Take a tour of this stunning eco home built for £1,200m2
Ed Humphreys and Emily Hurter took on almost every aspect of their project, building an impressive home on a modest budget
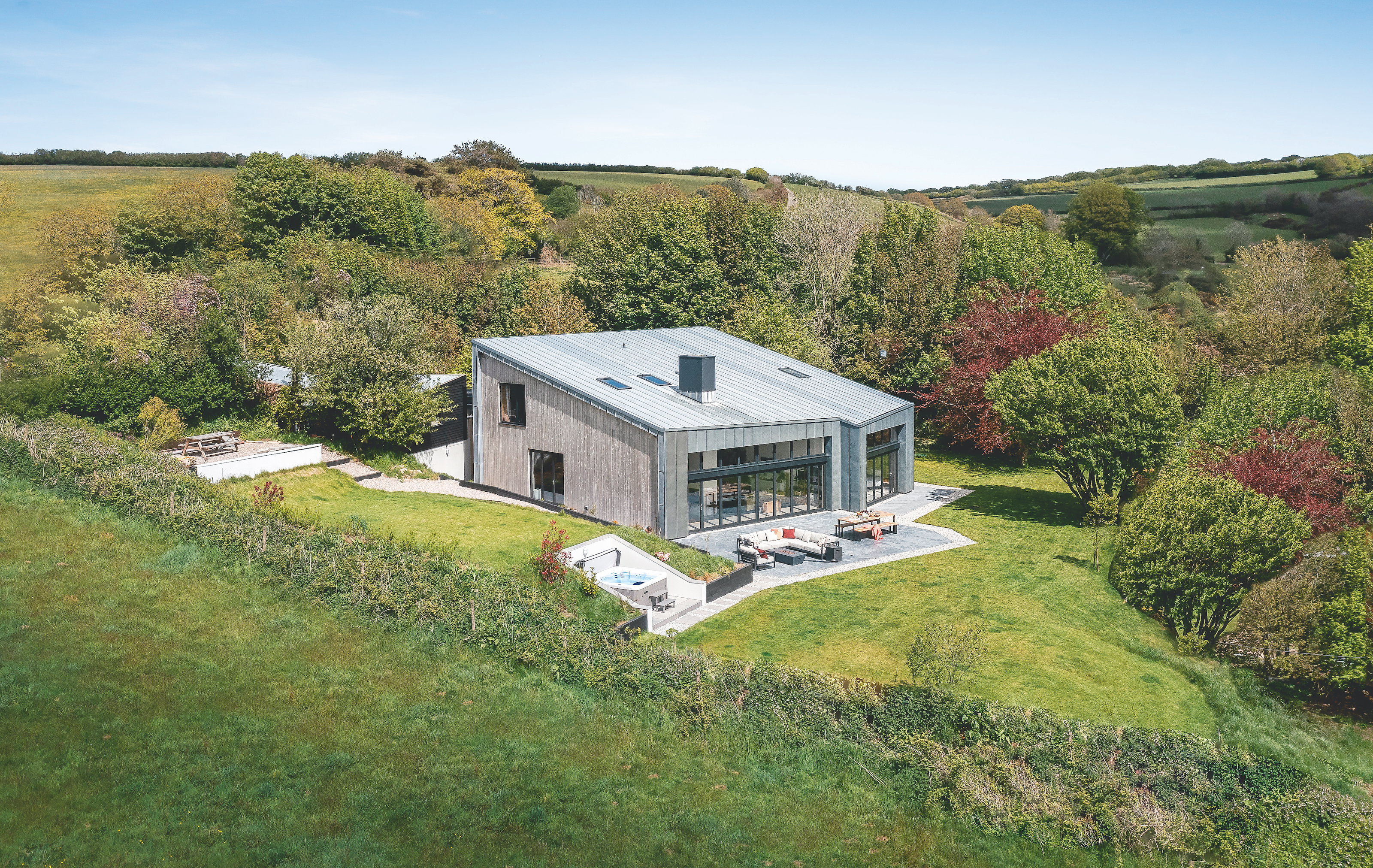
Who can pinpoint the very first moment of a self-build? Ed Humphreys and Emily Hurter met as young children in the garden where their house now stands — and were adults before they met again at a family dinner.
A few years later, they bought that same garden with the aim of taking on a self build project together.
The catalyst for the build was a decision by Ed’s parents to move overseas and sell off their former garden, which already had planning permission for a retirement property.
Here the couple explain how they created this unique property on an impressive budget.
Designing a home from scratch
From the beginning of the project, Ed and Emily were very involved, and took a hands-on approach.“We did all the design work ourselves,” says Emily. “We taught ourselves to use Sketch-Up and created the 3D renders together, then hired an architectural technician to convert our designs into technical drawings.”
Ed and Emily designed a four-bedroom contemporary home with an impressive eight-metre span of glazing to make the most of the beautiful Exmoor setting. Although different from the already-approved designs, the couple’s plans gained planning permission without significant problems. “We wanted something modern, but which uses textures and materials that complement the building’s rural surroundings,” says Emily.
“We tried to get the most house for the money we had,” explains Ed. “Our architectural fees were just £1,500, not the £10,000 we were quoted.” Emily also enjoyed retaining control of the design. “The design process was our favourite bit,” she says.
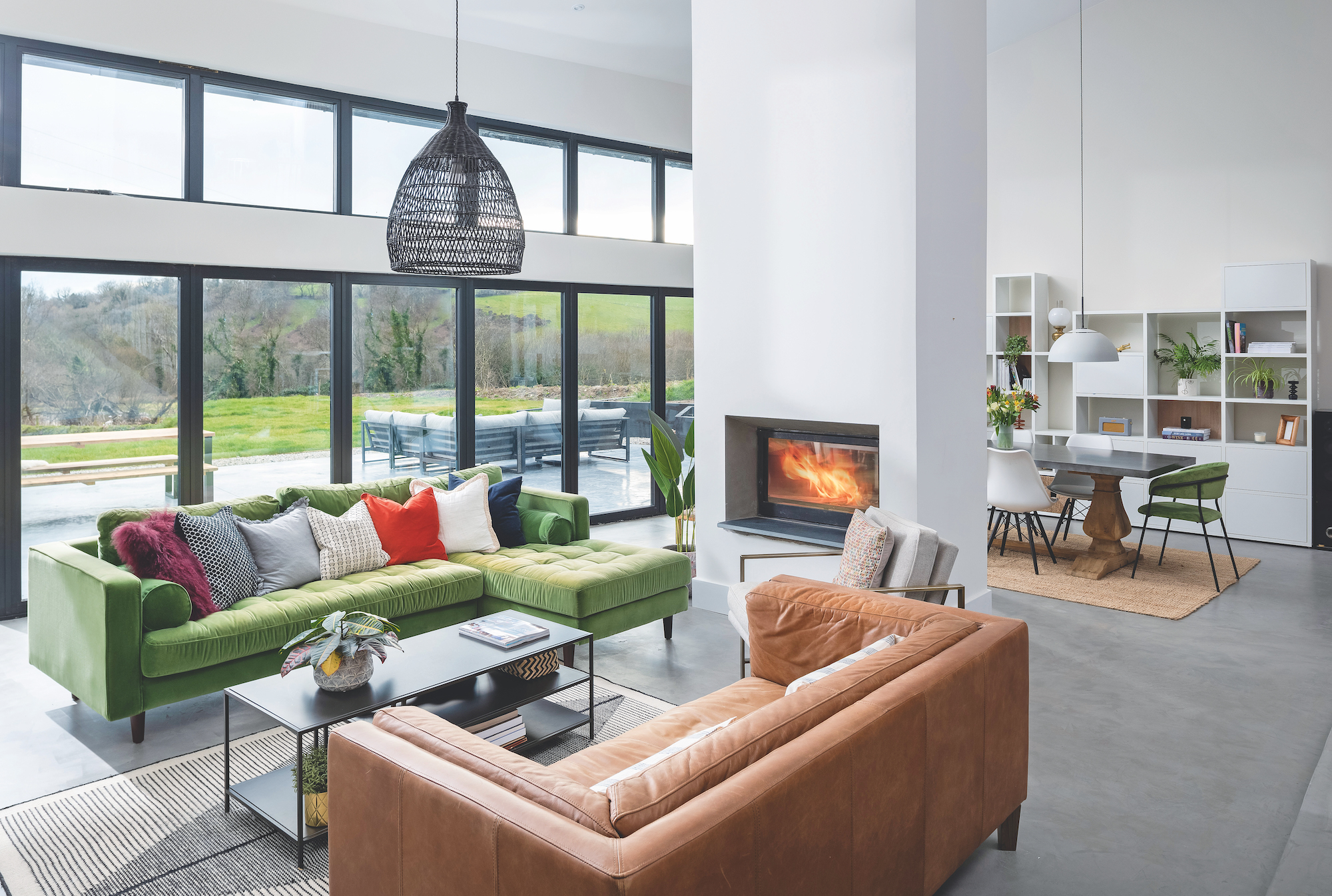
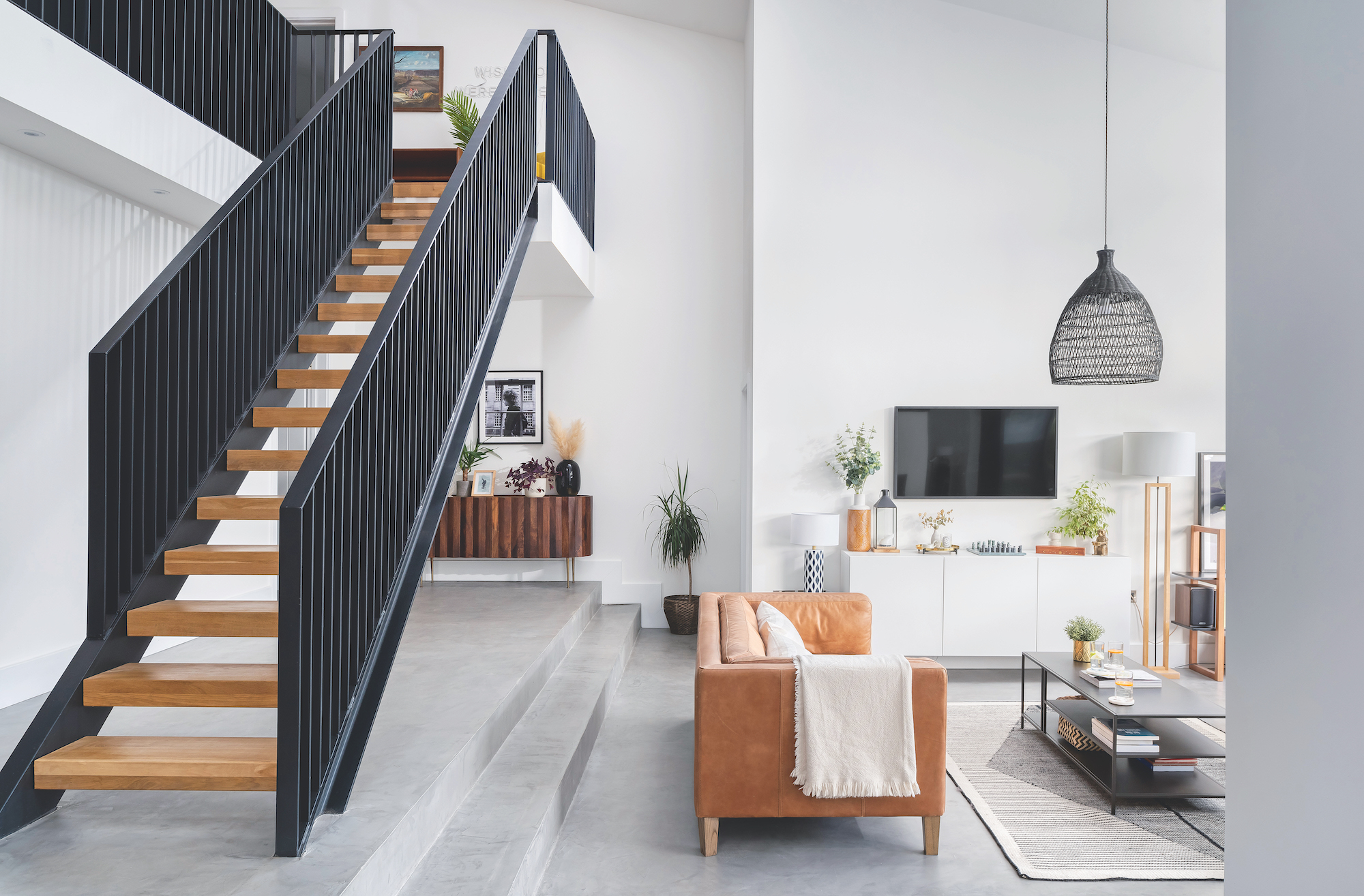
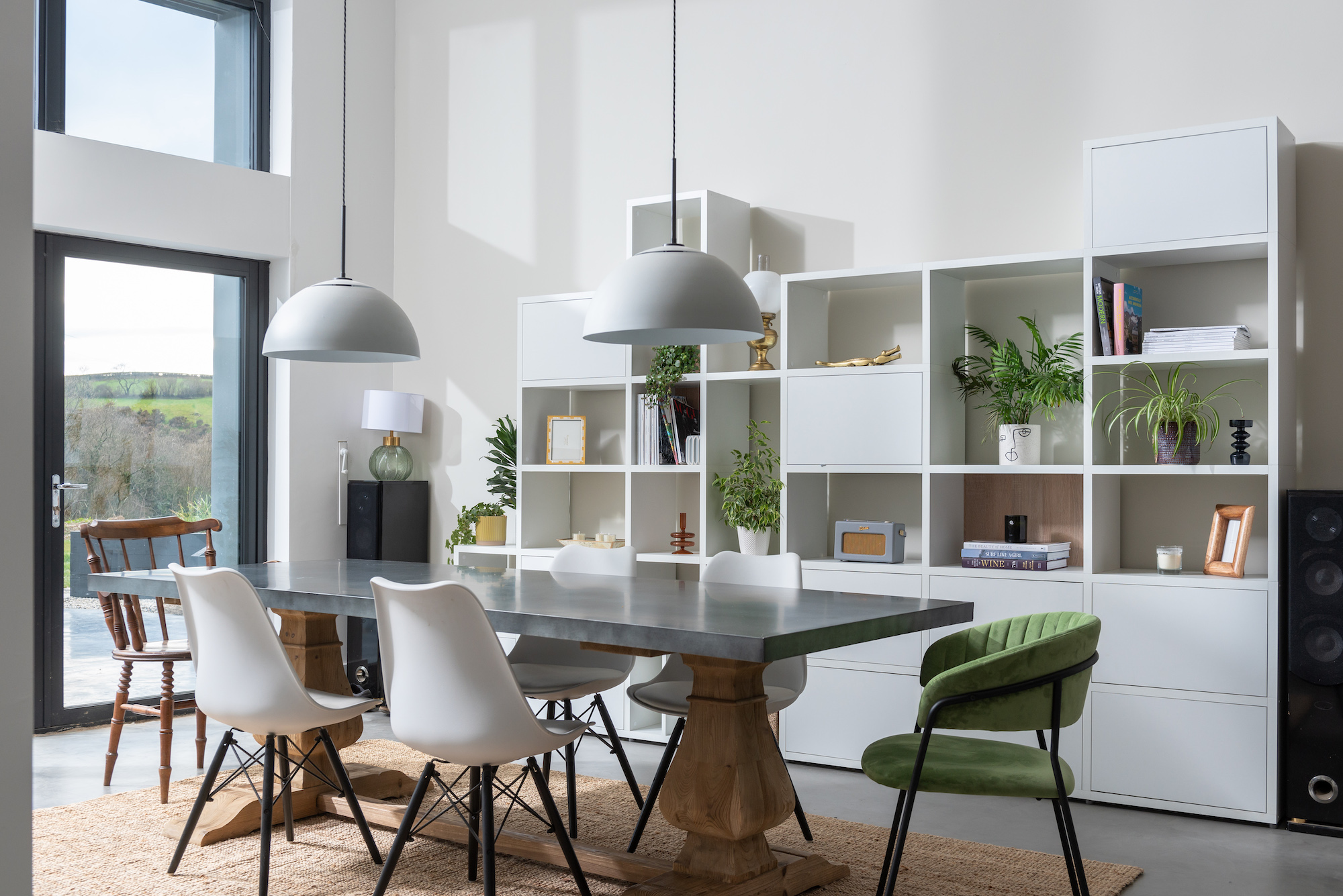
Balancing budget with green credentials
The couple chose to build using timber frame construction, with steels above the bifold windows in the living room and master bedroom.
For them, timber frame was the more cost-effective option, but it also offered environmental benefits, especially as it was ‘super insulated’ with Celotex. “We tried to get close to Passivhaus standards, while staying cost-effective,” explains Ed. “It’s a bell curve and those last few per cent cost disproportionately more.
It really has worked, though, and the building maintains such a stable temperature, despite being 5.5m high at the apex.” Cooling was also a priority for Ed and Emily, given the potential for passive solar gain.
The couple solved this by creating a ‘convection loop’. Three electric Velux rooflights at the tallest point in the main living space suck in cool air from the windows and expel the hot air, making the temperature drop. “We didn’t realise just how effective it would be,” says Emily. “It’s very comfortable.”
Getting stuck into DIY
Ed and Emily had a head start with the project, as they rented Ed’s old family home during the build, staying onsite without needing to hire a caravan. Ed, a trained carpenter, built full-time while Emily worked locally. Emily’s younger brother, James Hurter, who sadly died last year, worked extensively on the project using his professional joinery skills.
With guidance from his mentor and former employer, Ed tackled the groundworks himself, pouring the slab in two sections to create a stepped foundation. He also spent a week at a local sawmill, pushing planks of European cedar through a planer, creating tongue-and-groove cladding boards in a ratio of two wide to one narrow. “The eye doesn’t pick up the pattern,” Ed says. “It just looks irregular.”
The DIY element didn’t end with the structures. One of the most important features is the staircase, which the couple designed themselves. Having also done the calculations, they bolted the stringers into the subfloor and welded them onto a steel beam to create a cantilevered landing area.
Although Ed taught himself to weld, the job was taking some time, so he handed it over to a friend who works as a metal fabricator. Ed then turned to the ‘floating’ timber treads, each of which required a ‘lip’ to meet Building Regulations on gaps.
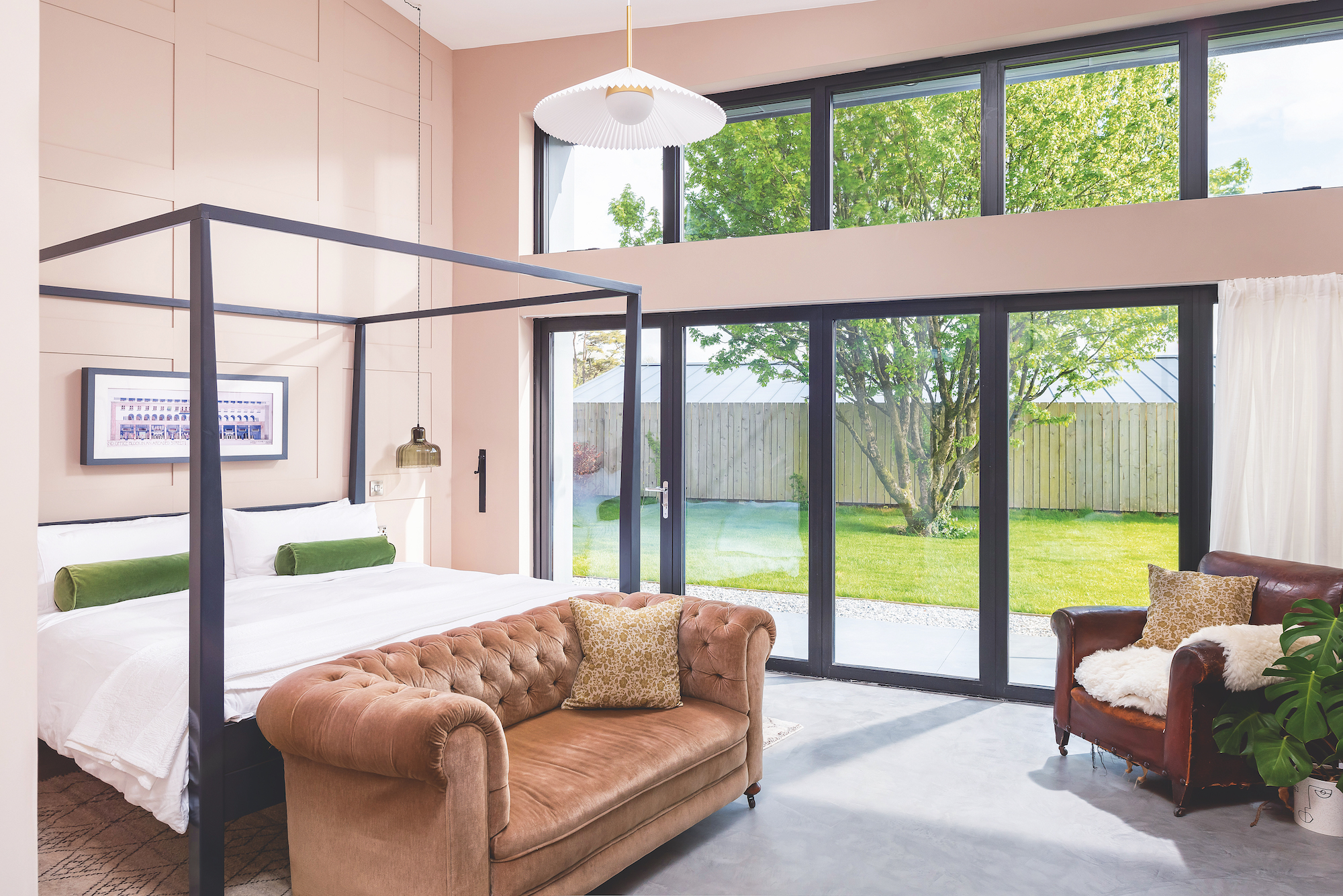
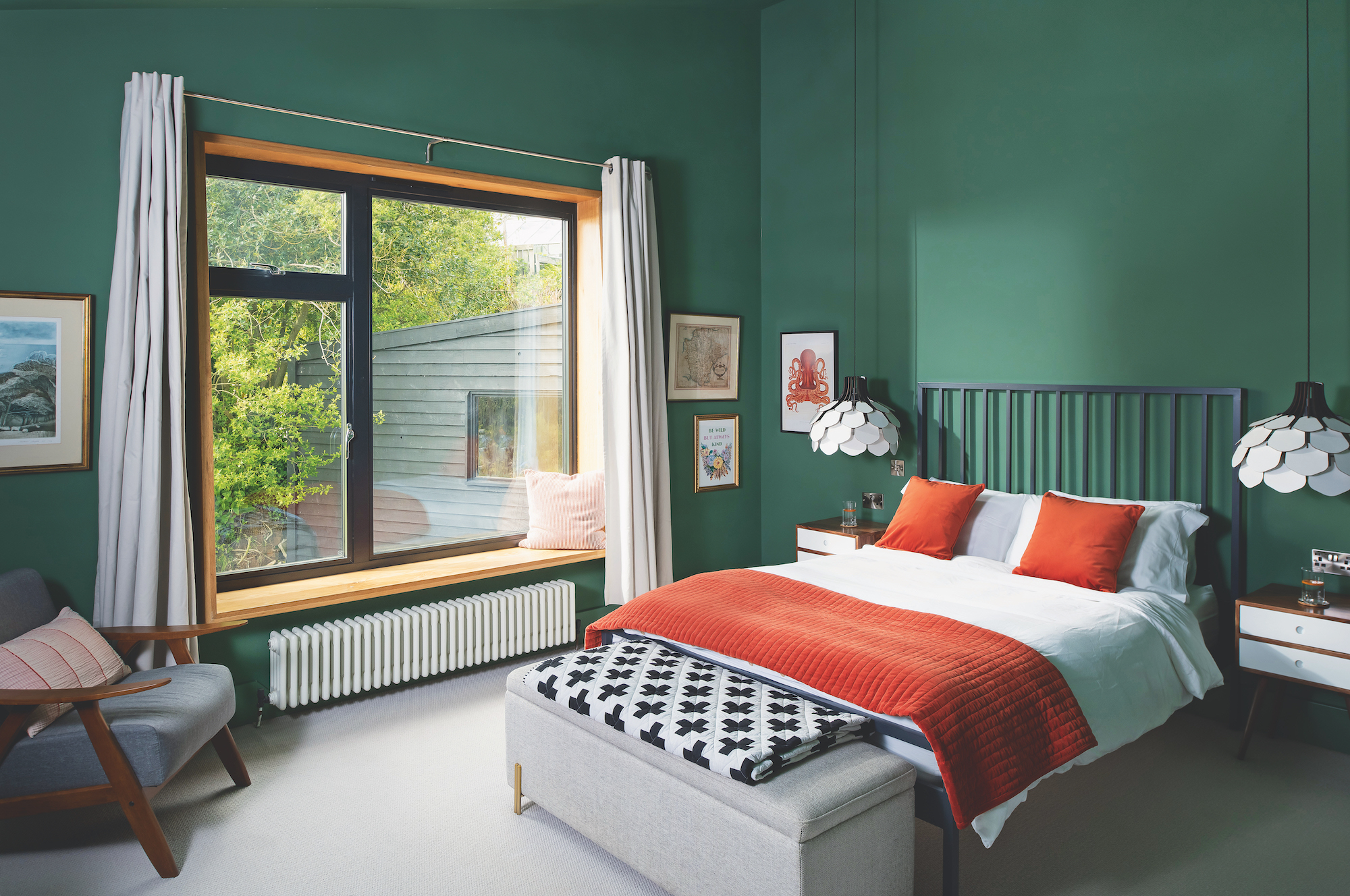
Dealing with on-site challenges
Inevitably, the build threw up some challenges. “A lot of jobs became a lot more work than we anticipated,” admits Ed. One such job was the polished concrete patio. “The weather was a lot hotter than forecast and it was such a stressful day,” he says. “The concrete was going hard before I could flatten it.”
The impressive aluminium bifold doors also caused problems when it became apparent there was a leak. Cutting back their newly laid floor, Ed discovered a problem was the fitting which was allowing substantial water ingress. With the window fitting company in administration, he stopped the leak with waterproof adhesive and remade the floor using an area of tiling, which now appears as a design feature.
Ed says, reflecting on the build and the resulting home: “Don’t compromise on your design or the details. No one cares as much about your build as you do. I love the main living space; it works so well and it’s warm and cosy. It just works.”
The property is presently available for short-term let through Unique Homestays.
Get the Homebuilding & Renovating Newsletter
Bring your dream home to life with expert advice, how to guides and design inspiration. Sign up for our newsletter and get two free tickets to a Homebuilding & Renovating Show near you.
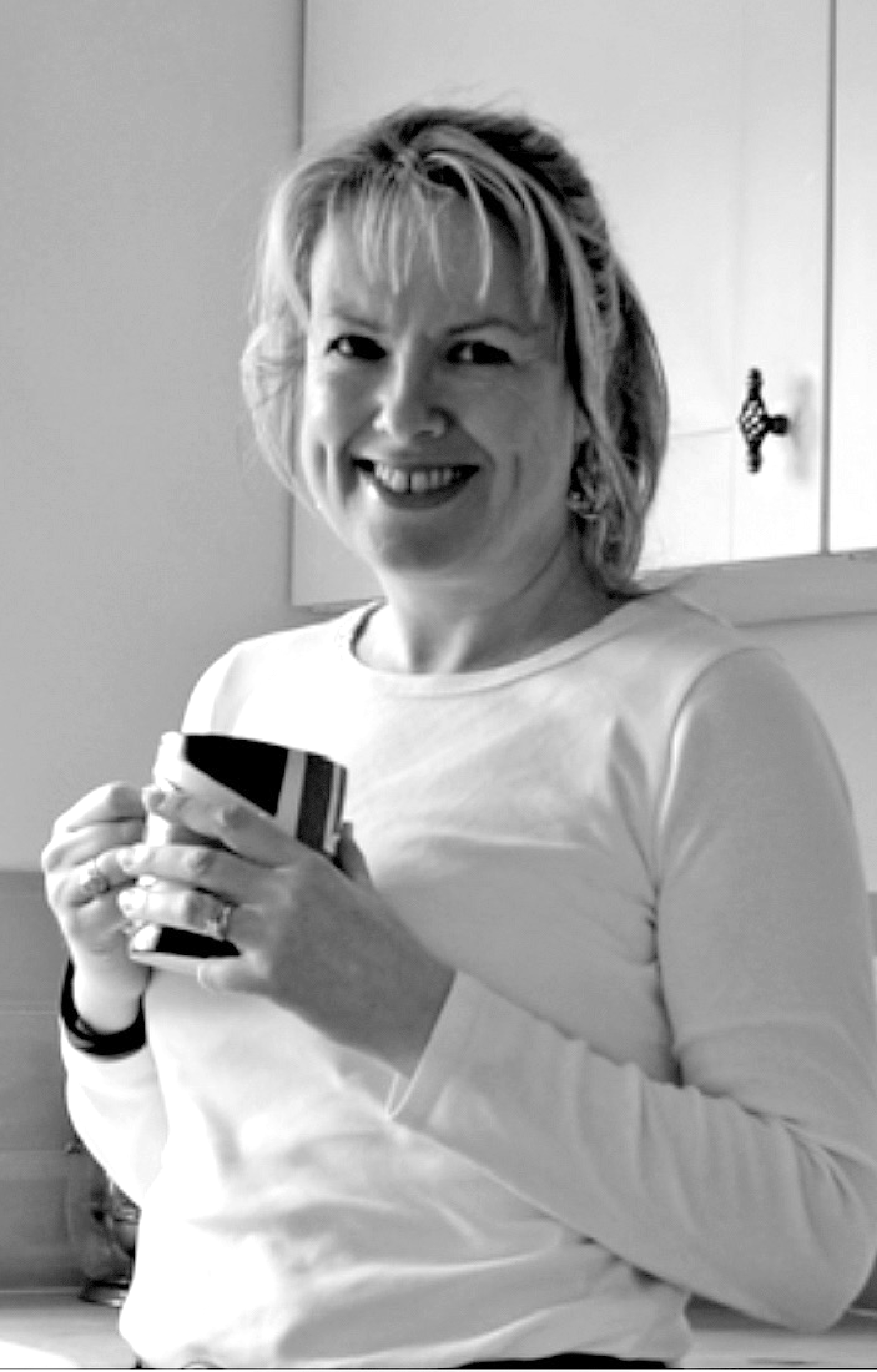
Alexandra Pratt is a home journalist with over 20 years experience, who has written for a number of self build titles. She has interviewed countless architects and self builders.
She is also a serial renovator and has been overhauling properties for over 15 years, and has built her way up the property ladder by undertaking DIY, living on site and project managing her own renovation and self build projects.