Types of foundation systems and which might be suitable for your soil
Foundations are an essential part of your self-build or extension. But what types of foundation are there and which ones are right for your soil type?
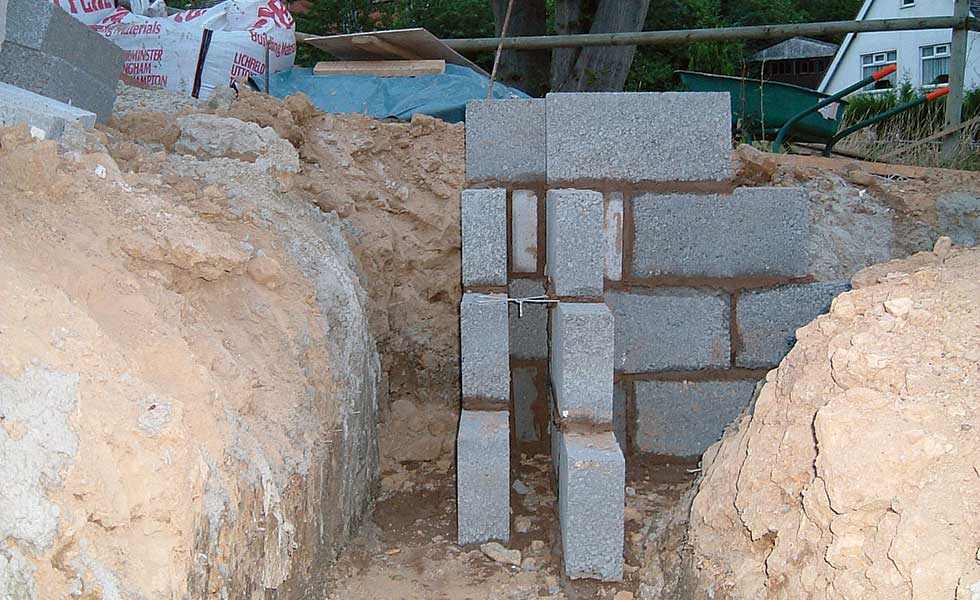
Essential to your build project, foundations are the basis on which your property is secured. Located underground, they help spread the weight, or structural load of the building placed on top of them.
However, not all sites are formed of the same sub-structure and neither are all buildings the same, which is why different types of foundations are needed.
The good news is, the decision on the types of foundation required falls to the experts - namely structural engineers and architects. But, knowing the options available before you start speaking to them can leave you feeling more prepared and potentially save you money on your budget.
Types of foundations - engineered vs foundation systems
The main types of foundation fall into one of two categories - foundation systems and engineered foundation systems. Strip and trench fill foundations are considered standard foundation systems, while engineered systems comprise of raft, pad, piled and screw pile foundations.
For even more advice, information and inspiration delivered straight to your door, subscribe to Homebuilding & Renovating magazine.
While we'll cover each one of these below and provide a signpost to the article with the more detailed expert advice for each type, it's good to know from the outset that standard foundation systems tend to be cheaper than engineered ones.
But there's a caveat. You may not always be able to use the cheaper option. One example of this is when the make-up of the ground or the structural load of your build is such that you need to dig deeper foundations, thus requiring more concrete and labour. In this instance, you may be advised to consider an engineered system.
For a more in-depth look at costs, our foundation cost guide gives examples of what you can expect to pay. Either way, it's always wise to ensure there's at least a 10% contingency in your budget to allow for unexpected issues - and I speak from experience when I say that it's impossible to know the exact make-up of your site until you start digging.
Conventional foundation systems
Strip foundations
The standard foundation solution in most parts of the UK is the strip foundation, also known as strip footings. According to architect, Ninian MacQueen, strip foundations are one of the most common types of foundation used in domestic builds.
Formed, as the name suggests, from strips of concrete laid in the ground, they are placed in the ground beneath load-bearing walls and any supporting columns specified for the main structure.
As strip foundations are one of the most common types of foundations you should find most contractors or groundworkers comfortable with using them. To build them, the topsoil is scraped back (and usually stored for reuse) and trenches dug down to a depth at least 450mm (this is often deeper depending on soil type), which is enough to put the foundations below frost action. The trenches are then filled with concrete to a minimum 150mm below the surface ground level.
The walls are then built up to just below finished ground level in masonry (concrete blockwork or engineering bricks) with the outer leaf switching to the selected external facing material for the walls or plinth, typically brick or stone, just below ground level.
Approved Document A of the Building Regulations (England and Wales) defines the minimum widths for strip footings based on the type of ground and loadbearing wall.
Trench fill foundations
Similar in design to strip foundations, trench fill foundations are also a type of foundation formed from strips of concrete dug into trenches in the ground.
However, they differ from strip foundations in the fact that they are only usually placed around the perimeter of the proposed building. They are not placed underneath load-bearing walls or supporting columns. This makes them easier to set out and a popular choice for extensions.
It's also important to realise that as they only run around the edges of a property, the structural load they are able to bear is far less, meaning while they may be suitable for some houses and smaller projects such as outbuildings, they might not be strong enough for larger properties.
But, as the depth required for them is usually quite shallow it does mean you should be able to avoid digging too deep - both physically in the ground and your pockets when it comes to ordering concrete.
Nonetheless, it's important to make sure that for both strip and trench fill foundations, they are placed deep enough below the ground frost level to avoid the ground swelling and contracting, leading to the integrity of the foundations being damaged and creating problems such as subsidence.
Engineered foundation systems
Where the required depth of foundations is more than 2.5m it becomes impractical to use conventional strip or trench fill foundations unless a basement storey is planned. In these cases it is more cost-effective to look at alternatives such as a concrete raft or piled foundations.
Raft foundations
If the word raft brings a picture of a watertight base, rectangular in shape to mind, you're not too far away from the premise of how a raft foundation looks from above.
A raft foundation is a reinforced concrete slab cast over a compacted hardcore sub-base that spreads the load of the building over a larger area of ground to overcome ground conditions with a lower load-bearing capacity.
Raft foundations are usually designed by a structural engineer, taking into account the ground conditions assessed in a geotechnical survey or at least inspection of trial holes by the engineer.
The raft design usually has an ‘edge beam’ around its perimeter and under any areas carrying large point loads. This consists of a cage of steel reinforcement that will need to be carefully assembled on site. Internal stiffening beams are sometimes needed too. These beams transfer the building loads through the rest of the slab and then evenly over the ground.
However, there are also four different types of raft foundations, meaning each type actually looks different below the surface. While architect Ninian MacQueen provides more detail in his piece on what are raft foundations, the main four types are:
- Solid slab - includes flat raft mat, wide toe rafts, slip plane rafts and blanket rafts - defined by their varying depths or the use of extra materials below them such as sand
- Slab beam - includes extra ground beams and used when there are uneven structural loads in the building
- Cellular raft - made from two layers of concrete with beams in between for when the ground is low load bearing
- Piled raft - include piles set below the raft for extra stability making this type of foundation suitable for taller buildings
Pad foundations
Pads of concrete, usually cast in situ, are placed beneath the position of each post of the frame and the posts are linked together at ground floor level to spread the load evenly. Pad spacings, size and depth are designed according to the design load of the building and the ground conditions.
Unlike the previous types of foundation discussed, pad foundations are square or circular shaped blocks of concrete that sit across the site at load-bearing points. But, as with raft foundations, there are also different types of pad foundations depending on the structure they are being used to support.
- Plain pad - suitable for lighter loads and also referred to as footings
- Reinforced pad - containing reinforcement in the form of steel bars
- Combined double pad - when two columns require pads next to each other
- Continuous pad - placed in a line and joined by steel rods
Although pad foundations are generally seen as a relatively low-depth type of foundation, they can be made deeper if the soil type is low load-bearing. Nonetheless, on the whole, they are more suited to structures such as sheds or warehouses, or buildings of either a steel frame or timber post and beam, rather than a new-build home.
Pad foundations can be well suited to sites where excavation needs to be kept to a minimum and can also be a cost-effective solution when overcoming a sloping site by suspending the ground floor on a post and beam frame.
Piled foundations
Where ground conditions are poor, variable or unpredictable, piled foundations are usually the solution. Although from the name you'd be forgiven for thinking these may involve a stacked system, as Ninian MacQueen explains in his article about piled foundations, they are actually long cylindrical like structures that are bedded deep into the ground.
To use the correct terminology, they are driven or bored down and can also be made of steel as well as reinforced concrete.
As with some of the other types of foundation, the term piled foundations includes a number of different sub-categories: end-bearing, driven, friction and bored piles are just some of the terms you may hear and are covered in more detail by Ninian. Other smaller versions include micro piles and helical and ground screw piles.
Once in place, the larger versions are capped off and usually connected via a series of ground beams. The main reason for using them? Primarily to deal with taller structures being built on weaker ground. Although in some instances, cases of them being required in extensions are known of to avoid disrupting the drains.
Smaller versions such as ground screws are also being used more widely in extensions and structures such as modular garden rooms.
Screw pile foundations
Local planning authorities will often allow structures to be built around trees within a root protection area on the proviso that the structures are supported by screw piles. These are a relatively new foundation solution consisting of slender, hollow steel shafts with a small number of steel helices (or screw threads) welded to them. The piles are screwed into the ground until they achieve sufficient friction to support the required load. This can be a cost-effective way of building foundations on sloping ground too, as the steel piles can be left above ground and linked together with tension wires or rods, and topped with a steel ringbeam or grillage to build from.
Chris Willis, co-director of OffPOD, a modular build company, explained how they use ground screws where possible in their builds.
"As a company, we've always tried to use them since we started," says Chris. "Not only because they're innovative and offer a more eco-conscious build option, but because they also be a much quicker way of building and can help when you're dealing with tree root systems that would be otherwise problematic with a more traditional type of foundation."
FAQs
How much will my foundations cost?
The cost of building foundations is one of the biggest variables, so anyone who wants to keep control of their budget and schedule needs to work out the most appropriate foundation system to use as early as possible.
Identifying the most cost-effective solution will depend largely on the ground conditions on site, including the type of soil, aggregate or rock and its key constituents.
The best way to achieve this prior to starting work on site is to instruct a geotechnical study which involves digging or boring trial holes around the site of a proposed new building, principally to establish the load bearing capacity of the soil at differing depths.
Samples are collected and tested for plasticity (shrinkability), pH levels, sulphates, moisture contact (seasonal water table) and other factors that will allow the foundation solution best suited to the site to be determined.
Neglecting to investigate the ground conditions on your site is one of the earliest and costly mistakes a self builder can make.
Which foundations are suitable for extensions?
If you're considering an extension, you'll also need to be up to speed on suitable foundations.
Our expert chartered surveyor, Ian Rock, covers the topic in great detail in his article foundations for extensions, but in summary, unless you are replacing a conservatory with a modular system such as a hup! build whereby the system is light enough to give you a more solid style extension on an existing conservatory base, you will need foundations for your extension.
A soil survey and initial ground investigations or test holes are always recommended, and while trench fill foundations are the most common type used for extensions the same variables of soil and structural load will apply to your extension.
Always consult the experts to ensure your extension will meet with the necessary Building Regulations.
What might affect my choice of foundation system?
Where the foundations are affected by tree roots (or their previous removal), you may be required to employ a fairly deep trench filled with concrete but with a compressible material to one or both sides of the external trenches to counteract any heave or expansion in the ground.
Water pipes must enter the building at a depth of at least 750mm but no more than 1.35m below ground. If that means that they pass through a concrete foundation then they must either be laid prior to pouring or, better still, a duct installed for them to be pushed through later.
If sewage pipes leaving the building have to be deeper than the top of the foundation concrete then they should also be ducted; they cannot be trapped within the concrete and must be able to move freely.
Bringing electricity to site or bringing gas to site doesn't usually need to be ducted or installed at this point as they are normally surface mounted. Finally, the building and warranty inspectors will have to approve the excavated foundations prior to any concrete being poured.
Keen to learn more? Read our step by step guide to building foundations to increase your knowledge base and start to venture above ground with our guide to building with masonry.
Bring your dream home to life with expert advice, how to guides and design inspiration. Sign up for our newsletter and get two free tickets to a Homebuilding & Renovating Show near you.
Michael is Homebuilding & Renovating's Director of Content, Vice Chair of the self build industry body, the National Custom and Self Build Association (NaCSBA), presenter of multiple property TV shows and author of Renovating for Profit (Ebury). He also runs an architectural and interior design practice, offering design and project management services. He is one of the country's leading property experts and has undertaken over 30 building projects including two self-builds and the renovation of a Grade-II listed farmhouse.
Michael has presented over 150 property shows for BBC, ITV1, Channel 5, UK TV Style, and Discovery RealTime, including I Own Britain's Best Home; Don't Move Improve; Trading Up; Good Bid, Good Buy; Build, Buy or Restore?; How to Build A House; and Hard Sell.
Michael is also a regular expert at the Homebuilding & Renovating Shows. He has written for leading British newspapers, including The Daily Telegraph, Sunday Times, Daily Express and The Independent and has appeared on news programmes such as BBC Breakfast.
- Sarah HarleyAssistant Editor