Is this the future of housing developments? Discover the custom-build site turning it all on its head
These custom build homes in Oxfordshire are leading the way in sustainability — during construction and for years to come
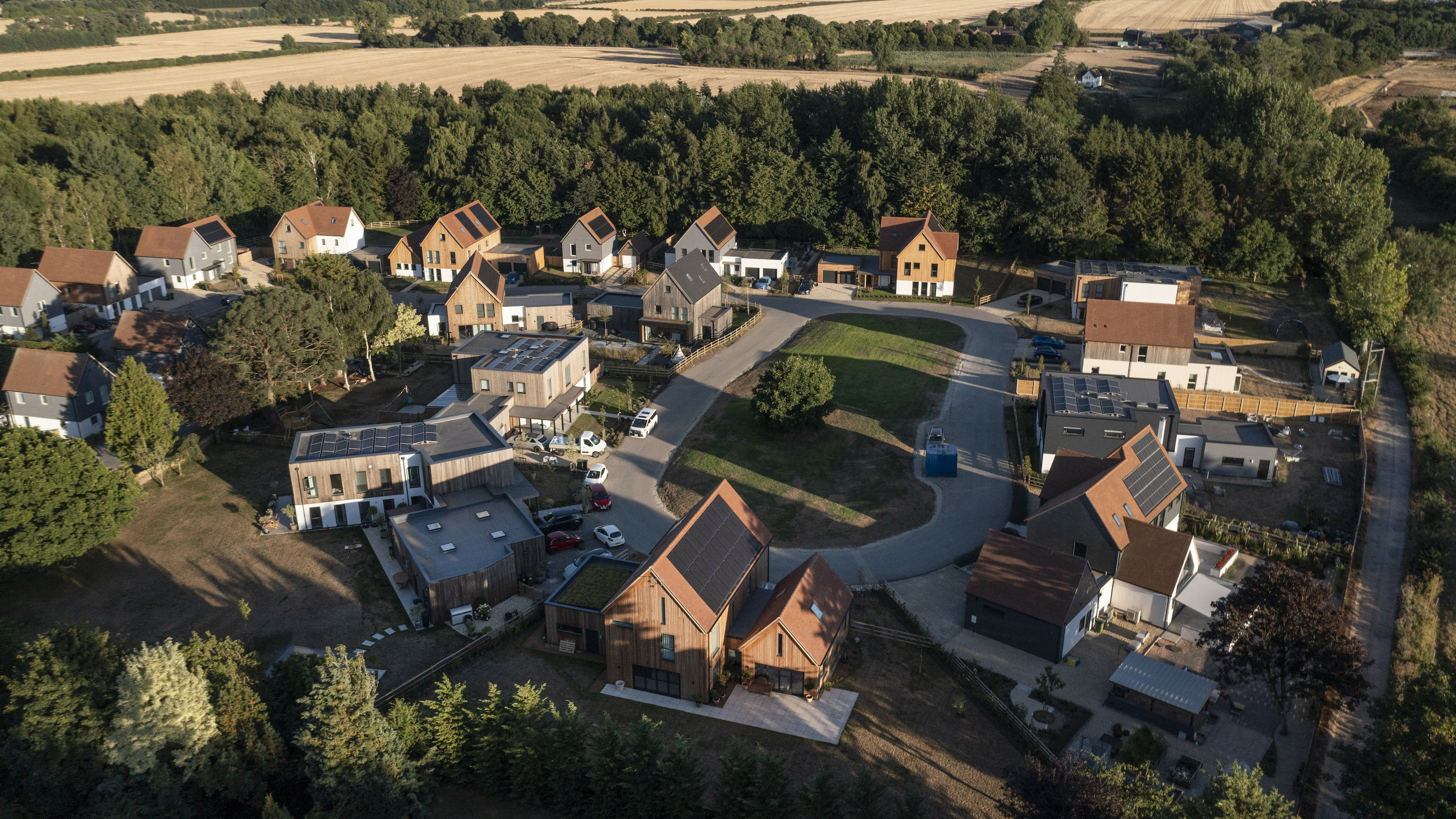
Deep in the heart of the Oxfordshire countryside lies a small development, Springfield Meadows, that could pave the way for anyone considering creating their own eco home, even if the self build route isn’t for them.
Built by Greencore Construction, the eight-acre site comprises 25 new homes, of which 12 are custom built — meaning that the owners purchased a shovel-ready plot, complete with the all-important planning permission and an in-house design team and architect ready to customise the company’s designs.
And given the freedom to make their mark, the homeowners approached the task with gusto. “I don’t think any house has the original footprint it was supposed to — they’ve all been tweaked and changed,” says Greencore’s James Pritchett. “For the internal layouts, we tried to give homeowners two or three options, and again everyone tended to go off piste! But we gave them the option to do that, and it wasn’t a problem for us.”
But that's what custom build is all about — some freedom of design to create an individual home, but with the support of a custom build enabler such as Greencore.
A greener approach
Custom build is a popular concept, but what makes this site all the more remarkable is its green credentials: the homes themselves perform better than Passivhaus, the rural site includes a pond, orchard and wildflower meadow and there’s even a car club that allows residents the use of one of two EVs (in addition to their own cars).
“A lot of developers – probably all – have a negative impact when they build something. We wanted to have a positive impact on the planet and the environment,” says James of Greencore Construction.
“We set out to create the most sustainable development in the country and to do something innovative. We were determined to show the mainstream housebuilders that we can be building to zero carbon now.”
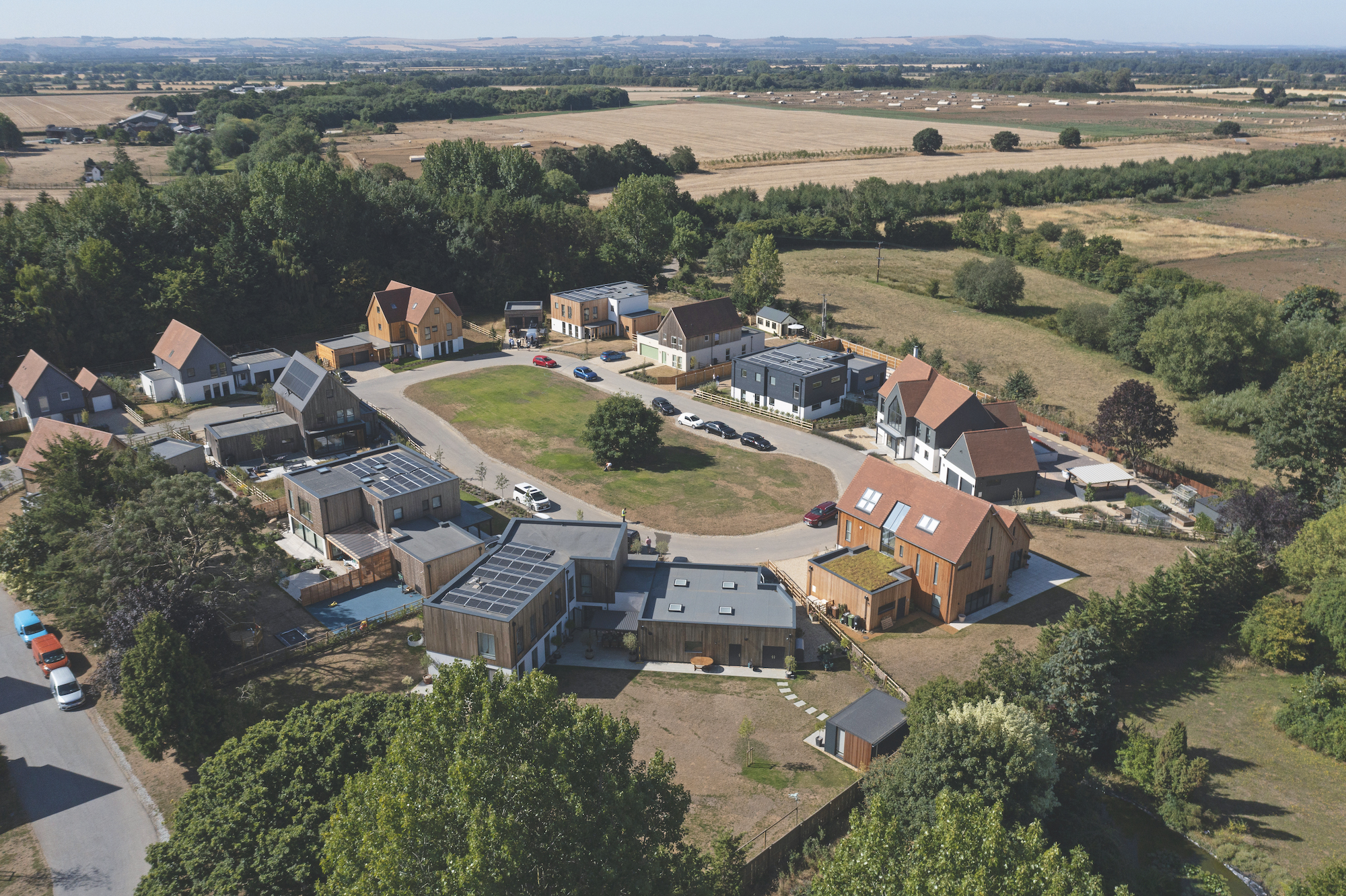
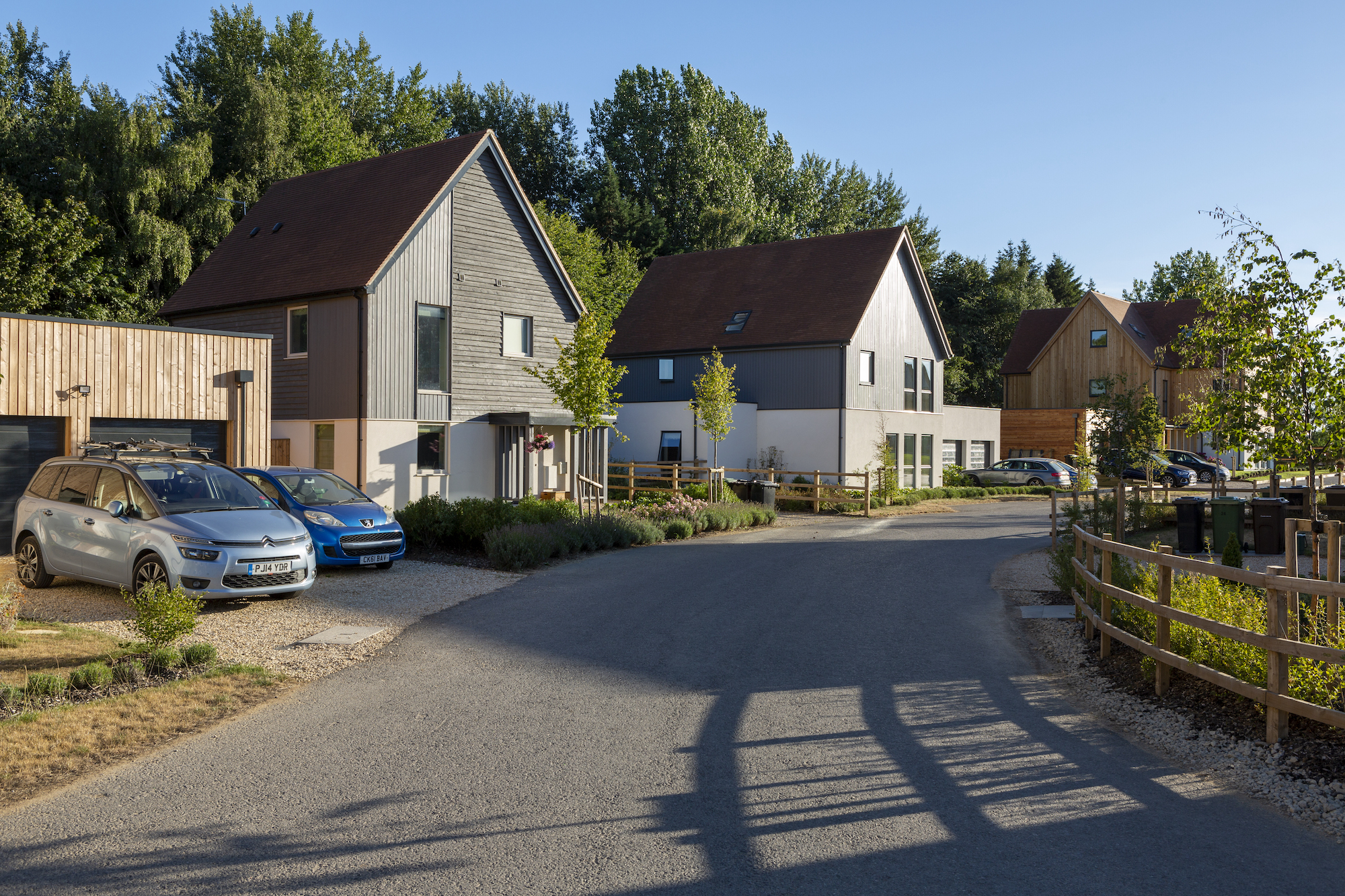
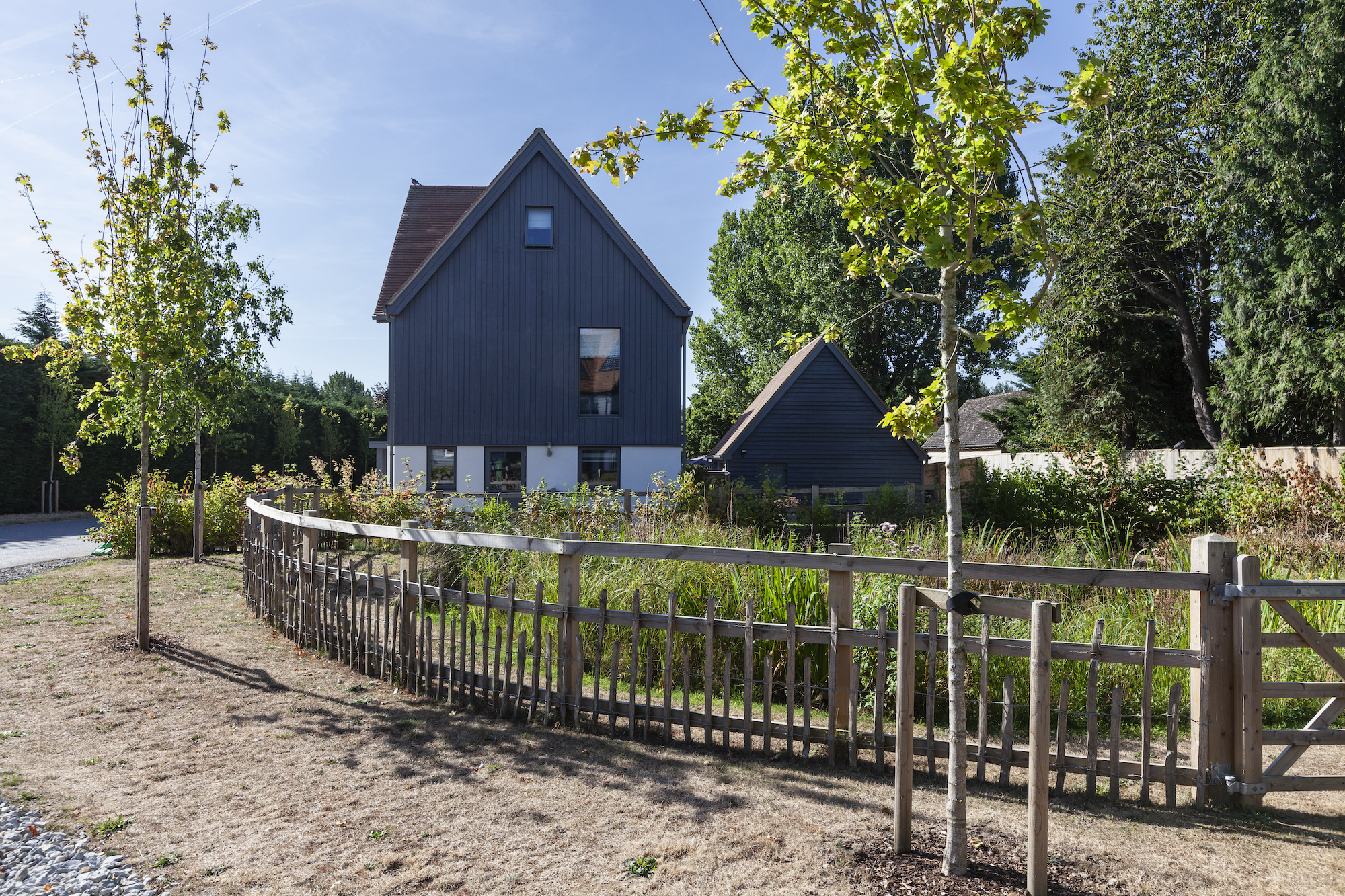
Addressing carbon emissions during construction
Where the houses really score is in their construction, using 90% less carbon emissions than a standard UK home of the same size during the build process, which by most measures is an energy hungry process: just think of all that extraction, processing and transporting of building materials as well as the construction itself. So rather than brick and block or concrete, the houses have been built using a timber frame construction and timber walls pre-fabricated in a nearby factory.
The closed timber frame panels were then insulated with lime-hemp and wood fibre insulation. As well as producing super-insulated walls, the off-site production process helped speed up the build process. “The walls are precision built, with tolerances of less than one millimetre, which meant that construction could be quick and accurate — the superstructure of the houses was up in two weeks,” says James.

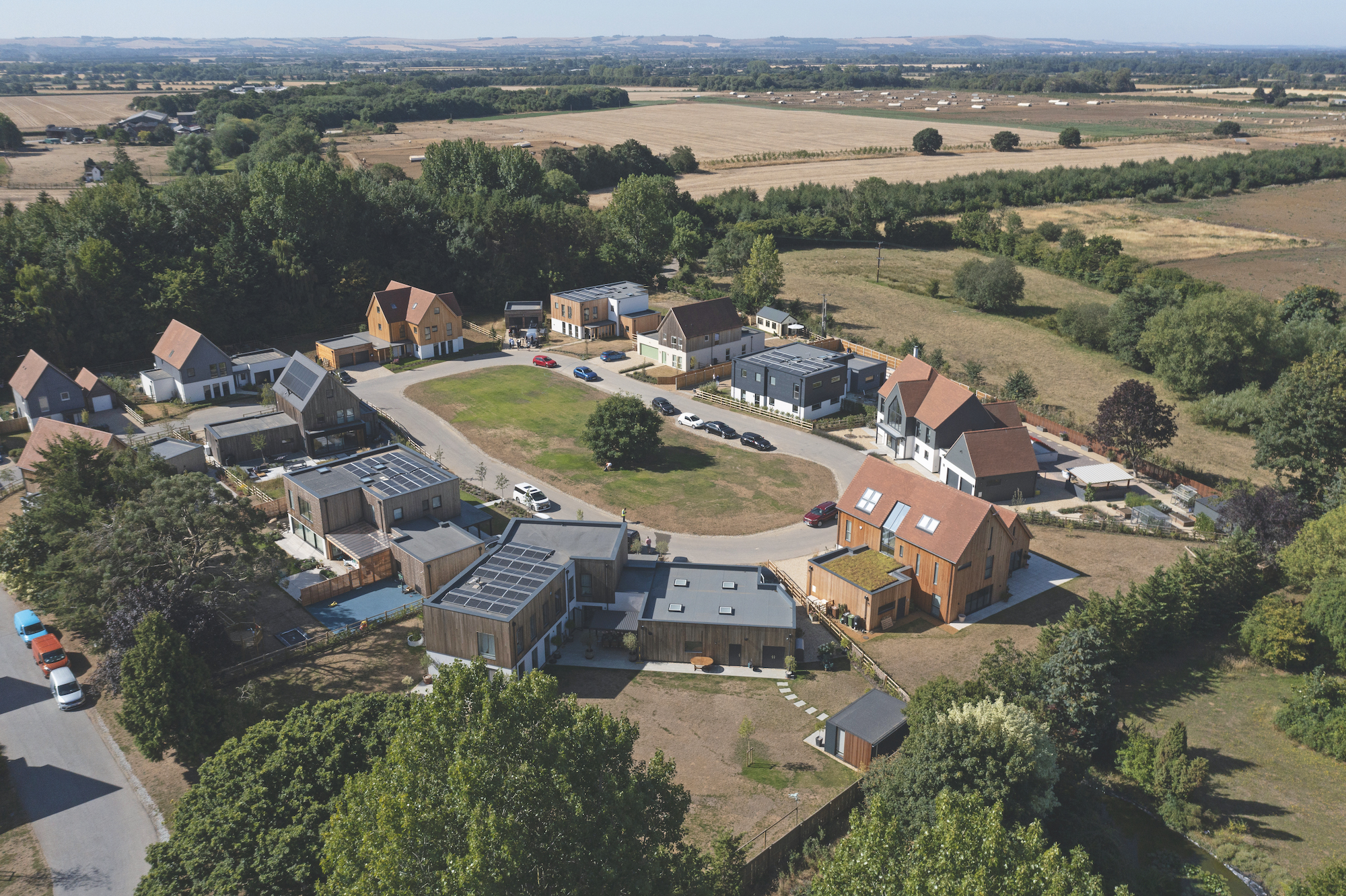
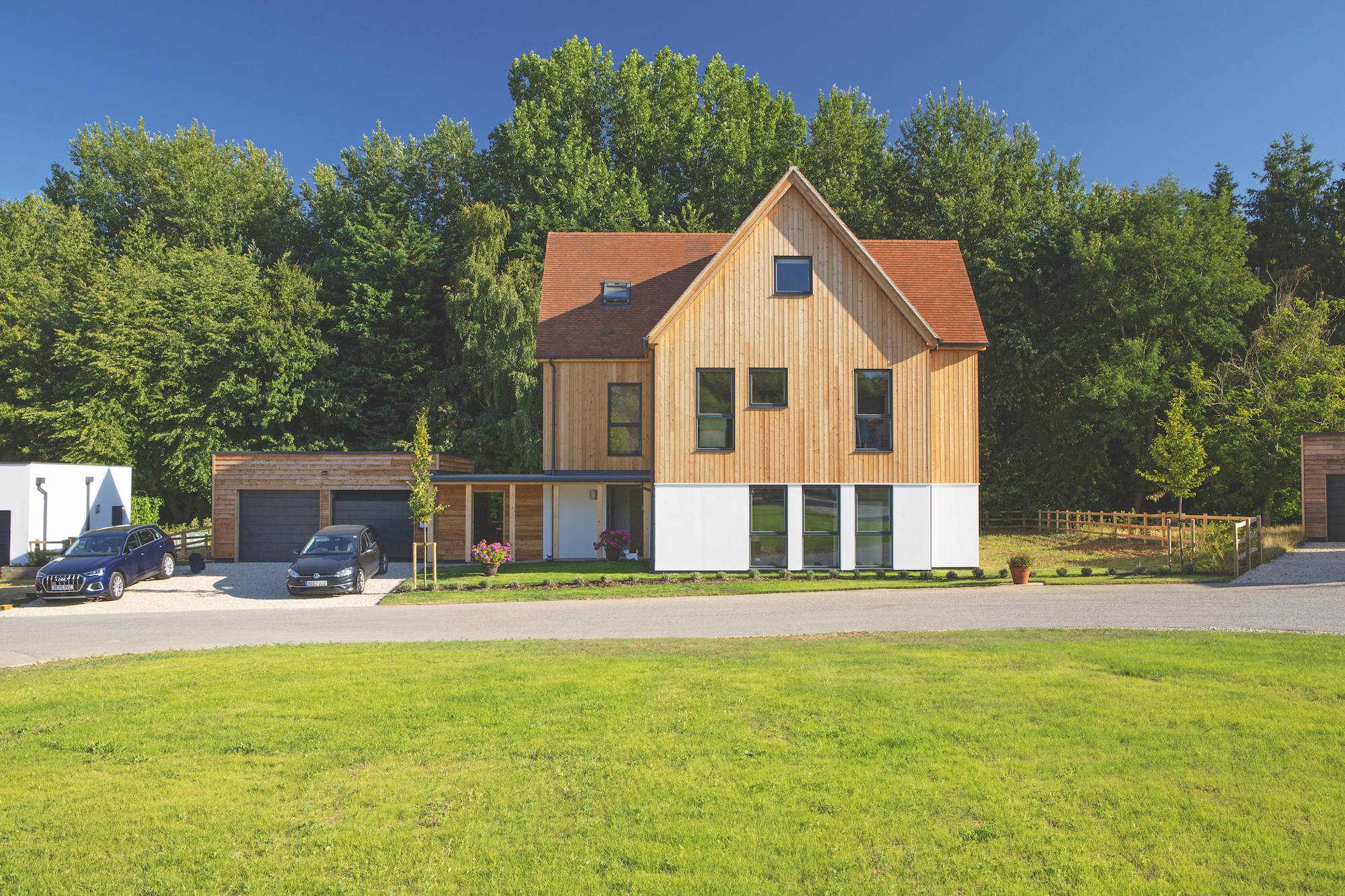
Back on site, the result is a cluster of carbon neutral (otherwise known as zero carbon) houses — this means that during their lifetime, energy consumption will be net zero, thanks to the photovoltaic solar panels on the roofs and connection to green electricity suppliers.
Some of the houses are actually carbon negative, which means they will generate more energy than will be used in their construction and use.
“These houses sequester more carbon than they ever emit during the construction phase. To do this we use a lot of biobased materials, natural wood fibre and hemp that all lock up carbon during photosynthesis,” explains James.
Going for a greener way of building
Wherever you look on site, there’s evidence of this careful carbon balancing act: the clay tiles on some roofs, for example, are among the most carbon intensive materials on Springfield Meadow but their carbon footprint is offset by the bio materials used in the build that lock up carbon. Plus, the solar panels are embedded into the roof, so fewer clay tiles are needed: a saving in both energy and costs.
Some aspects of this carbon neutral approach are surprising. Take heat retention: the homeowners don’t need air source heat pumps (ASHPs), as the heating requirement is so low that it does not justify the cost of installation — a simple underfloor direct heating system suffices.
A few cautious owners have opted for ASHPs, and around one-third have installed solar batteries, too. Cooking is via induction or halogen hobs (as you’d expect there’s no gas on site) and rainwater harvesting allows for plenty of water for keen gardeners.
MVHR systems in all the houses pump in clean fresh air and expel stale air, with some homeowners reporting a blunting of their hay fever symptoms.
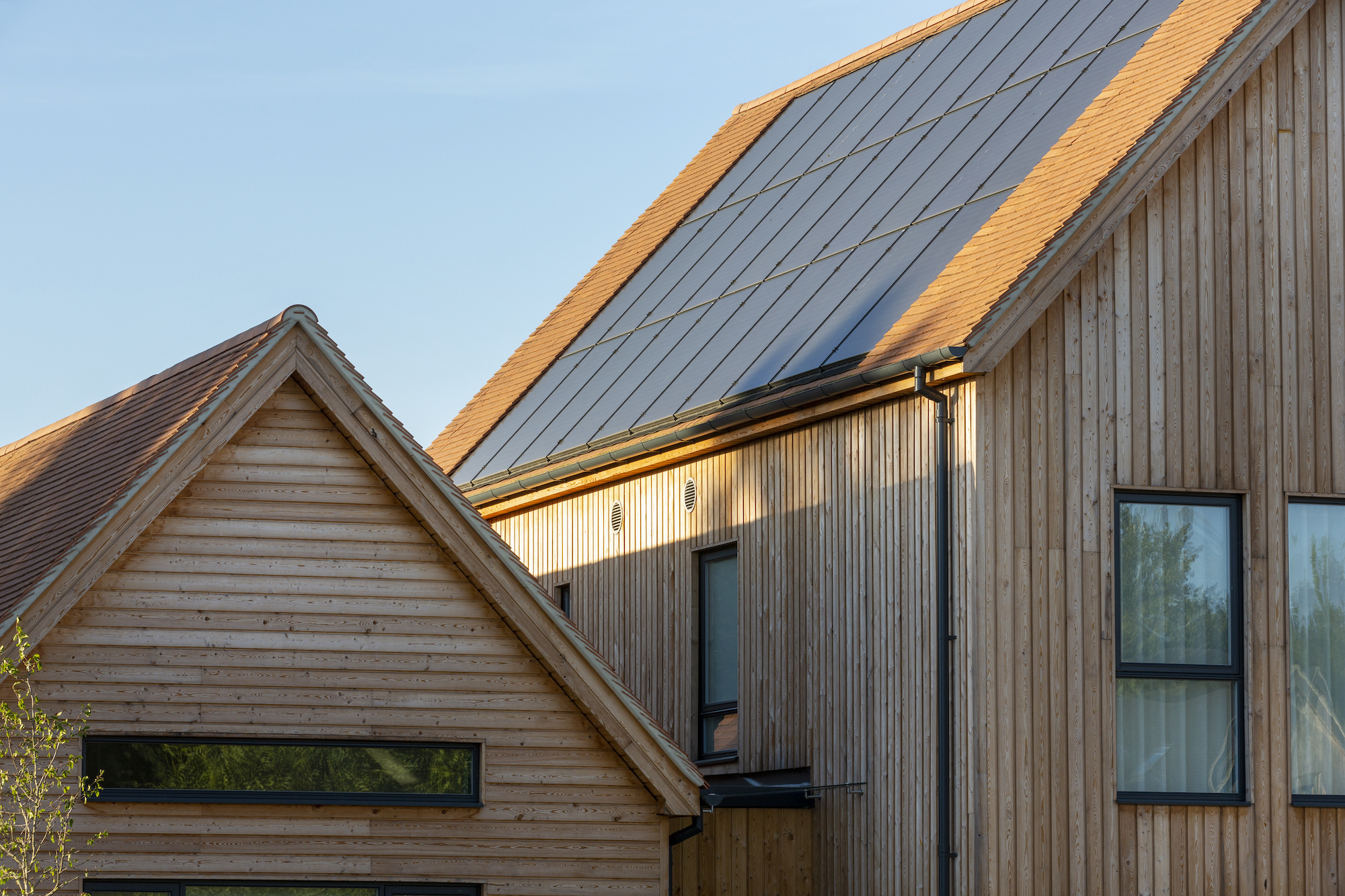
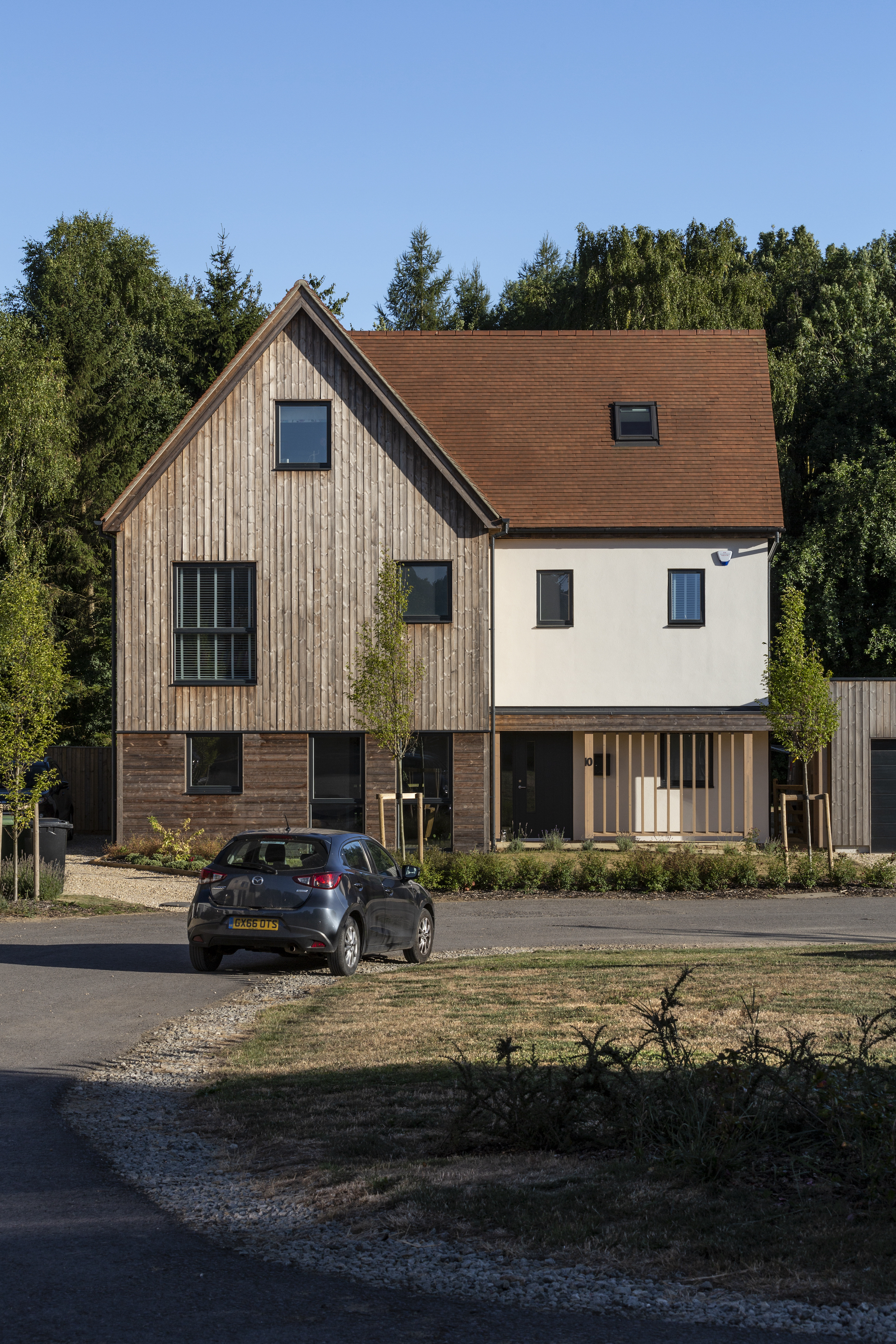
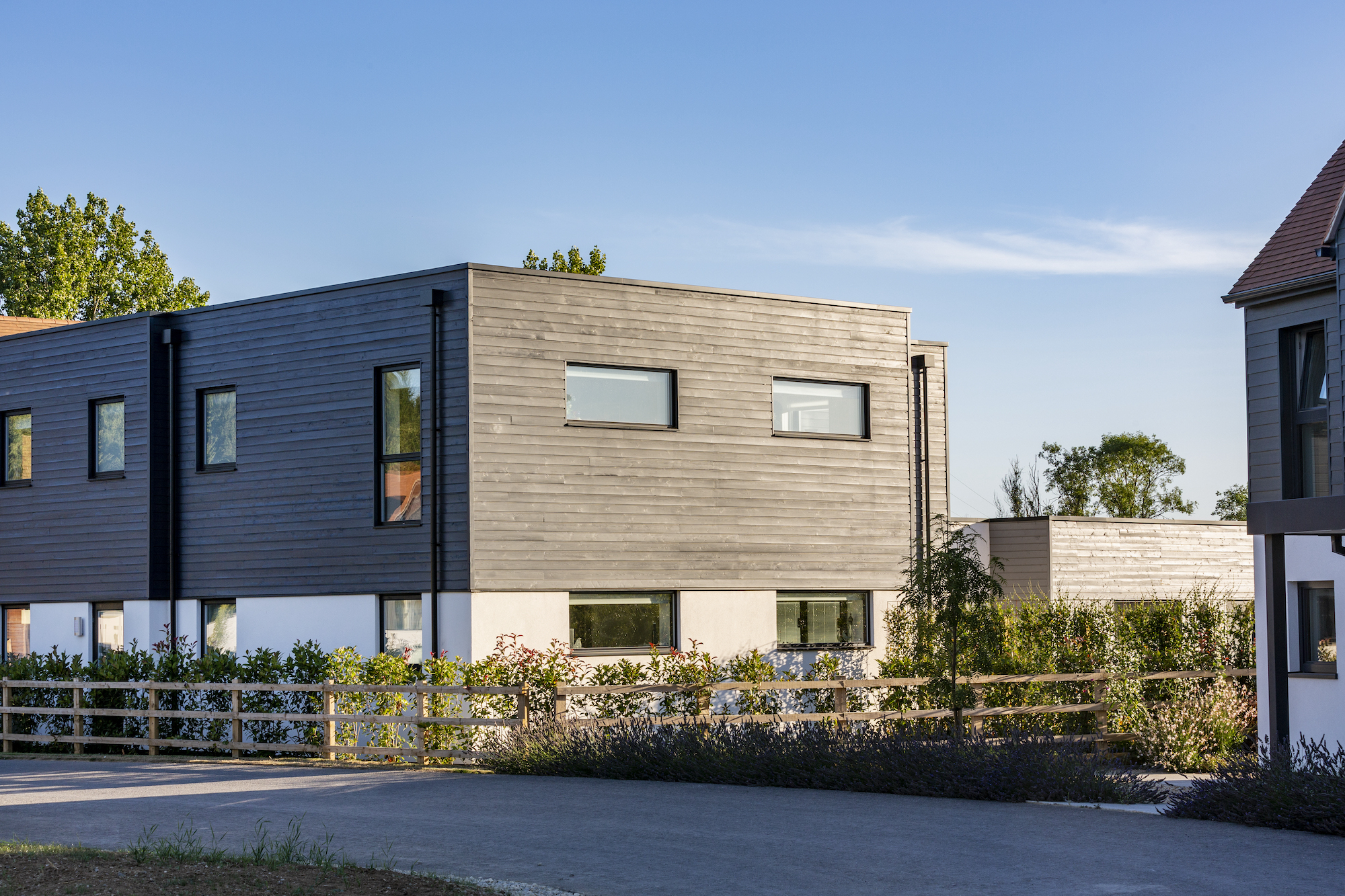
Many, if not all, of these measures will be familiar to self builders keen to reduce their carbon footprint. But is there a take-home message from this project that other people can learn from?
There is: and the answer comes down to using timber and natural materials according to James. “If you are using a timber frame structure and use as many bio-based materials as possible you can do a really good job of offsetting your carbon,” concludes James.
Get the Homebuilding & Renovating Newsletter
Bring your dream home to life with expert advice, how to guides and design inspiration. Sign up for our newsletter and get two free tickets to a Homebuilding & Renovating Show near you.
Alison Wall is an experienced homes journalist, and former chief sub editor of Homebuilding & Renovating. She has interviewed countless self-builders and renovators regarding their projects, and has a special interest in eco builds. She is also renovating her 1970s home and garden, and has a particular interest in making her own home greener, having recently added solar panels, an EV chargepoint and a solar battery system.