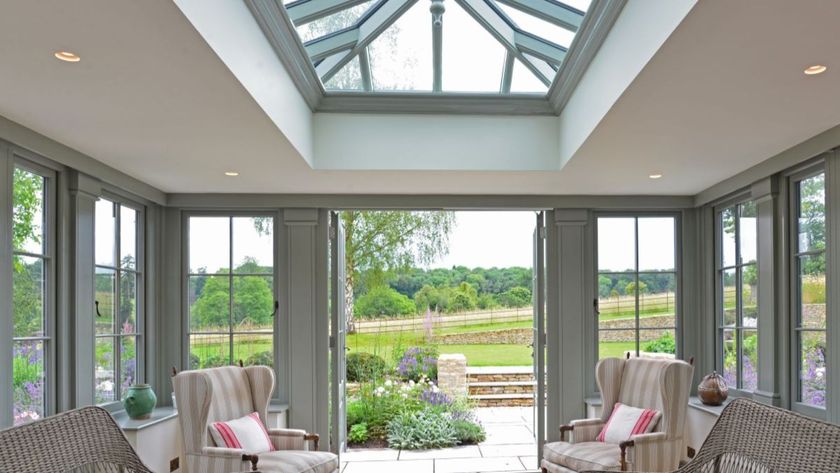