Ultra-low carbon limestone calcined clay LC3 cement used in UK 'for first time'
Architectural company claims to be the first users in the UK of innovative eco-friendly limestone calcined clay cement — known as LC3
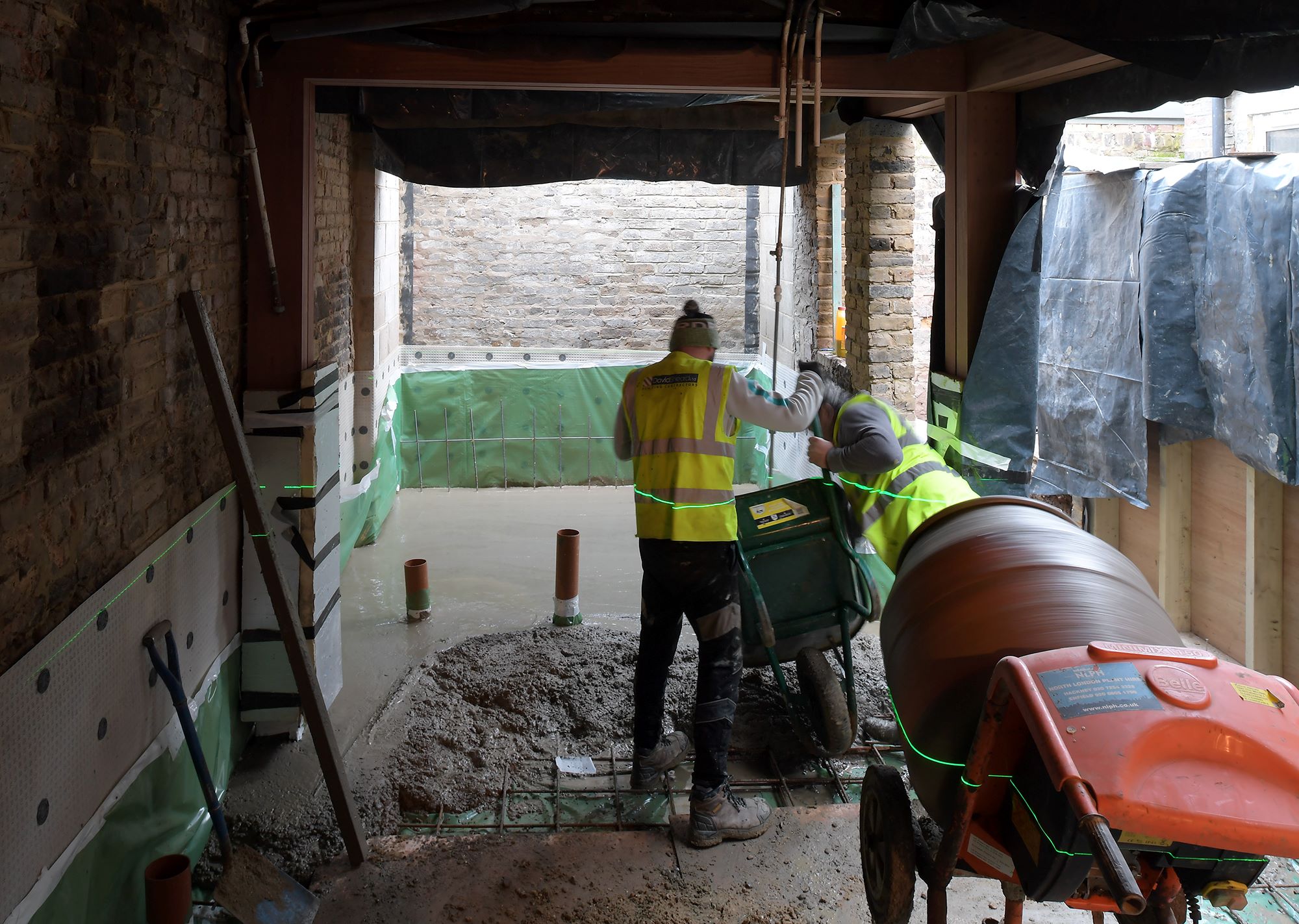
The construction industry is one of the largest emitters of carbon dioxide, accounting for approximately 39% of global energy-related carbon emissions.
As a result, the development of low-carbon building materials is crucial to reducing the amount of embodied carbon in the construction sector.
Embodied carbon is the amount of CO2 produced during the construction of buildings, with building regulations potentially being adjusted in the future in a bid to lower it.
One such material is ultra-low carbon limestone calcined clay cement, which has been used on a building site for, what is believed to be, the first time in the UK.
What is limestone calcined clay cement?
Limestone calcined clay cement (LC3) is a blended cement that incorporates calcined clay and limestone in its production.
The calcination of clay at lower temperatures reduces the energy requirements and emissions associated with traditional cement production.
The inclusion of limestone, a readily available and low-carbon material, further reduces the carbon footprint of the cement by potentially 40%.
Get the Homebuilding & Renovating Newsletter
Bring your dream home to life with expert advice, how to guides and design inspiration. Sign up for our newsletter and get two free tickets to a Homebuilding & Renovating Show near you.
Why does limestone calcined clay cement have a better carbon footprint?
Traditional cement contains large amounts of clinker, which is responsible for most of the CO2 emissions within the cement.
However, limestone calcined clay can half the clinker content of traditional cement, reducing CO2 emissions.
It was very easy to use LC3 in this project. It is no different to standard concrete for the contractors on site, so no extra training is needed
Kieran Hawkins, Cairn
There are other cementitious materials that aim to reduce the carbon footprint of cement products such as Cemfree, however, LC3 differs in a few ways.
LC3 uses limestone and calcined clay as its primary raw materials, while Cemfree is made from ground granulated blast-furnace slag, pulverized fuel ash, and an alkali activator.
Overall, both LC3 and Cemfree are promising alternatives to traditional cement, but they have different raw materials, manufacturing processes, and properties, which may make one more suitable than the other depending on the specific application.
In an interview with Kieran Hawkins, founding director at Cairn, architects who focus on climate-aware clients, stated the reasons why they chose to use LC3:
"The concrete industry account for approximately 8% of global C02 emissions. We need to use much less of it and, where it is unavoidable to use it, we need to minimise the amount of Ordinary Portland Cement — it is the super-heated production of this that generates the most significant volume of C02.
"On other projects we have been able to omit the concrete ground slab altogether and use small steel screw-piles instead."
Does LC3 cement require a different technique?
The use of limestone calcined clay cement does not require a different technique compared to the use of ordinary cement. Despite this, limestone calcined clay cement can actually be used in a wider range of construction applications than traditional cement.
Such applications include mortar production, the creation of tiles and terrazzo for flooring, facilitating the production of precast concrete products, such as pipes, blocks, and panels, and plastering as LC3 can be used in the production of plaster for interior and exterior walls.
However, LC3 may not be suitable for applications that require high-temperature resistance, such as refractory materials, or applications that require high chemical resistance, such as in chemical processing facilities.
LC3 is also a relatively new material, and its availability may be limited in some regions. Hawkins found this to be the case in when using the cement as he claimed:
"The only real negative was the lead-time as we were ordering from Europe. As it becomes more widely available this should stop being an issue."
Is LC3 cement compliant with building regs?
Currently, there are no specific regulations or standards for limestone calcined clay cement (LC3) in the UK. However, LC3 can be used in construction projects in the UK if it meets the relevant British and European standards for cement, concrete, and mortar.
In the UK, the Building Regulations set out the standards for the design and construction of buildings, including the requirements for the materials used in construction. The Building Regulations do not specify the type of cement to be used but instead set out the requirements for the strength and durability of the concrete or mortar.
In summary, LC3 cement can be used in construction projects in the UK if it meets the relevant British and European standards for cement, concrete, and mortar, and if it is used in accordance with the manufacturer's recommendations and guidelines.
Is LC3 cement more expensive to buy?
In addition to reducing the carbon footprint of the cement industry, the use of ultra-low carbon cement also has economic benefits.
The production of LC3 cement requires less energy and produces less waste than traditional cement production.
This results in lower production costs, making LC3 cement a potentially economically viable alternative to traditional cement.
However, as mentioned, due to LC3’s lack of widespread commercial availability prices may vary in different regions. You can go onto LC3’s official website to enquire about its availability.
Hawkins explained how he received his supply from FutureCem: "This was a one-off arrangement with a supplier in Europe. It is not yet available as a standard product in the UK, but we hope it will be soon. This project should help this process by acting as an example of its suitability.
"The costs were slightly more than standard cement, because of the importation. But when it is available directly within the UK there should be very little cost difference."
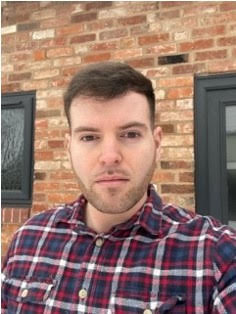
News Editor Joseph has previously written for Today’s Media and Chambers & Partners, focusing on news for conveyancers and industry professionals. Joseph has just started his own self build project, building his own home on his family’s farm with planning permission for a timber frame, three-bedroom house in a one-acre field. The foundation work has already begun and he hopes to have the home built in the next year. Prior to this he renovated his family's home as well as doing several DIY projects, including installing a shower, building sheds, and livestock fences and shelters for the farm’s animals. Outside of homebuilding, Joseph loves rugby and has written for Rugby World, the world’s largest rugby magazine.