Timber Shortage Eases in Boost for Self Builders and Home Improvers
The timber shortage has brought price hikes and delays, but there is good news as supply increases
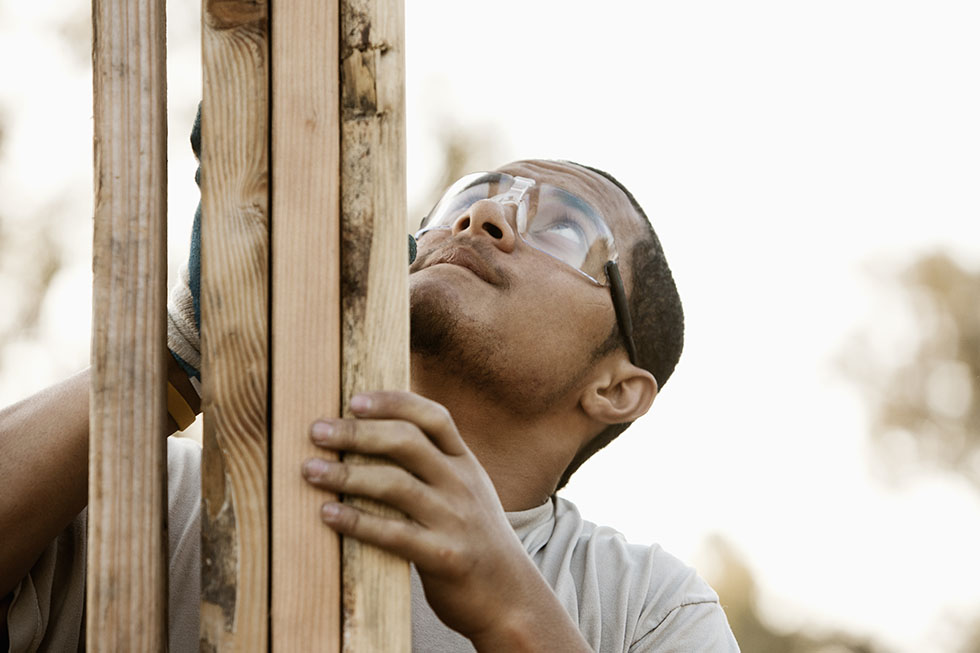
A timber shortage which has frustrated homebuilders all year is "highly likely" to be over, according to the Timber Trade Federation (TTF).
There have been "record-breaking" imports of timber since the beginning of the year, the TTF says, which is extremely positive news for the construction industry. The update will also be welcomed by self builders, renovators, extenders and home improvers who have been impacted all year by the construction materials shortage.
Over seven million cubic metres of softwood timber and panel products were imported by the UK between January and July - roughly two million cubic metres more than the same period in 2020, and half a million m3 above 2019 levels.
This, the TTF says, is nearly two million cubic metres more than in the same period in 2020, and half a million (or 8%) above pre-Covid levels in 2019.
The TTF has warned, however, that challenges remain to ensure builders access timber materials, and that materials shortages continue to be felt across the industry.
Timber Shortage Still Impacted by Driver Shortages
The record-breaking volumes of timber imports this year reflect high demand, but shortages elsewhere of HGV drivers and tradespeople means problems remain in delivering this timber to building sites.
(MORE: 89% of Builders Have to Delay Jobs)
Get the Homebuilding & Renovating Newsletter
Bring your dream home to life with expert advice, how to guides and design inspiration. Sign up for our newsletter and get two free tickets to a Homebuilding & Renovating Show near you.
Nick Boulton, head of technical and trade at TTF, warned: “We are not yet out the woods as any return to ‘regular’ patterns within the UK market will be difficult amidst the ongoing shortage of HGV drivers, and in fuel and labour, which are likely to continue to impact the market in the coming months.
“These shortages are of high concern to the timber supply chain as while there may now be enough timber in the UK to meet demand it does little good to anyone when there are no means to transport stock from ports to warehouses or customers."
Prices Remain High Too
Timber prices have steadily risen over the last year. Imported plywood costs have been particularly affected, surging in price by 81.7% in July compared to July 2020, according to the Department for Business, Energy and Industrial Strategy (BEIS).
And earlier this year, the average price of sawn and planed softwood in May, June and July had yearly increases of 55%, 65% and 88% respectively.
Why has There Been a Timber Shortage?
Timber supplies have been low since the first lockdown in March 2020, with high demand for wood and wood products persisting since the DIY boom last year, a consequence of homeowners spending more time at home due to the pandemic.
But the reasons for timber in particular being impacted are wide-ranging. The UK imports 80% of its timber, and Sweden, which supplies almost half of the structural wood used in the UK, this year recorded its lowest stock levels for 20 years.
There was also a slowdown in production of materials from some factories in the EU in 2020, and Britain leaving the EU lengthened the supply lines for a number of core supplies from Europe.
The TTF said in May that Brexit-related complications squeezed UK timber stocks, as 80% of the softwood used in building comes from Europe, and 90% of the softwood used for new build homes comes from the continent.
Which Timber Materials Have Been Affected?
Supplies of OSB, MDF, P5 chipboard, veneers and solid wood have all been affected throughout the year.
The TTF said earlier this year: “Structural plywoods are also in globally tight supply and likely to remain so, as there is little extra manufacturing capacity that can quickly open up the supply pipeline.
"I-joists and metal web joists are both made using structural timber and panel products, so supplies there too may remain constrained."
How to Navigate Timber Supply Challenges
Problems receiving timber supplies could be significant to those working on self build projects who are building with timber frame, potentially affecting lead times and leading to higher material costs.
Renovators could too be affected by price increases, while some DIY projects may be impacted due to the pressure that some building merchants have been under.
Noble Francis, economics director of the Construction Products Association, says one way of mitigating supply issues - if you’re working with contractors - is to keep open lines of communication regarding the cost and availability of timber products.
“Secondly, plan and order well in advance for future projects months down the line, so you can purchase the key materials which have extended lead times and rising costs,” he added.
Jack has worked in journalism for over a decade and was the former News Editor of Homebuilding & Renovating between 2019 until 2023. In his time as News Editor he broke the most relevant and beneficial stories for self builders, extenders and renovators, including the latest news on the construction materials shortage, planning permission and green initiatives. In 2021 he appeared on BBC's The World at One to discuss the government's planning reforms.
He enjoys testing new tools and gadgets, and having bought his first home in 2013, he has renovated every room and recently finished a garden renovation.