How this couple transformed a derelict stone barn into a stunning Passivhaus — and no longer pay energy bills
Paul and Sonny Shepherd waved goodbye to high energy bills after converting a barn to EnerPHit Passivhaus standard
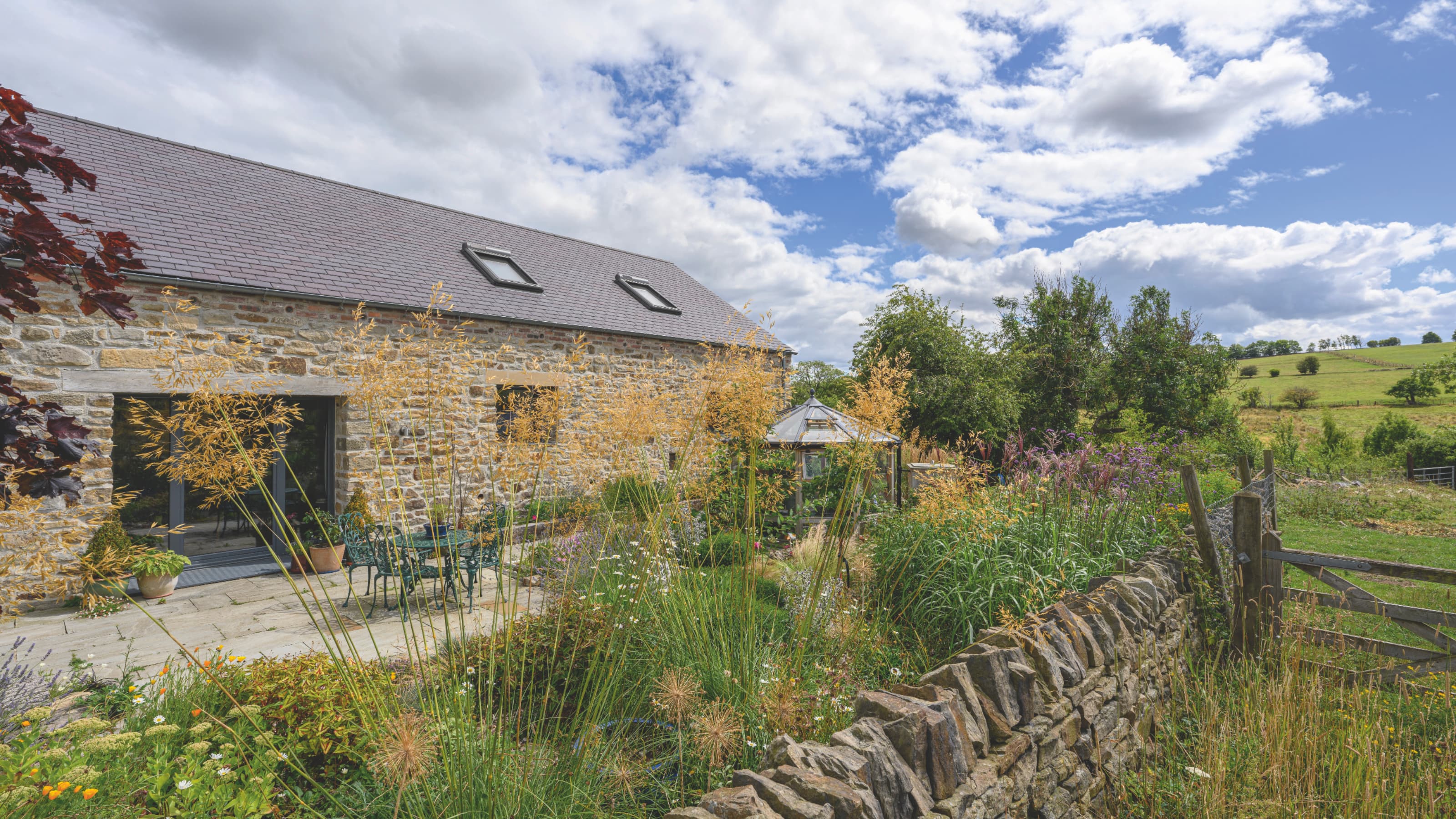
Some of the best projects can be years in the making. That was certainly what Paul and Sonny Shepherd found, having bought two hectares of land, along with two barns, 12 years ago.
Converting the first barn taught them valuable lessons as first-time self-builders. But it was through the conversion of the second barn that they were able to realise their ambitious eco-friendly dreams.
Here's their story about how they created the impressive build, plus how they pushed it one step further to make the Passivhaus EnerPHit standard, meaning they could eliminate energy bills altogether.
Choosing to project manage the Passivhaus build
“We were becoming increasingly concerned about climate change, so we started to find out about converting our second barn as a Passivhaus project,” explains Paul, a retired GP. “We went along to see Steel Farm [a Passivhaus project led by architect Mark Siddall] and realised we didn’t know what we were doing! So we decided to appoint Mark and take ourselves on a two-day training course with Passivhaus Training.”
Fired with enthusiasm, the couple decided to take on the project management themselves. “We were two people with no building experience and we learnt enough to convert our barn to Passivhaus certification — it isn’t rocket science,” says Paul. “But it does need attention to detail, and not many tradespeople know about this approach.”
Rebuilding the barn with sustainability in mind
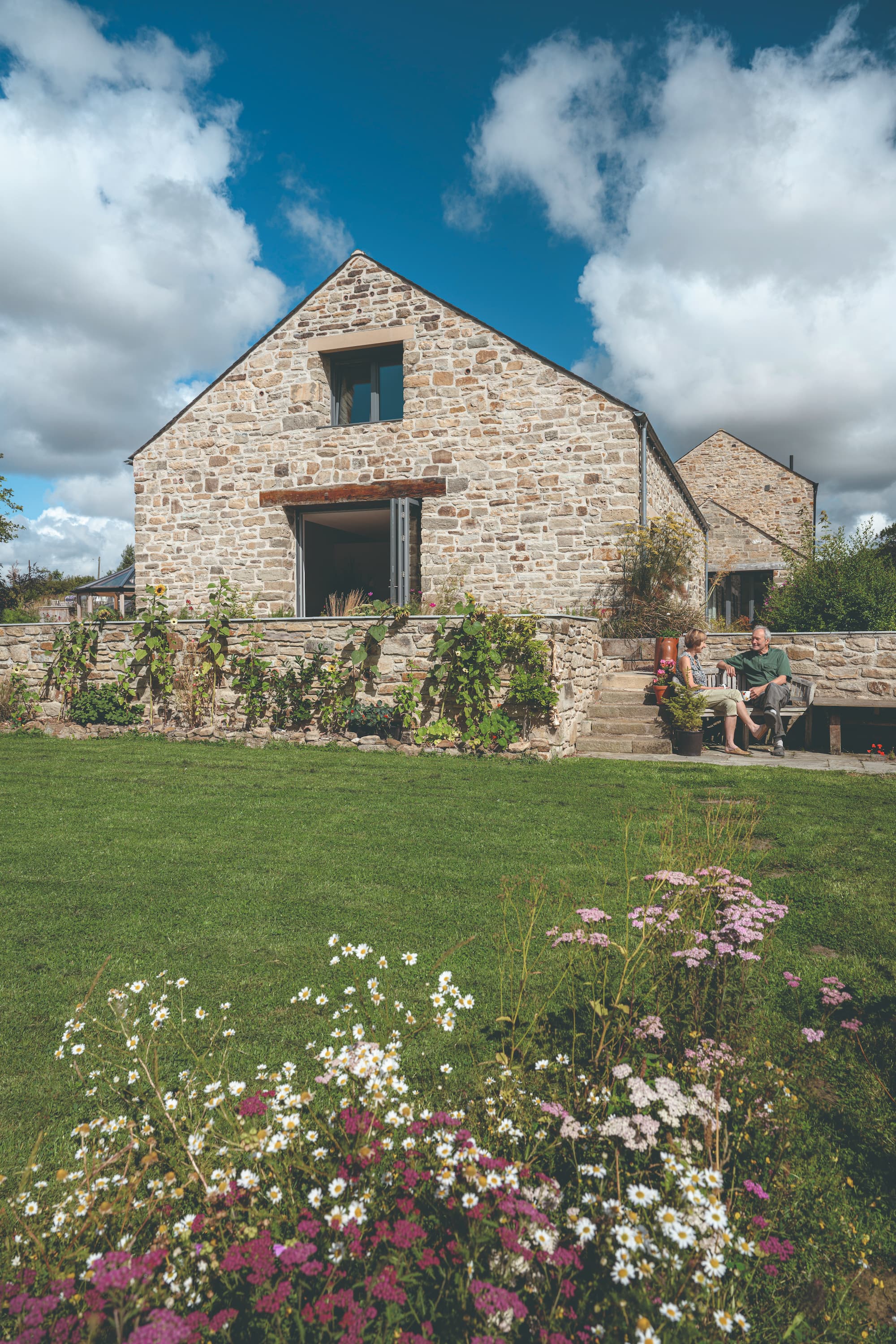
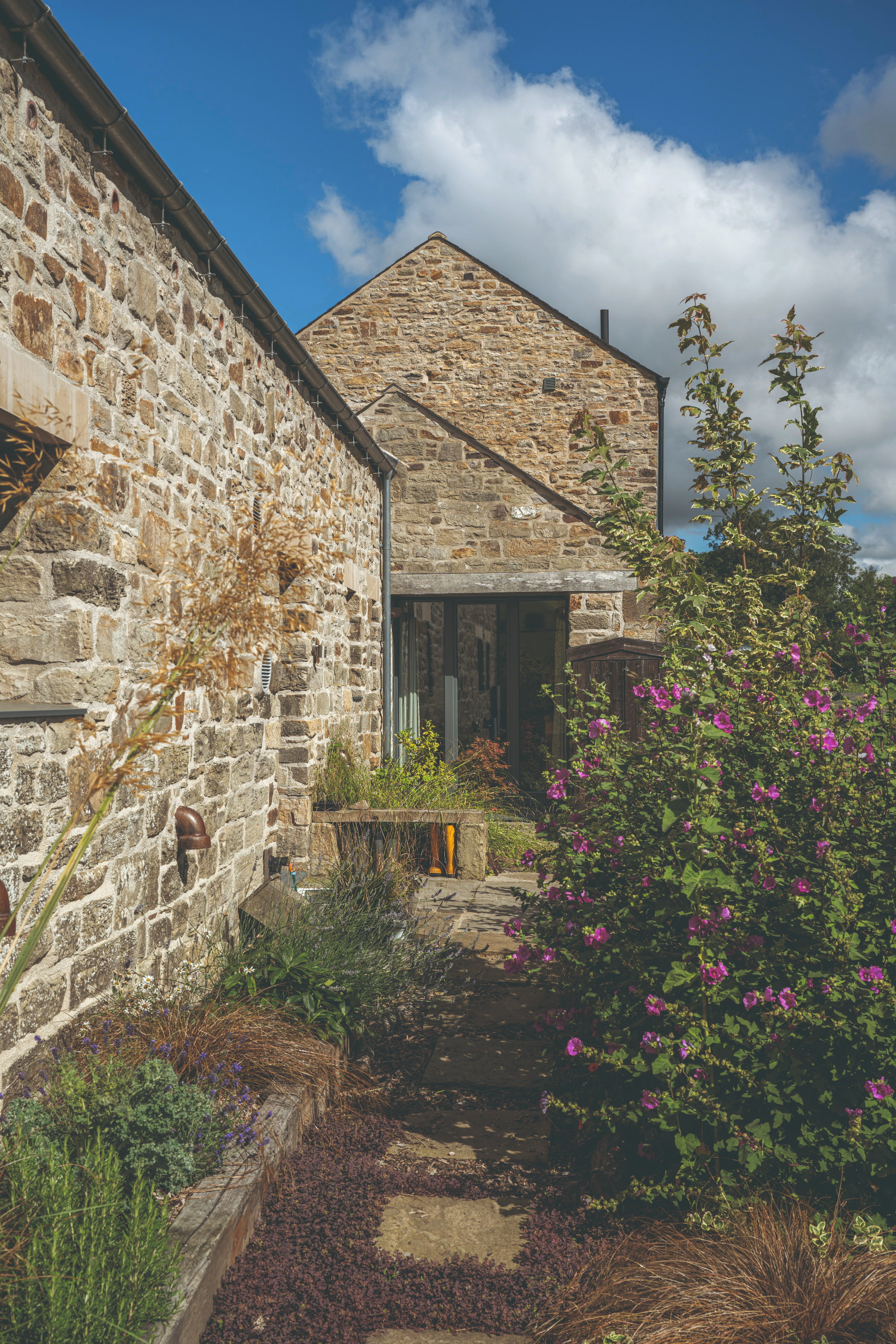
With the stone-built barn in danger of falling down, around 70 per cent of the structure had to be removed. “It looked like a medieval ruin,” says Paul. “Some stone walls had to be taken down to the ground, while others could be partly retained. We had to put the building back to look like the original barn, as stipulated by the planners.”
To create a habitable fabric first structure, an airtight timber frame, prefabricated in a factory and pre-filled with cellulose insulation, was craned in, lowered into position, and sealed with airtightness products to seal it completely. “The frame was erected in just five days,” recalls Paul.
The couple took on around 40 per cent of the physical work, preparing the site, removing the roof, putting in the insulation, tackling the internal decor and even fitting all the airtightness membranes, tapes and grommets themselves — one of the most critical elements of any amazing Passivhaus home. “It took us exactly one year, working eight to 10 hours a day, six days a week,” says Paul. “A Passivhaus retrofit is harder than building from scratch as you have to work with an irregularly shaped external shell.”
Future-proofing with an accessible interior
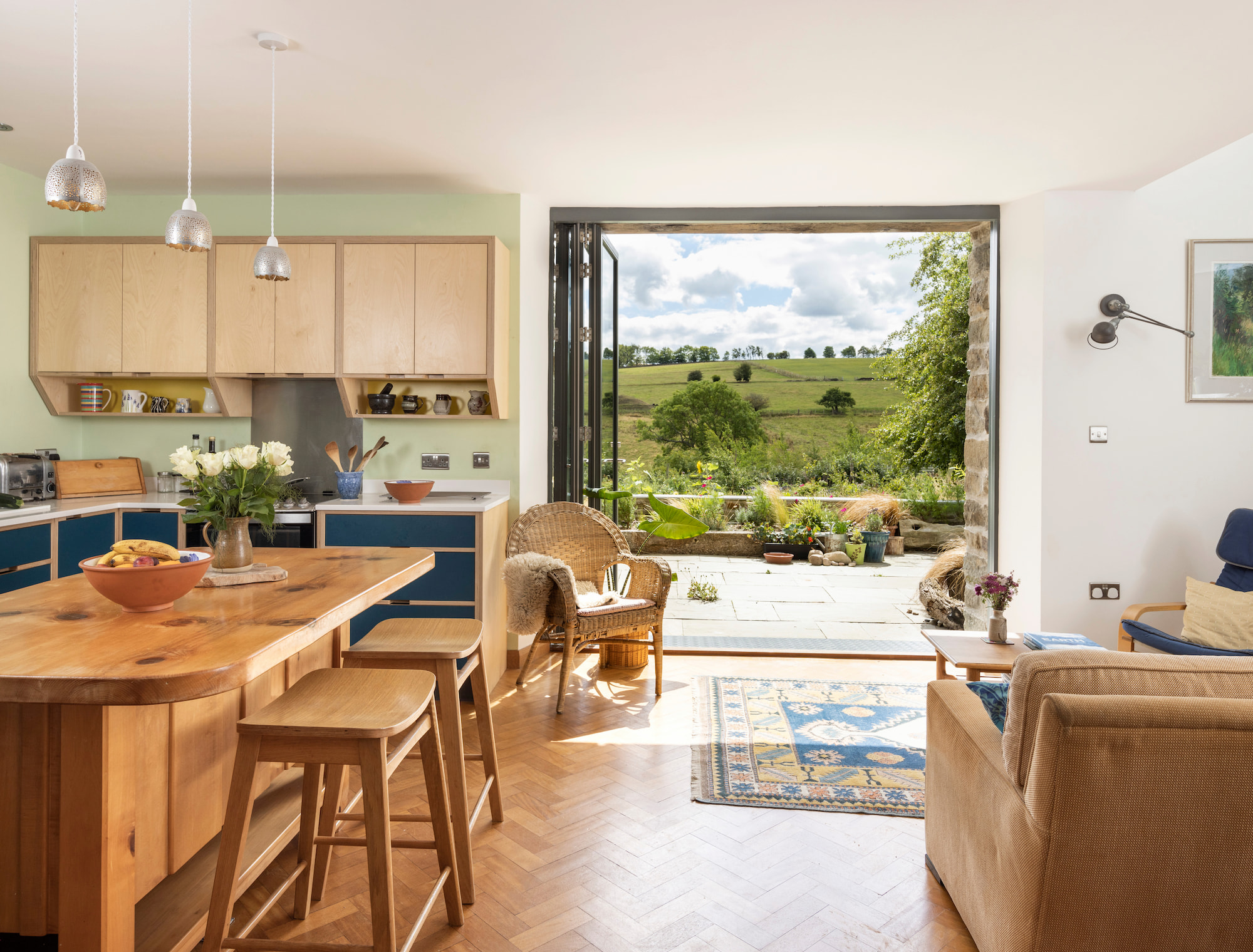
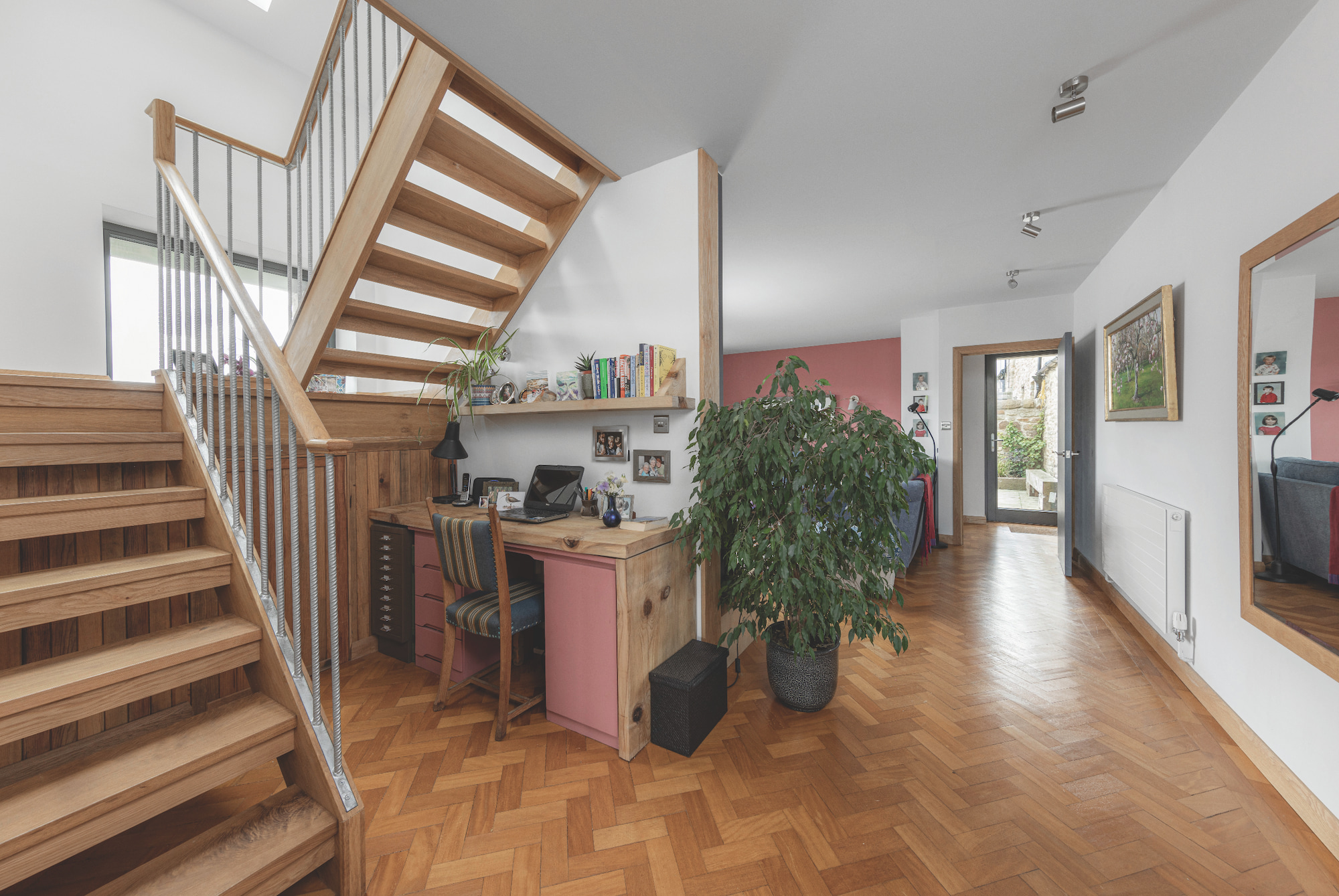
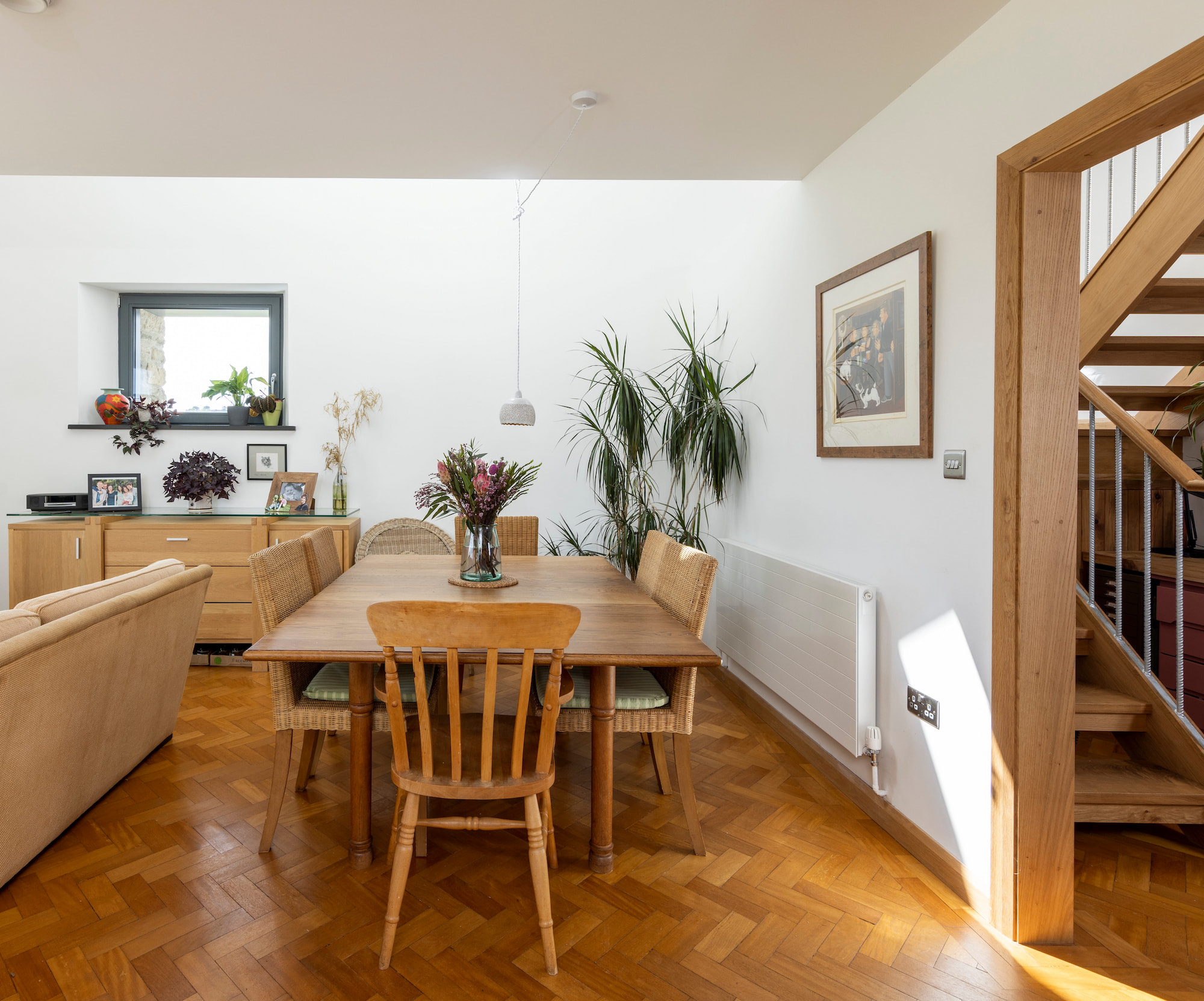
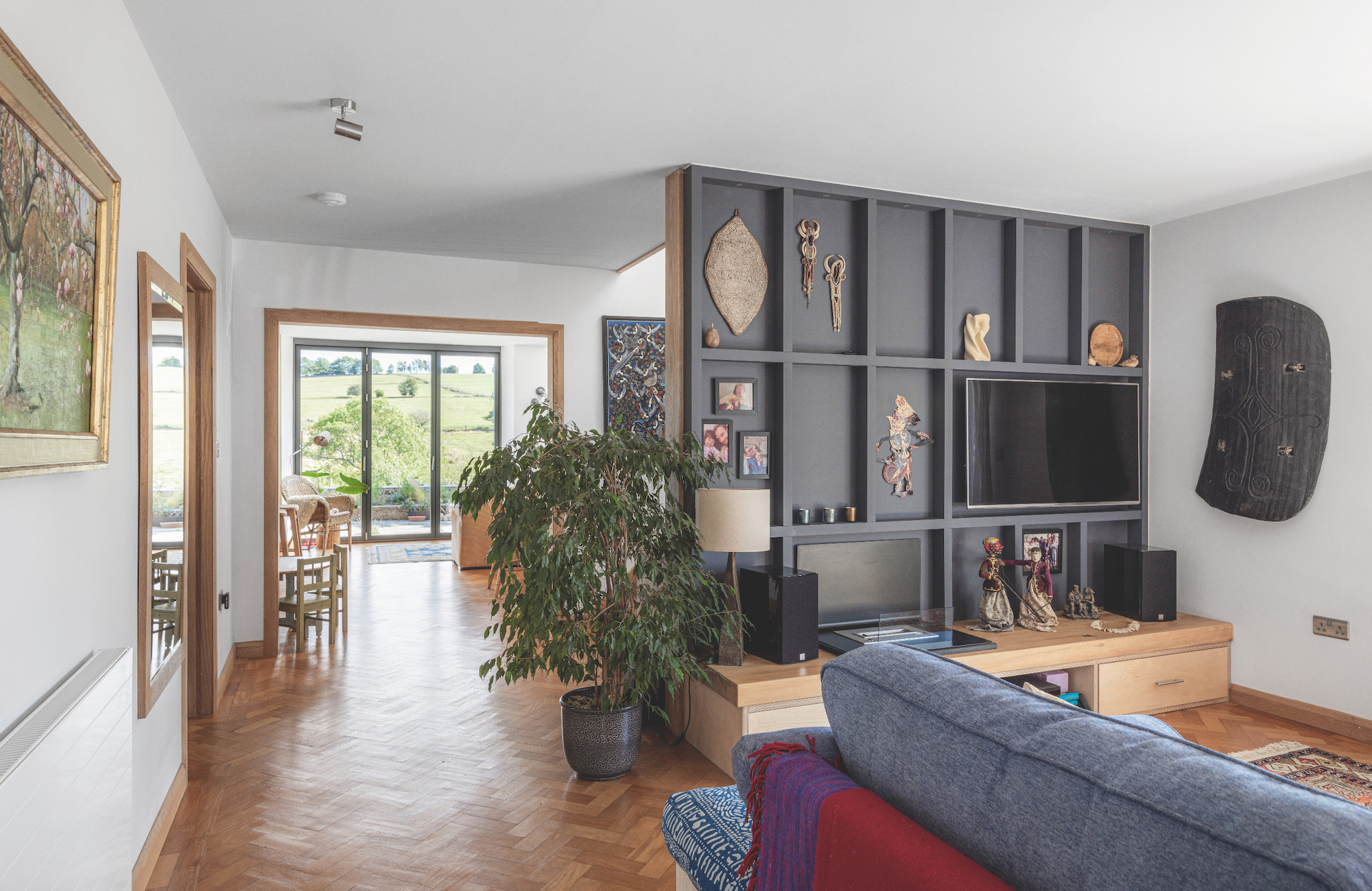
The practical pair also considered their current and future needs in line with their green values. “We wanted our new home to be light, airy and open plan — it’s all on one level downstairs so when we are older we can live on one level,” says Paul.
“We also wanted the interiors to have a modern look, with lots of natural and recycled materials. So we used clay paints while lots of the interior fittings, such as the kitchen island and a desk in the office, are made from an old Monkey Puzzle tree.”
Using renewables to pay nothing on energy bills
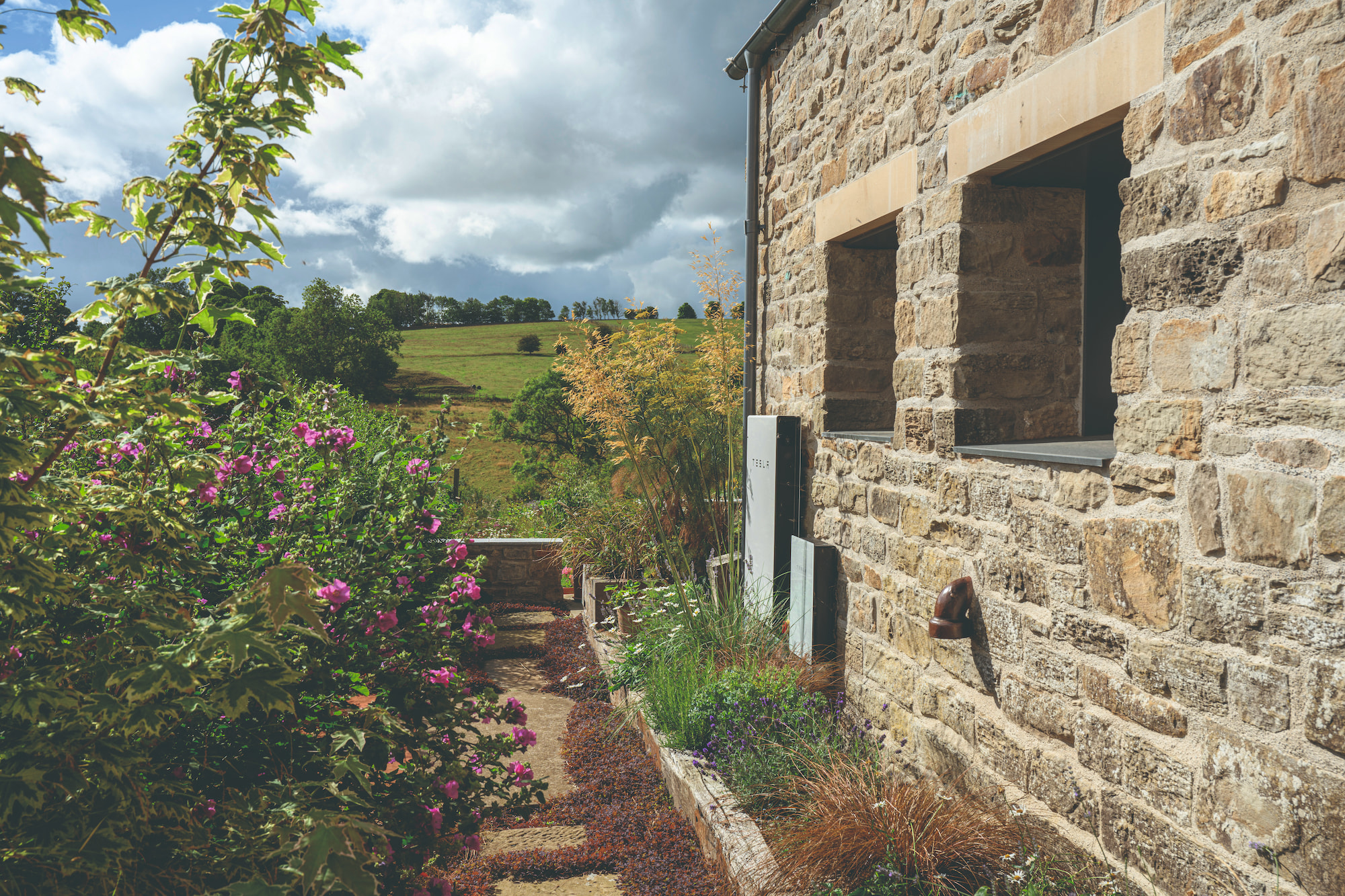
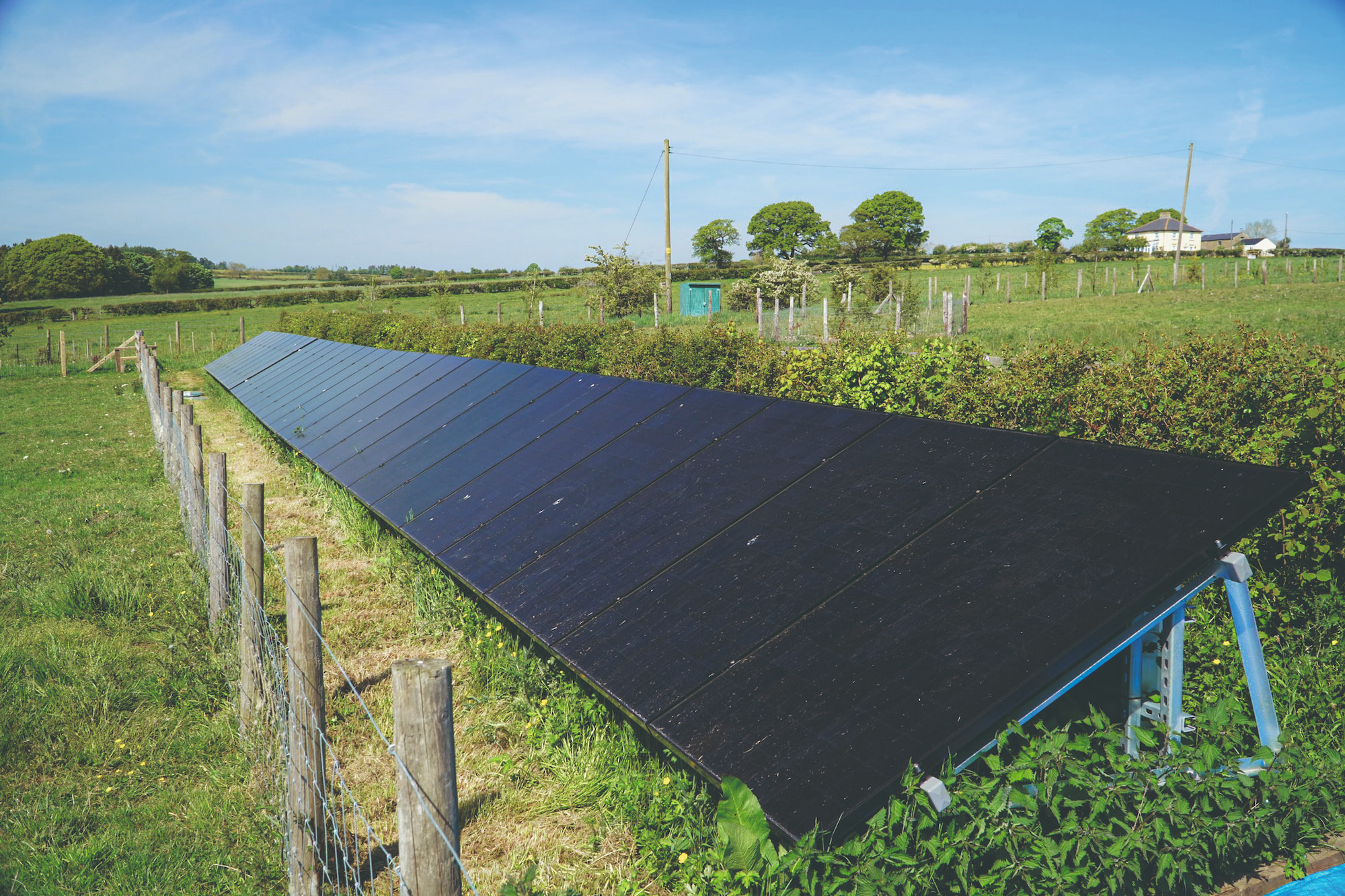
Keeping building and ongoing energy costs down was another key goal. “Our architect designed carefully to ensure that the building cost no more to convert than using conventional building methods,” says Paul. Savings included foregoing underfloor heating – not needed as the structure had an excellent airtightness level as well as being well insulated – and installing only three radiators in the entire building.
That, plus the PV solar panels and battery storage, mean the couple pay nothing for their energy. In fact, the home produces more energy than it uses, earning it the rare EnerPhit Plus standard from the Passivhaus Institute.
“The house has more than lived up to expectations,” says Paul. “A particular surprise was having a constant comfortable temperature with high-quality air [via the MVHR system], and no need or desire for any extra heating.”
Get the Homebuilding & Renovating Newsletter
Bring your dream home to life with expert advice, how to guides and design inspiration. Sign up for our newsletter and get two free tickets to a Homebuilding & Renovating Show near you.
Alison Wall is an experienced homes journalist, and former chief sub editor of Homebuilding & Renovating. She has interviewed countless self-builders and renovators regarding their projects, and has a special interest in eco builds. She is also renovating her 1970s home and garden, and has a particular interest in making her own home greener, having recently added solar panels, an EV chargepoint and a solar battery system.
- Gabriella DysonInteriors journalist and contributing editor