3D printed houses to be constructed in the UK for the first time
The first 3D printed house project has begun in the UK which could reduce traditional build costs by 30%, its developers say
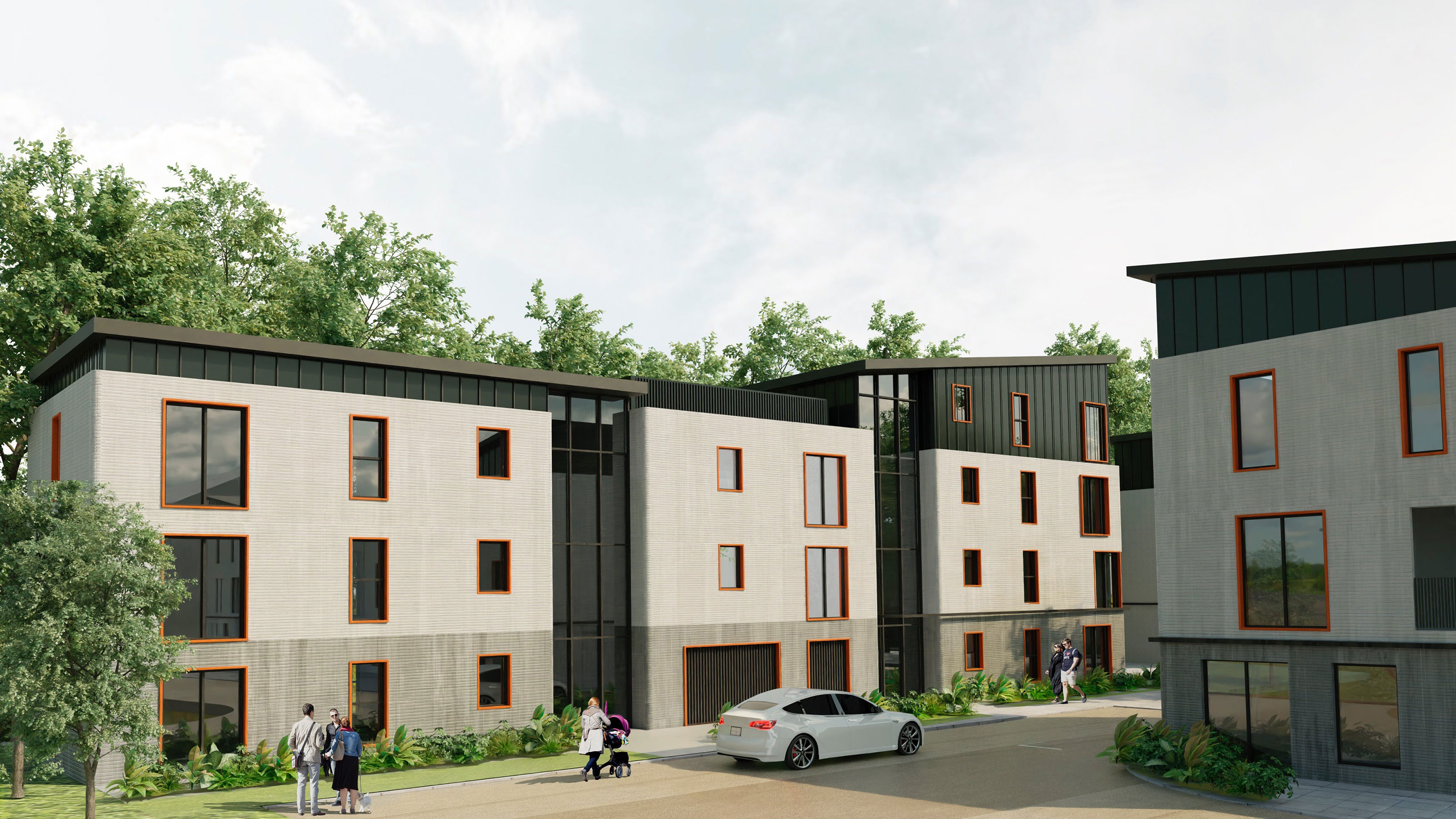
The UK’s first 3D printed houses are being developed, potentially showcasing a low-cost, efficient way of building homes that could revolutionise the construction industry.
3D printing is said to be a quick and efficient building method that is cheaper to than more traditional build routes. It is claimed it could reduce build costs by as much as 30%, according to not-for-profit housing provider Building for Humanity.
Building for Humanity has launched a £6 million project to construct a 3D printed housing estate in the UK.
But how will it stack up? We take a closer look at this project as well as the potential for 3D printed homes in the future.
Where are the UK's first 3D printed houses being built?
In this new £6m project, 46 eco homes will be built to provide homeless people and low-income families in Lancashire with houses. The homes will include a mix of houses and apartments as well as private and communal gardens to help create a local community.
The Building for Humanity project will transform an unused piece of land on Charter Street in Accrington for the homes to be built, that can be printed within weeks. The actual homes will be built by Irish firm Harcourt Technologies (HTL.tech), which is the partner and distributor of COBOD 3DCP technology in the UK and Ireland.
COBOD, short for Construction Of Buildings On Demand, is a world leader in 3D printed houses and buildings, and can reportedly halve lead times on building projects. This will be the first time COBOD is used in a UK residential project.
Get the Homebuilding & Renovating Newsletter
Bring your dream home to life with expert advice, how to guides and design inspiration. Sign up for our newsletter and get two free tickets to a Homebuilding & Renovating Show near you.
How are 3D printed houses made?
3D printed houses can be made in a variety of ways depending on the printer used. Different types of 3D printer include robotic arms, sand printers and gantry systems.
Typically, a blueprint will be created that is sent to the printer. The materials will then be printed layer by layer and distributed to the building site (or printed on site). It is then down to builders to install any additional construction or features; labour is still required to complete 3D printed homes.
In the case of the UK Building for Humanity project in Lancashire, the material used to create the homes will be 3D printed concrete. Recycled materials will be used in the printable concrete mix too; a 40% slag substitution will be used to be more sustainable.
Dr Marchant van den Heever, technical director of HTL.tech, explained to Homebuilding & Renovating that 100% of the printing will be conducted on site, and their gantry-based system – used for larger 3D printing projects – will fabricate the superstructures of the homes, such as the walls and the load-beating elements. The roof, windows and doors will all be built traditionally.
Justin Kinsella, CEO of HTL.tech, said: “HTL’s core objective is to develop the use of 3DCP to create less wasteful and more sustainable building solutions which harness the benefits of advanced manufacturing technology. [We can] provide affordable, higher quality structures, faster and more reliably and in an environmentally beneficial manner.”
This technology is believed to save time compared to conventional construction methods. It can also reduce use of materials and resources.
Will the homes conform to Building Regulations?
HTL.tech is in the process of finalising Building Regulations approval for the homes but, as Dr van den Heever explains, there are varied challenges for obtaining approval.
"This is a new technology; there aren't specific material standards for 3D concrete yet, nor are there specific construction standards for printed concrete. Another challenge is the inherent conservatism within the construction industry, which tends to stick to what it knows."
This is why HTL.tech has plugged into the existing residential construction value chain, utilising CEMEX-certified materials that are synonymous with ready-mix concrete, which Dr van den Heever explains is a "very mature, regulated industry".
The materials will be tested according to the same standards used to test the compression capacity of ready mix concrete. And because the 3D printed concrete will replace concrete blocks in the Charter Street homes, they are using a standard called Eurocode 6 for masonry construction, following these design protocols.
"The only way to breach the market with this new technology is to demonstrate value, firstly, but also competency and comfortable. We had to go through this process because we need to provide high-quality housing at an affordable rate," said Dr van den Heever. "From a technical point of view, we’re ready to deploy."
How could 3D printing impact housing in the UK?
3D printing homes hasn’t yet been widely adopted by UK construction firms, but amid soaring house prices in recent years and first-time buyers finding the housing market unaffordable, something has to be done to increase access to housing.
“3D printing has been around for a number of years and it was always inevitable that we would be looking at the prospect of 3D printed homes as a construction method,” says David Hilton, energy efficiency expert and director of Heat and Energy Ltd.
“I am all for progress and this form of construction will inevitably be a solution for the mass homes market.”
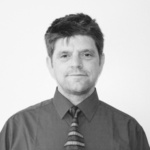
David is a renewables and ventilation installer, with over 35 years experience. He has a Masters degree in Sustainable Architecture, and is an authority in sustainable building and energy efficiency, with extensive knowledge in building fabrics, heat recovery ventilation, renewables, and also conventional heating systems.
Andrew Baddesley-Chappell, CEO of the National Custom & Self Build Association (NaCSBA), believes that 3D printed homes have the potential to address a lack of affordable housing in the UK.
“As the government has long recognised, there is insufficient customer choice in our new homes market which in turn leads to too little competition and too little innovation,” he said.
Commenting on the Charter Street project, Baddesley-Chappell added: “This scheme is yet another example of the opportunities that technology presents to deliver both choice and economy into our new homes market.”
What is the future of 3D printed houses?
There are lots of questions surrounding 3D printed houses, from the use and size of the printers, to the quantity of homes they can realistically build, and how they will be financed.
Dr van den Heever believes that within two or three years there will be many more 3D printed home projects in the UK.
"This is a technology that is there to be scaled. And the benefits will become even more apparent at a scaled output. The key drivers for the construction industry are all there — this type of building is fast, reliable and cheap."
Hilton expects 3D printed homes to gain importance in the coming years, but says that some questions need to be answered before this can happen.
“It is difficult, for example, to know what the expected life of the homes will be, as well as the long-term maintenance requirements. Will the materials be easily recyclable? Also, if a lot of the services and service voids are printed, does this allow for easy maintenance and upgrading? I would like to think that the fabric of the building should outlast the need for significant upgrades.”
As for its use in self build and custom build, which is becoming a more affordable option for people to climb on to the housing ladder since the launch of the Help to Build scheme, Hilton is sceptical.
“It seems the ‘printers’ can be quite large pieces of kit, as such it may not be a viable solution for one-off homes, smaller homes or extensions to existing homes.”
Do similar approaches already exist?
3D printing signals a move towards modular, prefabricated construction. A number of successful off-site prefabricated approaches already exist in the UK to create kit homes (also known as turnkey or package self build). These systems are typically timber based.
Prefabs are built in factory environments before being delivered to site for installation. They are becoming increasingly popular, particularly among custom and self builders.
WikiHouse, meanwhile, is a manufactured building system that uses structural timber and assembles basic building blocks, which can be delivered to site. These can then be assembled by anyone, even if you don’t have any experience of building a home (which can save on labour costs).
Where else has 3D printing been used?
There have been several ‘world-firsts’ in recent years as 3D printing evolves.
In 2020, a world-first construction in Germany in 2020 saw construction company PERI build the country’s first 3D home. It took just five minutes to print one square meter of a double-shelled wall, and the print head, which was pre-programmed by a computer, moved over three axes on a fixed frame and was controlled by just two people.
The home was heated, cooled and ventilated by Viessmann’s high-efficiency Vitocal 200-S air/water heat pump and the Vitovent 300-W ventilation system.
Meanwhile, in a demonstration of how effective 3D printing could be for creating affordable housing, the world’s first 3D printed community was built in Mexico in 2020. The homes were built to enable low-cost housing for some of the country’s poorest communities in Mexico’s Tabasco state.
A 3D printer called Vulcan 2 took about 24 hours to produce each house; it can build two 500-square foot houses concurrently, according to its developers ICON.
And in April 2021, a couple in the Netherlands became the first people in Europe to move into a 3D printed home.
Jack has worked in journalism for over a decade and was the former News Editor of Homebuilding & Renovating between 2019 until 2023. In his time as News Editor he broke the most relevant and beneficial stories for self builders, extenders and renovators, including the latest news on the construction materials shortage, planning permission and green initiatives. In 2021 he appeared on BBC's The World at One to discuss the government's planning reforms.
He enjoys testing new tools and gadgets, and having bought his first home in 2013, he has renovated every room and recently finished a garden renovation.