How homeowners can get their heat pumps running costs down to only £1.84 a day, according to study
The Energy House 2.0 project has been experimenting with different home setups to achieve the cheapest heat pump running costs
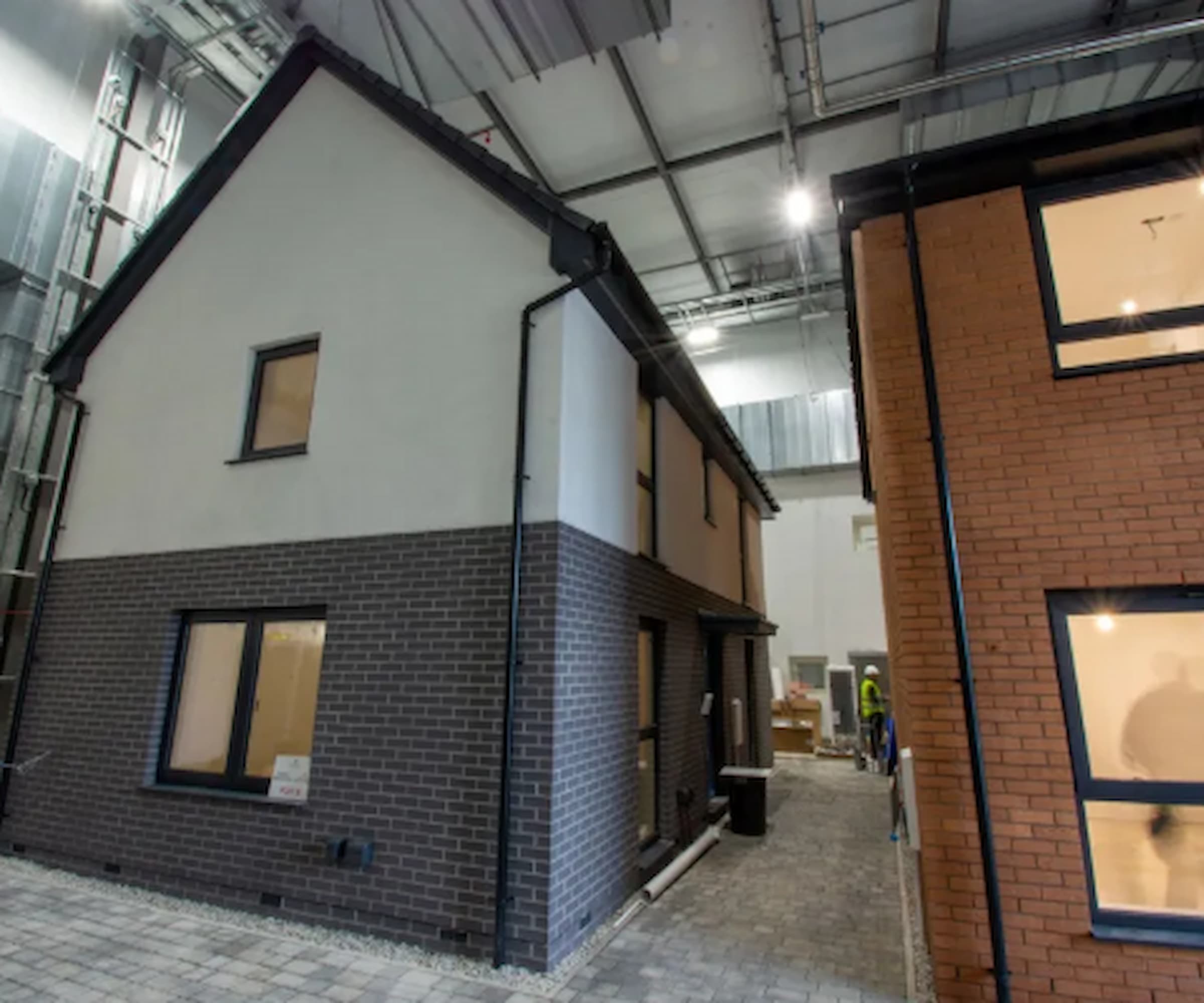
The Energy House 2.0 project at the University of Salford represents the most extensive study on electric heating systems under controlled conditions in the UK – and they've finally released their results.
Researchers have discovered how to get air source heat pump running costs down to a mere £1.84 a day as well as other efficiency improvements.
They did this by setting up two experimental homes – Bellway's "Future Home" and Saint-Gobain’s "eHome2," built in partnership with Barratt Redrow, which were tested inside a state-of-the-art chamber that simulates extreme weather conditions, from -20°C to +40°C.
What heating systems did the study examine?
The research, funded by the UKRI’s Greater Manchester Innovation Accelerator Programme, evaluated 14 heating systems, including air source heat pumps, infrared panels, underfloor heating, and MVHR.
These were tested within Energy House 2.0's chambers, which Homebuilding & Renovating reported on last year that simulated year-round conditions in just weeks.
As Professor Richard Fitton explained: "Without the unique facilities we have here at Salford, it would take years to deliver these results... These insights will be invaluable as we try to reduce the carbon emitted in heating our homes.”
How can homeowners achieve lower heat pump running costs?
The research found air source heat pumps to be highly efficient, capable of heating homes for less than £1.84 per day under typical winter conditions.
Get the Homebuilding & Renovating Newsletter
Bring your dream home to life with expert advice, how to guides and design inspiration. Sign up for our newsletter and get two free tickets to a Homebuilding & Renovating Show near you.
However, it highlighted a need for a behavioural shift in how we use heat pumps, as the study showed electrified systems work best when used continuously, unlike gas boilers designed for short bursts of heat.
Features in the two test homes that achieved the £1.84 a day running costs included improving insulation, airtightness, and window quality to reduce reliance on heating and cooling systems. This "fabric first" approach highlights how optimising a building's materials and structure can give cost savings.
Bellway's "Future Home" was a three-bedroom timber-frame house incorporating two air source heat pumps (including a prototype roof-mounted version), underfloor heating and MVHR, enhanced insulation
Meanwhile, Saint-Gobain's "eHome2" was designed to test next-generation heating, ventilation technologies, and smart systems. The home was built with innovative materials like lightweight off-site construction, weberwall brick, and Pasquill Posi-Joist™ flooring, which supports integrated MVHR systems.
How homes can be built using 75% less carbon
The study also confirmed that meeting the Future Homes Standard (targeting a 75% reduction in carbon emissions for new builds compared to 2013 regulations) is achievable with current technology. Both tested homes performed well, with a performance gap of just 8% between predicted and actual outcomes. This is significantly better than the industry average, where gaps can reach up to 140%.
Professor Richard Fitton of Salford University emphasised: "Without the unique facilities we have here at Salford, it would take years to deliver these results... These insights will be invaluable as we try to reduce the carbon emitted in heating our homes."
Broader implications
This research underscores the importance of innovative design and efficient heating as the UK transitions to net zero housing.
Both homes demonstrated how technologies like ASHPs and enhanced insulation can reduce costs and environmental impact.
These findings provide a blueprint for future homebuilding as gas boilers are phased out from 2025 in new builds and 2035 in existing homes.
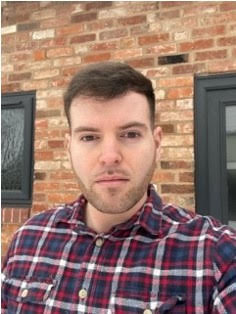
News Editor Joseph has previously written for Today’s Media and Chambers & Partners, focusing on news for conveyancers and industry professionals. Joseph has just started his own self build project, building his own home on his family’s farm with planning permission for a timber frame, three-bedroom house in a one-acre field. The foundation work has already begun and he hopes to have the home built in the next year. Prior to this he renovated his family's home as well as doing several DIY projects, including installing a shower, building sheds, and livestock fences and shelters for the farm’s animals. Outside of homebuilding, Joseph loves rugby and has written for Rugby World, the world’s largest rugby magazine.