Internal wall insulation: What are the Pros and Cons?
Internal wall insulation can improve your home's thermal efficiency and reduce your heating bills, however, if it's not specified carefully, it can cause issues too
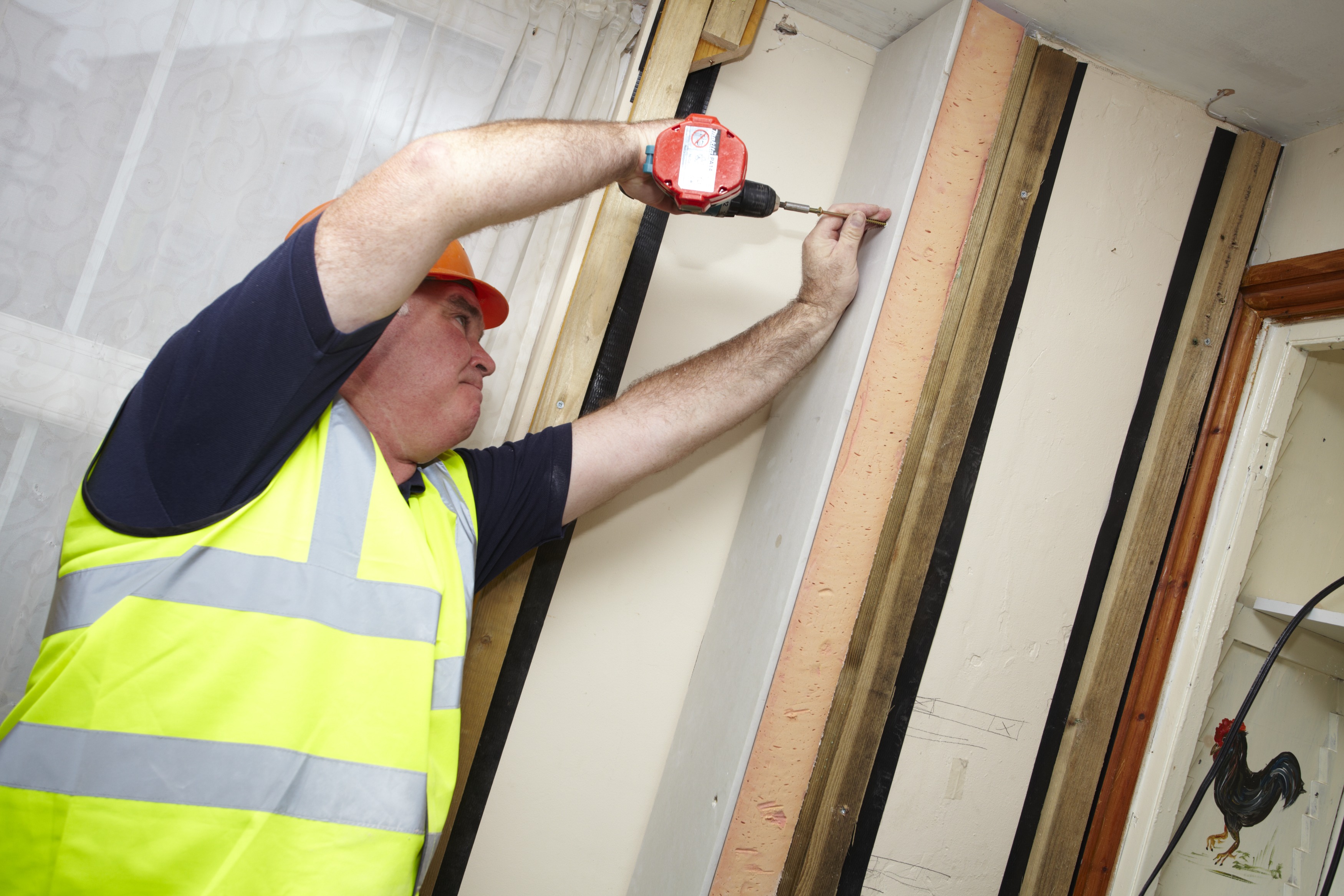
First things first, internal wall insulation is generally only a route to consider for certain homes. Solid wall homes made from solid stone or brick, usually built before the 20th century tend to be the main candidates for this type of insulation.
For houses after this time, there's often a cavity wall as part of the home's construction, offering the opportunity to use cavity wall insulation to improve the thermal efficiency of the fabric of your home.
Your options when it comes to insulation for solid-wall homes extends to both external and internal wall insulation. While the latter tends to be cheaper, it also eats into valuable floor space, making it worth careful consideration.
But it's effect on your home's space isn't the only thing to consider. Internal wall insulation changes the fabric of your home, and can, if not employed properly, cause issues such as damp and condensation.
Here, we explore the pros and cons of this type of insulation, and look at how to make the most of it without creating problems for your home.
What is Internal Wall Insulation?
Need more advice or inspiration for your project? Get two free tickets to the Homebuilding & Renovating Show.
Internal wall insulation involves the application of insulation to the interior face of external walls in order to improve the thermal performance of the property.
There are four main methods of installation — the most common (but not always the most effective) is building a new stud wall, to which insulation can be added.
Internal wall insulation can, however, be disruptive and require the removal and re-fixing of items such as switches, radiators and kitchen units, so you need to be sure it is the best insulation solution for your home.
Creating an airtight layer is vital, so awkward areas, such as reveals and floor voids, require particular care.
How Much Does Internal Wall Insulation Cost?
Up to 60% of the cost of internal wall insulation will be labour. Skimping on the thickness of insulation as a means of reducing the expense of installation is a false economy; the labour cost will remain largely the same whatever thickness of insulation is installed.
The generally accepted cost for internal wall insulation is between £40 and £50/m2 — but it can reach over £100/m2 when a new stud wall is built.
The cost of internal wall insulation will vary according to the type of insulation specified and the condition of the existing wall.
There are grants available for internal wall insulation for solid walls for qualifying households under the government's ECO scheme.
Internal wall insulation is much cheaper than external wall insulation, in some cases less than half the price.
What Building Regulations Apply for Internal Wall Insulation?
The Building Regulations stipulate certain requirements when it comes to airtightness and heat loss that need to be achieved in order for your home to be compliant.
The U-value of a material is the rate at which heat (in watts) is lost through each square meter of the surface. A lower figure means better thermal performance.
- An uninsulated cavity wall will have a U value of around 1.5W/m2 and there will also be a relatively high level of cold bridging due to the cavity ties
- A solid 225mm brick wall will be around 1.9W/m2
- A solid stone wall will be around 1.7W/m2 to 1.4W/m2 (depending on the thickness)
- Current Building Regulations require a maximum U value of 0.3W/m2 and realistically 0.2W/m2. Achieving that U value for solid walls will mean installing at least 100mm of rigid insulation (Celotex, Kingspan or similar)
It has been well established that improving airtightness has a greater impact on heat loss than insulation. The solid elements of the wall will naturally be fairly airtight — but it is the gaps, cracks and penetrations that can be problematic.
These tend to occur as much in awkward places, such as floor/ceiling voids, below the ground floor, the first floor ceiling, as on the accessible areas of the wall. The insulation applied to the wall can form the airtight barrier, but the benefit will be reduced by up to 50% if the gaps, cracks and penetrations are not also dealt with.
Does Internal Wall Insulation Cause Damp?
The dew point is the point where air meets a temperature that causes the moisture to condense out as water. Internal wall insulation will tend to keep the wall at external ambient temperature and thereby draw the dew point towards the internal surface.
If the dew point is too close to the internal surface of the existing wall, moisture can be absorbed by the insulation and appear as damp patches on the plasterboard.
To help prevent damp penetration, a vapour control layer will need to be installed. The internal surface of an insulated wall will tend to be warmer, reducing the likelihood of condensation forming, but there will be areas – such as where an external wall meets an internal wall – that remain cold.
There is a distinct risk of condensation forming in those areas, typically in high-level corners. Overcoming this typically means extending the insulation to cover that cold bridge.
How do I Install Internal Wall Insulation?
There are three basic methods of installing internal wall insulation (and one alternative method which we will also cover), but the process is broadly the same for all three:
- Check the condition of the wall and undertake remedial work
- Ask the preferred insulation manufacturer to check where the dew point will occur with the preferred thickness of insulation
- Decide on which of the three methods will be best (as below)
- Decide how to deal with reveals, floor voids and other potential cold bridges
- Remove everything fixed to the walls to be insulated — plug sockets, light switches, curtain rails, radiators, pipes, skirtings, covings, kitchen cabinets, fitted wardrobes, etc
- Carry out any preparation work to the wall (i.e. knocking off old plaster if damaged)
- Build the new stud wall (if required) and/or fix insulation
- Seal joints and skim plasterboard to finish
- Reinstate light switches, plug sockets, etc
1. Fix insulation directly to the wall
The first option for installation is whereby the insulation is fixed directly to the wall. Kingspan and Celotex offer products specifically designed for this method, with insulation bonded to plasterboard and with a vapour barrier.
If the wall is relatively flat and in good condition, this can be an effective, quick method. Boards can be glued directly to the wall with an adhesive specific for the purpose. Mechanical fixings (screws) can also be used, if necessary. Gaps between boards, at the ceiling and floor edges, should be filled with mastic and taped over before plaster skimming to ensure continuity of the vapour barrier.
Ensuring a continuous, unperforated vapour barrier is the only effective way of dealing with a dew point that occurs in the wall.
These are expensive products, but this is offset to some extent by the speed of installation.
The problem with this method is refixing heavy items such as kitchen cabinets, and hanging pictures, mirrors, etc. Special fixings are available for this but, over time, it can become a headache.
2. Battening the wall
The second option is to batten on the wall. There are two ways of doing this:
- Fixing battens to the wall to provide a more even fixing for the insulation
- Or, fixing the battens over the insulation, known as the ‘warm batten’ method. Both would use 25x50mm battens
The first method is the more common and, when the wall is very uneven, can be the best option. However, the insulation will be rigid and is screwed to the battens, inevitably leading to perforations in the vapour barrier.
The warm batten method is less common but it has some distinct advantages. In this method, a semi-rigid wool batt is placed against the wall. Appropriately spaced battens are placed on top and screws driven through the batten, through the insulation and into the wall.
Rigid or semi-rigid insulation can then be installed between the battens with plasterboard then installed. The advantages the warm batten method offers is that the battens are kept warm by the insulation and so are less likely to rot; the battens are accessible directly below the plasterboard and so pictures can be hung with more ease; and extra battens can be installed to allow heavier items such as kitchen cabinets to be refixed.
3. Construct a new stud wall
Option three involves constructing a new stud wall, generally 100mm thick inside the existing wall, with a 40mm cavity between the two. This option takes up more floor space than the other options.
It is also more expensive and no more effective, except in the case of very damp walls. The cavity between the new stud wall and the existing wall must be ventilated to the exterior so any moisture can be carried away, but this then impacts on airtightness.
4. Apply insulating plaster
There is a fourth internal wall insulation option: applying an insulating plaster directly to the wall.
This is most useful on stone walls, where breathability is important. This would involve either a hemp or cork-lime mix (the hemp or cork providing the insulation) or layers of lime plaster sandwiching a cork or woodfibre board.
This option will not get the desired U-value – typically around 0.5W/m2 is the best you will get – but it has a few distinct advantages:
- It significantly improves airtightness by sealing all the cracks and gaps
- It provides a warm internal surface
- And most importantly, being breathable, it prevents and damp patches
How to Prepare a Wall for Internal Insulation
The condition of the wall’s surface and whether the wall is damp will need to be addressed before installation. The surface condition will determine what preparation work is needed — principally if the old plaster needs hacking off. It will also determine:
- if insulation can be fixed to the wall with adhesive
- whether mechanical fixing will be needed
- if battening is necessary to give a flat surface
Insulation can make a damp wall worse by reducing the temperature of the wall and by reducing (or eliminating) air movement across its internal surface.
There are only two ways of dealing with a damp wall: creating a stud wall with a cavity between the insulation and the existing wall, or finding the cause of the damp and eradicating it.
When it comes to the latter, if you believe that rising damp is a myth, then options other than installing a damp-proof course need to be explored. Damp could be caused by rain penetration through the wall itself — in which case internal insulation would be a mistake. It might be a leaky gutter, downpipe or overflow, which is easy to fix. It could be that the external ground levels have been built up above those of the interior wall levels.
What Kind of Insulation Should I use for Interior Walls?
What is most suitable will vary with the application, and a bit of research will be needed to find the best solution for your home.
- Rigid foam boards of insulation (such as Kingspan or Celotex) are better insulators than the alternatives and so they are thinner and take up less floor area. They can also incorporate a vapour barrier. But they are more expensive and might not tick breathability boxes on your checklist.
- Mineral wools such as Rockwool or Knauf are widely used. These tend to be available as semi-rigid batts or quilts.
- Natural materials such as sheep’s wool, woodfibre insulation or cork (try Ty Mawr) are good options for people looking for good levels of breathability and those interested in the eco-credentials of a product. Natural materials do not ‘gas-off’ (release toxins) either.
- Thin insulation: It is the floor voids, reveals and returns that need particular attention to ensure continuity in the insulation and eliminate cold bridges. Generally, thinner materials are needed here and there is a selection available — from paints such as Therma-Coat Acrylic Insulating Primer to aerogels like Spacetherm.
Is it Worth Insulating Internal Walls?
Internal wall insulation presents its own set of problems. It is cheaper than external wall insulation – up to 50% less – but less effective, potentially more problematic and more disruptive, certainly if the house is being occupied while the work is going on.
Perhaps the way to look at it is that it is better than doing nothing and it has a better payback than external wall insulation, which possibly makes it worthwhile overcoming the problems it presents.
Pros:
- It is cheaper than external wall insulation (up to 50% less)
- It might be the only option if you can not insulate externally (if you are in a conservation area for example)
- There are options where breathability is a concern
Cons:
- It is less effective than external wall insulation
- It is more likely to cause damp problems (so needs careful planning)
- You will lose internal floor area
- It is a more disruptive process (you may need to move out of the rooms being worked on)
How Much Floor Space Will I Use With Internal Wall Insulation?
The thickness of internal wall insulation varies from brand to brand, but you can expect it to be anywhere from 60mm to 100mm — largely, the more expensive the insulation, the thinner its profile. You should expect to lose at least 100mm on each wall when insulating interior walls.
Get the Homebuilding & Renovating Newsletter
Bring your dream home to life with expert advice, how to guides and design inspiration. Sign up for our newsletter and get two free tickets to a Homebuilding & Renovating Show near you.
Tim is an expert in sustainable building methods and energy efficiency in residential homes and writes on the subject for magazines and national newspapers. He is the author of The Sustainable Building Bible, Simply Sustainable Homes and Anaerobic Digestion - Making Biogas - Making Energy: The Earthscan Expert Guide.
His interest in renewable energy and sustainability was first inspired by visits to the Royal Festival Hall heat pump and the Edmonton heat-from-waste projects. In 1979
this initial burst of enthusiasm lead to him trying (and failing) to build a biogas digester to convert pig manure into fuel, at a Kent oast-house, his first conversion project.
Moving in 2002 to a small-holding in South Wales, providing as it did access to a wider range of natural resources, fanned his enthusiasm for sustainability. He went on to install renewable technology at the property, including biomass boiler and wind turbine.
He formally ran energy efficiency consultancy WeatherWorks and was a speaker and expert at the Homebuilding & Renovating Shows across the country.