How much does it cost to build a house in 2025? Our self-build expert explains how to allocate your build budget
If you want to build your own home, knowing how much it's likely to cost is key when planning your design. To help you plan your budget, our expert guide reveals the average self-build costs for 2025
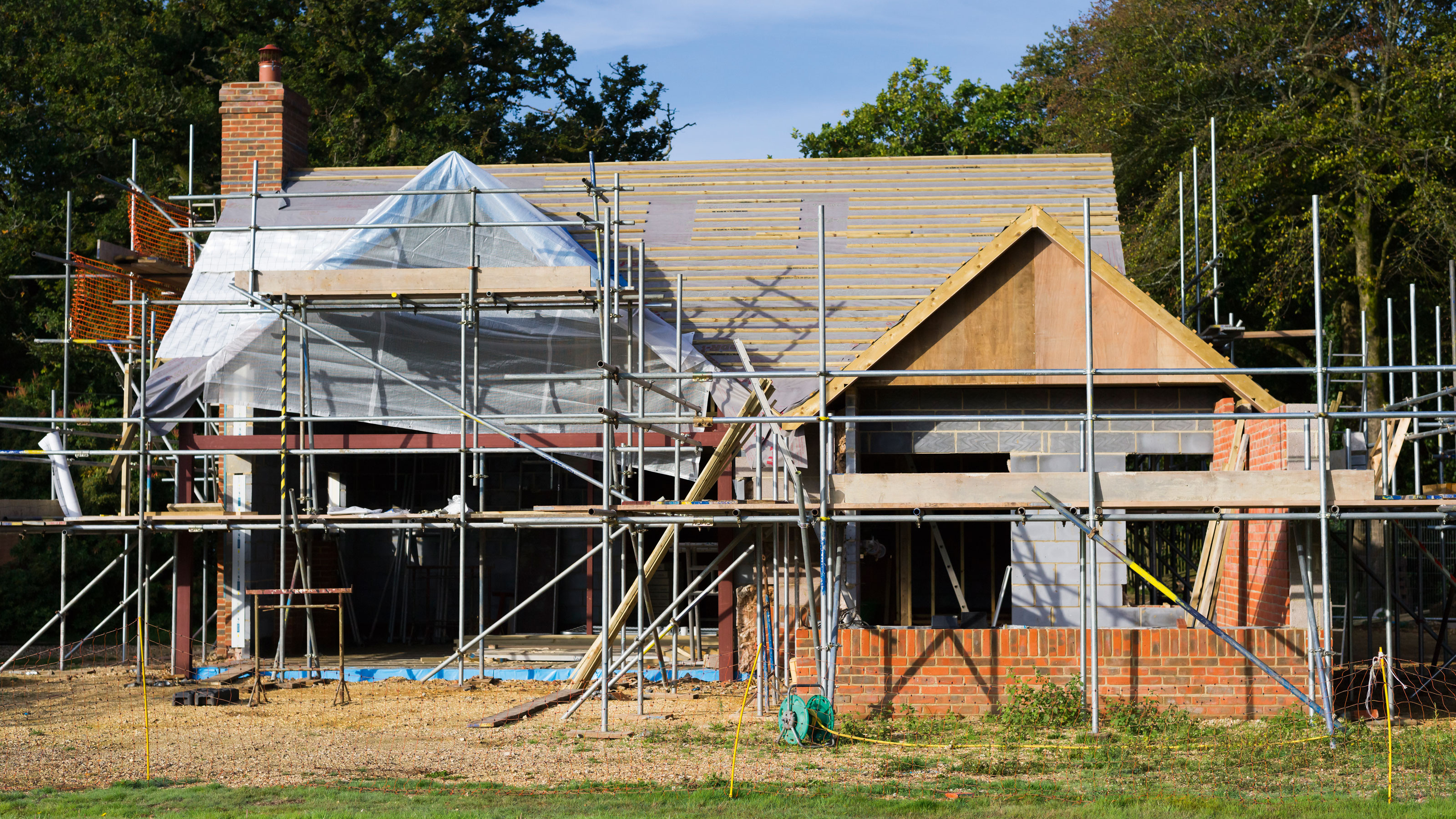
- Plot costs
- Allocating your budget
- Construction system costs
- Utilities connections costs
- Foundations costs
- Construction materials costs
- Roofing systems costs
- Walls, floors and ceilings costs
- Staircase costs
- Chimney costs
- Windows and doors costs
- Kitchen and bathroom costs
- Flooring costs
- Heating and hot water system costs
- Electrics costs
- Project management costs
- Additional costs
- FAQs
Keen to know how much it costs to build a house? As you might imagine, it's a big question that's not easy to give a direct answer to. However, it's the first hurdle you'll need to make it over to decide if building a house is right for you.
The truth is, a self build can cost almost anything, with houses built for just a couple of hundred thousand to houses in the millions. The variables that will have an impact on the overall cost of building your own home is long, however, with the right guiding hand, you can break down this overall cost into smaller sections and start to decide where to spend your money.
It's worth remembering that building your own home has the potential to pay dividends. A well-considered homebuilding project could potentially net you a profit of 25-30% when (or if) you come to sell.
Use this guide to the costs involved in building a house to a get an idea of how much you dream build will cost, so that you can start to plan your budget.
How much should I spend on building a house in 2025?
The answer to how much it costs to build a house really depends on how much you have got to spend. Self-build can be such a personalised experience that there is likely an option available for you no matter the budget (within reason).
Determining how much you have to spend is a case of looking at the following:
- your savings
- equity from the sale of your current home
- funds available via a self build mortgage if required
The first expense, before you even start to build your home, is the plot (unless you already own one), the cost of which will depend on where you want to live and how big a garden you want. You'll need to factor in the costs related to purchasing the land, alongside legal fees and land taxes (SDLT in England, LBTT in Scotland and LTT in Wales). You can visit hmrc.gov.uk for the latest tax rates on land transactions. Site surveys are also invaluable, including a topographic survey, geo-technical survey and where relevant, a tree survey.
Once you've worked out this cost, subtract it from your savings, equity and mortgage and you'll be left with your budget for the design and construction work. However, we suggest setting 10% aside as your contingency fund straight away plus 5% to deal with inflation, which whilst subsiding compared to 2021 is still prevalent. This can be used to cover any unforeseen circumstances that might arise, especially in dealing with the groundworks phase, including the building foundations, which is typically the hardest to establish accurately.
How much does a self-build plot cost?
You can get a good idea of plot prices by visiting Homebuilding & Renovating's own plotfinding service Plotfinder.net — which is also the UK’s largest database of small development sites. Costing only £5 a month for a subscription, there's more than 10,000 plots and projects on the site to look at with plenty of development opportunities for a range of budgets. You can also sign up to a weekly newsletter that sends you a roundup of the best projects coming onto the market in the UK.
While this will give you an outline figure for different kinds of plots in different areas, there are plenty of other ideas around for how to find a plot for your build which may be offer a more affordable route.
Bear in mind that the conditions of your plot may add to the overall costs to build a house. Key factors influencing construction costs include: access to the highway, utility connections, site clearance or decontamination, soil type/ground conditions, topography, access and ecology/protected species habitats.
Dealing with legal issues can also add to costs, such as making arrangements for utilities connections or access across adjacent third party land, or removing a restrictive covenant. Using a conveyancing solicitor with specific experience in development land transactions is very important.
Another way to value a building plot is to reverse engineer it from the value of the build potential. According to expert self-builder David Snell, the cost of a self build should adhere to a 'third, third, third' principle, with the plot cost, building cost and profit to be made making up the final home value. This gives you a pretty easy formula to look at the value of other homes on similarly sized plots of land in the area, and work backwards to your plot cost.
How to divide a self-build budget
The two largest slices of the pie, as demonstrated in this pie chart, are the cost of your home’s superstructure and foundations and floor structure. The superstructure includes the walling, external cladding and roofing, and will typically account for 25-30% of the overall budget. The cost of the superstructure will vary depending on the size and construction system used.
Aside from these two expenses, the rest of your build tends to account for between 5-10% of the total cost. The trick with balancing your budget is to understand that some individual elements can potentially be reduced in price later down the line if earlier elements go over the initial budget, but by having a contingency budget you can avoid compromises.
Construction system costs
Need more advice or inspiration for your project? Get two free tickets to the Homebuilding & Renovating Show
The cost of the load-bearing structure of a self-build depends on the system used, and this should be a factor when choosing a construction system. However, it's important to consider that while some systems may cost more than others, you also need to take into account the speed of build, and any savings a particular system might incur further down the build.
For example (based on an average build cost of £575,000-£600,000):
- Traditional blockwork construction This includes external walls and ground floor partitions with timber first floor partitions and now accounts for 14-16% of overall build cost. The current average is £80,500-£96,000 and it remains the baseline for comparison.
- Timber frame construction (140mm studs) The premium over blockwork is 15-20% due to timber prices and the overall impact on total build cost is 2-3%. The additional cost equates to approximately £12,000-£17,500, but it is increasingly popular due to speed of construction and environmental benefits.
- Oak frame construction The premium is 40-50% over blockwork, which adds 7-8% to overall construction costs. The additional cost is approximately £40,250-£48,000. It's a more luxury market option, but prices are stable due to specialist nature.
- Modern Methods of Construction (MMC) Structural Insulated Panels (SIPs) and insulated concrete formwork (ICF) are currently around 10-25% more expensive than blockwork. It adds 2-4% to overall construction costs (£11,500-£24,000). Although the cost premium has increased it is offset by reduced labour costs, faster build times (typically 20-30% quicker), better thermal performance, lower energy costs over building lifetime, reduced waste on site, better compliance with new Building Regulations and enhanced airtightness performance.
How much do utilities connections cost?
Unless you are buying a serviced plot or replacing an existing dwelling, you will need to allow £10,000-£25,000 for connection to utilities such as the local mains water, sewer and power network (such as bringing electricity to site) and broadband.
Connection to the gas network is still worth exploring, but it is getting harder to meet the current Building Regulations for energy efficiency for new dwellings with a gas or oil boiler.
- Water connection £1,500-£5,000
- Sewer connection £2,500-£8,000
- Broadband/telephone £1,200-£3,500
- Gas connection £1,500-£4,000
Factors that will influence the cost include distance (rural locations are likely to be further from the nearest available connection point), ground conditions, access, road crossings, crossings over third party land. If the site is a replacement dwelling, you may save the cost of some or all service connections, but will need to set aside a sum for demolition and site clearance.
Living off grid is an option and off-grid heating options and other solutions, such as the ones detailed below, can prove more cost efficient for more remote sites.
- Power It is possible to live off micro-generation and battery storage but it is still expensive (£25,000-£40,000) and a backup generator is still necessary (£3,000-£5,000). The reality remains that a mains power connection to even out supply is still the only practical option for most sites, even when microgeneration with renewables is in place.
- Water Where the distance to the nearest mains water connection is prohibitive it is worth exploring the cost of drilling a borehole and creating a private potable water supply at cost of £10,000-£25,000.
- Sewer If there is no mains sewer, you will need to budget for an off-mains alternative in place of a mains drainage connection. As a budget figure, allow £3,500–£5,000 for a packaged sewage treatment plant for a small family and £5,000-£7,500 for a larger household for the sewage treatment plant and £12,000-£18,000 for installation.
- Broadband Starlink is the best option for speed but requires a clear view of the northern sky and is weather dependent. Using 4G or 5G wireless networks is worth exploring, but signal may not be available in remote areas. Some rural areas run a rural wireless network using a central mast and localised antennae on each property. This requires a clear line of sight to the mast and is weather dependent.
How much do the house foundations cost?
The cost of getting out of the ground is not one where there is a great deal of choice, as it is the ground conditions, including the soil type, that will determine how deep the foundation needs to be, the design of the foundations and the cost of excavation. Your project structural engineer will be responsible for designing the foundations and these will need to be approved for Building Regulations compliance.
For a typical 200-250m² self-build including foundation system, ground floor construction, drainage, service connections allow the following depending on ground conditions:
- Good ground conditions
- Strip foundations: £35,000-£45,000
- Raft foundations: £40,000-£50,000
- Piled solutions: £55,000-£75,000
- Challenging ground conditions
- Strip foundations: £45,000-£60,000
- Raft foundations: £50,000-£65,000
- Piled solutions: £65,000-£90,000
- Problematic sites
- Strip foundations: Not recommended
- Raft foundations: £65,000-£85,000
- Piled solutions: £80,000-£120,000
Ground conditions are the primary driver of foundation costs, with poor soil conditions potentially increasing expenses by 40-100%. Site characteristics such as sloping ground (+25-40%), high water table (+20-35%) and contaminated land (+40-100%) can significantly impact the final cost. Access constraints and remote locations typically add 15-30% to the base cost.
The choice of foundation type is crucial, with traditional strip foundations being the baseline, raft foundations adding 20-30% and piled solutions potentially doubling the cost. Design complexity matters too, especially when relating to foundations for difficult sites. Split levels can add 20-30%, while complex footprints increase costs by 15-25%.
Early investigation is essential. Investing 2-3% of the budget in ground investigations can prevent costly surprises further down the line. Always maintain a contingency of 10-25% depending on site risk factors. The foundation package typically represents 15-20% of the total build cost for a standard self-build project.
Construction materials costs
All the costs in this section are based on a typical 200-250m² self-build project with a total build cost of £575,000-£600,000. Prices reflect early 2025 rates and include labour, materials, and standard fixings.
The higher baseline costs reflect current Building Regulations requirements, especially around thermal performance, as well as increased material and labour costs in the construction sector.
How much does it cost to build a house with brick?
Building with brick will typically cost around 6-7% of the house build, approximately £45,000-£50,000 (based on a total build cost of £575,000-£600,000). However, this cost depends on the type of brick used. This figure is based on stock bricks costing between £850-£950 per 1,000 and bricklaying costs of £1,500-£1,800 per 1000 bricks (185m² of brickwork at 60 bricks per square metre plus 10% wastage = 12,000 bricks).
Character bricks, including reclaimed bricks, are more likely to start at around £2,200-£2,800 per 1,000, potentially pushing this element towards £65,000-£75,000, plus additional labour time required to lay irregular-shaped bricks. This is especially true if they are laid in a traditional brick pattern such as Flemish bond, which can add 30-40% to labour costs.
Additional costs can be incurred with detailing, such as brick arches over door and window surrounds, typically adding £200-£300 per feature.
How much does it cost to build a house with natural stone?
Natural stone is a more expensive choice than stock bricks. Using cropped coursed stone blocks to form an independent outer leaf of a cavity wall (with a blockwork or timber frame inner leaf) works out at around £550-£650/m², similar to handmade brick, potentially totalling £70,000-£85,000 for a typical project.
Using reconstituted stone costs much the same for labour but reduces materials costs by 15-20%, bringing the total closer to £60,000-£75,000.
Building using traditional random stonework is slower and although the materials cost is similar, the labour cost is typically 40-50% higher, potentially pushing costs to £90,000-£110,000. The most cost-effective option is using them at a depth of 250mm against full-fill cavity insulation and waterproofed blockwork (if acceptable to Building Control in your area).
Building against a backing block to form a cavity, with an inner leaf of blockwork or timber frame, will add around £35/m².
How much does it cost to build a house with a rendered finish?
Sand and cement house rendering on blockwork is one of the cheapest options, especially if it is self-coloured using white cement and local sand, costing £55-£65/m² (approximately £30,000-£35,000 total). If painting is required, this typically adds around £65/m² to the cost (additional £12,000-£15,000).
Adding lime will make the render more forgiving but will increase the cost to £80-£90/m² (£40,000-£45,000 total). Modern polymer renders are more flexible and crack resistant, and also self-coloured so do not require painting, but are more expensive at £95-£120/m² (£45,000-£55,000 total).
How much does it cost to build a house with cladding?
Painted softwood shiplap can prove a cost-effective choice for cladding a house at £85-£100/m² (£40,000-£45,000 total), especially on a timber frame structure, where no backing block is required.
Dense timbers such as oak (£160-£190/m²), western red cedar (£150-£180/m²), and sweet chestnut (£140-£170/m²), and also heat-treated softwood such as larch (£120-£140/m²), are premium choices with cladding costs ranging from £55,000-£85,000 depending on species chosen. These prices include installation and all necessary fixings, though regional variations may apply, particularly in remote locations where costs can increase by 15-20%.
Roofing systems costs
Roof costs are typically made up of the following elements:
- The structure
- Insulation
- Felt and battens
- Roof covering
- Flashings/detailing
The cheapest option is to build a simple rectangular-format low-pitched roof using manufactured trusses. The low pitch means the rafter lengths are shorter, using less timber, and the manufactured trusses use a web of thinner timbers, again reducing materials costs.
The more complex the roof structure, the more likely it will have to be cut on site, using more labour and timber than factory-made trusses. This will add to costs and take longer to construct. It will also require an engineer to check the design and produce calculations for Building Regulations purposes for a fee (typically £800-£1,200) that would otherwise be covered by the truss manufacturer. More complex roof designs may also require structural steelwork.
It's also worth noting that the steeper the roof gets, the more expensive the roof will be to construct. As a rule of thumb, increasing the roof pitch by 5% will double the cost of the roof, while increasing it by 10% will triple it.
When it comes to roof coverings, developers favour large-format, interlocking concrete roof tiles with a coverage as low as 8–10 tiles/m², keeping labour and materials costs down. Most self-builders choose more attractive, smaller-format tiles made from natural materials such as clay roof tiles or slate. Unfortunately, smaller tile formats will increase labour and material costs.
Current costs (early 2025), including labour and materials:
- Concrete interlocking tiles (typical of those used by the big housebuilders): £45-55/m²
- Natural slate tiles £95-110/m²
- Plain clay tiles £155-170/m²
- Flat roofing £60-80/m²
If you decide to go for decorative details to the ridges or verges, or to use very irregular handmade tiles, this will add 15-25% to the cost of labour and materials.
Walls, floors and ceilings costs
The following costs are based on a typical self-build house (200-250m²), with approximately 110m² first floor area. The standard specification for first floors is to use softwood joists covered with flooring grade chipboard; the cost of which is now £48-55/m² (approximately £5,280-£6,050 total).
Using engineered joists such as I-beams or beams with a steel web such as Posi-joist will add to your costs by £5-£7/m² (£550-£770), but the more regular dimensions and improved stability can help avoid squeaky floors and provide better service void access. These engineered solutions are becoming increasingly popular due to their reliability and ease of installation.
If you are building a masonry or concrete (ICF) house, you could opt for a concrete first floor structure, using either pre-stressed concrete beams infilled with concrete blocks or large-format concrete floor panels. This offers superb strength and acoustic separation, and allows you to have masonry first floor walls throughout. This will cost around £165-220/m² including insulation and 65mm screed. Total cost for 110m² first floor would be £18,150-£24,200.
When it comes to internal walls and ceilings, there is little cost difference between blockwork and timber frame internal partition walls in terms of basic construction, though timber frame often offers faster installation.
Developers looking to keep down costs work with a standard ceiling height of 2.4m. Changing the ceiling height adjusts the average cost/m² for that storey by approximately 1.6% for each extra 100mm (meaning a 2.7m ceiling height on the ground floor adds approximately £9,600 to the total costs based on current prices).
Following industry standards allows you to use industry standard-sized materials such as standard plasterboard sizes on your walls, which helps control costs.
For wall finishes (based on 200-250m² house):
- Standard specification Emulsion paint throughout, with minimal tiling to kitchen and bathrooms at £195/m² (overall floor area) so around £43,000
- Good specification More extensive tiling in the kitchen and bathrooms and wallpaper in the living room at £245/m² (£54,000)
- Excellent specification Also includes wallpaper to the bedrooms and premium tiles at £285/m² (£63,000)
Ceilings are usually covered with plasterboard and finished with a two-coat skim of fine gypsum plaster and emulsion paint at £85-£95/m² (£17,000-19,000).
If you decide to add decorative coving, ceiling roses or other decorative plasterwork, you will need to allow for extra (typically £25-35/linear meter for coving installation).
Costs for a new staircase
Your staircase design is an opportunity to add individuality to a property and to make an architectural statement. If this is your plan, make an additional allowance for this above the new staircase costs allowance included in the standard build costs per square metre.
- Standard specification
- Softwood staircase with two straight flights linked by a half-landing
- Softwood balustrade, painted or stained
- Current cost is around £3,500-£4,000
- Good specification
- Single straight flight in painted softwood
- Enhanced balustrade design
- Current cost is around £4,200-£4,800
- Excellent specification
- Straight flight in hardwood
- Hardwood balustrade with premium finish
- Current cost is around £5,500-£6,500
Costs for adding a chimney
Many modern houses do not include a chimney – especially those built by speculative developers, largely because of the cost and new environmental regulations. While traditional chimneys are becoming less common, when included, costs start at £7,500 for a standard specification.
Many modern houses now opt for alternative heating solutions, but for those wanting a traditional feel, a log burning stove with a stainless-steel flue is popular, with current installed costs around £4,800-£6,000. Note that new regulations require higher efficiency stoves meeting Ecodesign standards.
Current (early 2025) price allowances for different specifications:
- Standard specification
- Basic fireplace and flue system
- Current allowance: £7,500-£8,000
- Good specification
- Enhanced fireplace design and higher-grade materials
- Current allowance: £8,500-£9,500
- Excellent specification
- Premium materials and design features
- Current allowance: £10,000-£12,000
Windows and doors costs
External joinery is another feature that self builders place a great deal of value on, and consequently tend to invest in quite heavily. With current Building Regulations requiring better thermal performance, costs have increased significantly for all window styles.
For external doors and windows, you should consider the below costs:
- Standard specification
- Off-the-shelf painted softwood casement windows
- Double-glazed units (minimum U-value 1.4 W/m²K)
- Factory-fitted aluminium ironmongery
- Current cost is £175-190/m² (£35,000-£38,000 for 200m² house)
- Good specification
- High-performance, off-the-shelf painted softwood casement windows
- Triple-glazed units
- Enhanced security features
- Current cost is £240-£270/m² (£48,000-£54,000)
- Excellent specification
- Double or triple-glazed aluminium window frames
- Hardwood surrounds
- Hardwood panelled front door
- Premium ironmongery
- Smart-home integration ready
- Current cost is £340-£380/m² (£68,000-76,000)
For internal doors, you also have a wide range of price points to choose from. The below costs are based on requiring a total of 16 internal doors.
- Standard specification
- Hardboard-faced hollow-core flush doors
- Softwood frames, hung and decorated
- Basic ironmongery
- Current cost is £650 per door (£10,400 total)
- Good specification
- Enhanced hollow-core flush doors
- Better quality frames and finishing
- Improved ironmongery
- Current cost is £750 per door (£12,000 total)
- Excellent specification
- Hardwood veneered solid-core doors
- Premium softwood frames
- High-end ironmongery
- Sound-proofing features
- Current cost is £900 per door (£14,400 total)
Kitchen and bathroom costs
The cost of a new kitchen depends significantly on the quality, style, and specification level chosen, ranging from off-the-shelf units to high-end bespoke designs.
Prices typically range from £8,500 (budget range, DIY installation) to £75,000+ (high-end bespoke kitchens, professionally installed). Larger kitchens can exceed these figures significantly.
Kitchen ranges typically include the below at the various price points:
- Standard Basic quality units, laminate worktop, standard appliances, basic lighting and a simple layout. £12,000-£16,000
- Good Higher quality units, quartz/granite worktops, branded appliances, enhanced lighting, island units. £20,000-£30,000
- Excellent Bespoke units, premium materials, high-end appliances, smart features, complex designs. £35,000-£75,000+
For bathrooms, plumbing costs remain relatively consistent regardless of the bathroom design you choose, but fixture and fitting costs vary enormously. Quality tiling now starts from £35/m² upwards. Additional features like smart showers, heated towel rails, underfloor heating and luxury baths can significantly impact the final new bathroom costs.
- Main bathroom (includes WC, basin, bath, additional plumbing, doors, walls, windows and finishes)
- Standard quality: £7,500
- Good quality: £11,000
- Excellent quality: £16,500
- Shower room (includes WC, basin, shower cubicle, doors, walls, windows and finishes)
- Standard quality: £7,800
- Good quality: £11,500
- Excellent quality: £17,000
- Cloakroom (includes WC, basin and additional plumbing, doors, walls, windows and finishes)
- Standard quality: £4,000
- Good quality: £5,500
- Excellent quality: £7,500
Flooring costs
For flooring, you should typically budget around £60/m² for standard finishes, £85/m² for good standard flooring and £120/m² for excellent quality.
Everything from wood flooring costs to LVT flooring costs will vary depending on the supplier and quality of the materials. As a rough guide, however, typical flooring costs for a range of materials are as follows:
- Contract-quality carpet £45-65/m²
- 100% wool carpet £65-85/m²
- Laminate (wood effect) £45-65/m²
- Engineered oak flooring £110-140/m²
- Reclaimed pine floorboards £85-110/m²
- Natural stone flags £120-160/m²
- Ceramic/porcelain tiles £70-95/m²
Complete heating and hot water system costs
The cost range represents variations based on house size, equipment choices, regional labour rates, and installation complexities.
- Option 1: Gas Boiler, Radiators and Domestic Hot Water (DHW)
- Gas combi/system boiler: £4,000-£7,500
(Includes hot water cylinder and controls) - Radiators: £4,500-£6,000
- Total: £8,500-£13,500
- Gas combi/system boiler: £4,000-£7,500
- Option 2: Gas Boiler, Underfloor Heating and Domestic Hot Water
- Gas combi/system boiler: £4,000-£7,500
(Includes hot water cylinder and controls) - Underfloor heating: £10,000-£15,000
- Total: £14,000-£22,500
- Gas combi/system boiler: £4,000-£7,500
- Option 3: Oil Boiler, Underfloor Heating and Domestic Hot Water
- Oil Boiler and Tank: £7,500-£12,500
(Includes hot water cylinder and controls) - Underfloor heating: £10,000-£15,000
- Total: £17,500-£27,500
- Oil Boiler and Tank: £7,500-£12,500
- Option 4: Air Source Heat Pump, Underfloor Heating and Domestic Hot Water
- ASHP system: £18,000-£25,000 and DHW
(Includes integrated or separate hot water cylinder – typically 200-300L cylinder for average home) - Underfloor heating: £10,000-£15,000
- Total: £28,000-£40,000
- ASHP system: £18,000-£25,000 and DHW
- Option 5) Ground Source Heat Pump, Underfloor Heating and Domestic Hot Water
- GSHP system: £28,000-£38,000
(Includes hot water cylinder and controls, ground works and all pipework) - Underfloor heating: £10,000-£15,000
- Total: £38,000-£53,000
- GSHP system: £28,000-£38,000
- Optional Solar Thermal Addition
- Solar thermal system: £4,000-£7,000
(Can reduce Domestic Hot Water costs by 40-60%. Works with any of above systems)
- Solar thermal system: £4,000-£7,000
- Annual Running Costs (Including Domestic Hot Water):
- Gas System: £1,100-£1,400
- ASHP: £850-£1,200
- GSHP: £700-£1,000
Most new homes will now need Mechanical Ventilation with Heat Recovery (MVHR) in order to be able to achieve the required energy performance under the latest Building Regulations.
Typical MVHR costs for a house under 150m² is £8,500-£10,000. For larger houses, expect to pay £10,000-£13,000.
Electrics costs
Standard costs do not vary much from house to house other than by scale. If you decide to fit anything out of the ordinary (e.g. a whole-house structured cabling network), you will need to make an allowance for these upgrades.
Standard | £120–£150/m² |
Good | £150–£185/m² |
Excellent | £185–£250/m² |
LED downlights (for seven) | £300-£600 |
Structured cable network/room | £150-£300 |
Smart home audio system/room | £800-£1,500 |
Smart lighting circuits/room | £400-£600 |
Security system with cameras | £1,200-£3,000+ |
EV charging point | £800-£1,500 |
Smart home hub integration | £1,500-£3,000 |
How much does a project manager add to the cost of building a house?
In order to get a building site to run smoothly, someone has to manage the processes, but what's the right self build project management route for you? A project manager has to ensure that the right people are hired in the right order and that the correct materials are on site as and when needed, as well as checking that the work is carried out properly and that the site is left clean and safe everyday.
The average build costs are based on the cost of using a main contractor to manage the whole build. They will:
- Co-ordinate and pay for the trades, materials, plant, tools and scaffold required
- Liaise with the architectural designer or you the client on design decisions
- Co-ordinate the statutory inspections for Building Regulations and warranty
- Take legal responsibility for the site in terms of health and safety
- Manage the build quality and programme
- Insure the project for all risks during the construction phase
If you take on this role by hiring subcontract labour directly, providing materials and facilities as required, you can reduce the build cost by 10-15% depending on how efficiently you manage the project.
Approximately 35% of the total cost of building a house is labour, so if you decide to substitute some or all of the labour costs with your own DIY labour, you can reduce the average build cost substantially.
You can undertake almost every aspect of the building work if you have the time and skill to complete it competently, except for connecting gas appliances.
Trades more easily undertaken by the DIY self builder include:
- Carpentry
- Fitting insulation
- Roof tiling
- General labouring
- Assisting plumbers and electricians on second fix
- Decorating
- Floor laying
- Tiling
- Landscaping.
Typical savings for a DIY self builder doing roughly 25-30% of all the work amount to 20-25% of the total cost compared to using a contractor.
Average construction cost £/m² by build route (excluding VAT) are as follows:
- DIY Route: £1,000-£1,600/m²
- Requires significant personal time commitment
- Highest potential savings
- Longest build time
- Requires strong project management skills
- Most risk but highest cost saving potential
- Self-Managed: £1,600-£2,200/m²
- You act as project manager
- Hire individual trades
- Coordinate deliveries and scheduling
- Medium risk level
- Good potential for cost control
- Main Contractor: £2,000-£2,800/m²
- Single point of responsibility
- Less personal time commitment
- Professional management
- Lower risk
- Higher costs but more predictable
- Design and Build: £2,300-£3,500/m²
- Turn-key solution
- Least personal involvement required
- Lowest risk
- Includes professional fees
- Highest cost but most convenience
On larger projects, a professional is usually retained to put the project out to tender, appoint the contractor and administer the contract through to completion.
The fee for this is typically 3-5% of the total contract value (construction cost). If you take on this role yourself you can save this fee (which isn’t included in the base figures £/m²).
Additional costs for building a home
The following costs are typical of a self build project and often omitted from a construction budget.
- Topographical Survey of Site £600-£1,000
- Design Fees
- Architect fees 7-15% of build cost (design and contract administration)
- Planning drawings: £3,500-£6,000
- Building Regulations drawings: £3,500-£6,000
- Structural engineer: £1,500-£3,000 - Planning Fees £462 plus Portal Fee for single new dwelling (England)
- Building Regulations Fees £1,000-£3,500
- Warranty 1% of construction value
- Self-Build Insurance 1% of projected costs
- Utility Connections £15,000-£25,000
- Demolition (if existing dwelling present on site): £10,000-£15,000
- External Works/Landscape allow 15% of total build cost
- Preliminaries 10% of construction costs (skips, site welfare, muckaway etc).
- Site Investigation Costs
- Soil Investigation/Ground Conditions Survey around £1,000-£2,500
- Archaeological Survey (if required) is £2,000-£5,000
- Tree survey (if required) is around £450-£850 - Legal fees
- Conveyancing: £1,500-£3,000.
- Legal agreements with neighbours (Party Wall etc.): £700-£2,000 per neighbour
- Title insurance (if required): £300-£500 - Finance Costs
- Mortgage/finance arrangement fees: 0.5-2% of loan amount
- Stage payment valuations: £150-£300 per visit
- Project management software/tools: £200-£500 - Professional Services
- Quantity surveyor: 1-3% of build cost
- Project manager (if required): 5-10% of build cost
- CDM principal designer: £1,000-£2,500
- SAP Assessments: £200-£500
- Air Pressure Testing: £300-£500 per test
- Party walls surveys: £900-£1,500 per neighbour (double if the neighbour insists on appointing their own surveyor) - Local Authority Requirements
-Section 106 Agreements (if applicable). Check for any detail on additional contributions within the planning decision notice
- Community Infrastructure Levy (CIL): apply for self build exemption
- Highways Agreements (if required): £2,000-£5,000 - Site-Specific Costs
-Temporary site access: £1,000-£3,000
- Site security during build: £200-£500 per month
- Temporary power supply: £500-£1,500
- Site toilet facilities: £100-200 per month - Environmental Considerations
- Ecological survey: £500-£2,000
- Bat survey (if required): £500-£1,500
- Flood Risk Assessment (if required): £600-£1,500
- Energy Performance Certificate: £200-£400 - Post-Construction
-Professional deep clean: £500-£1,000
- Snagging survey: £300-£600
- Building Control sign-off fee: £200-£500 - Contingency
Allow 10-15% of total budget for unexpected costs including 5% allowance for inflation - Moving Costs
-Storage during build: £100-£200 per month
- Temporary accommodation: Mortgage, rent, mobile home etc.
- Removal Services: £1,000-£2,000
FAQs
What factors have an impact on build cost?
The bigger the house, the more it will cost to build, but there can be some economies of scale that reduce the average cost/m² for larger houses, making a carefully-designed large house better value.
The cost efficiencies of a large house are mainly in the cost of building the superstructure, especially the foundations, walls and roof. The cost/m² of gross floor area for external walling elements decreases as the wall/floor ratio decreases.
Other one-off unit costs for items such as service connections, staircase, kitchen and boiler are spread out further on a larger house. To maximise efficiency, the design needs to be kept simple and avoid unusually large spans for floor joists/beams, rafters etc.
The specification and cost for a set footprint and roof layout will not vary by adding storeys above, yet the gross internal area will increase dramatically – spreading out the cost. Multiple storeys also make better use of land, which is typically the most expensive element of all.
In areas where land values are particularly high, adding a basement storey is also worth considering. The cost of building a storey below ground level is higher than above ground, primarily due to the cost of excavating and removing spoil to landfill, plus the cost of waterproofing and pumped drainage. This is mitigated to some extent by the fact that fewer windows are usually used than for above-ground storeys, and there is no external wall cladding (e.g. brick or stone). Depending on ground conditions a basement will cost 50-100% more per square metre than above ground space and in very complex sites with limited access, costs can increase by 200%.
Are house construction costs still inflated post-pandemic?
The extreme volatility in construction costs that characterised 2021 has largely subsided, although prices haven't returned to pre-pandemic levels. Whilst the dramatic 23% year-on-year increases have been replaced by more modest 2-3% annual rises, we're experiencing a new 'normal' with higher baseline costs.
Key materials such as timber and steel have stabilised, with supply chains now functioning more predictably, whilst concrete continues to see moderate inflation of 3-4% annually.
Labour costs continue to rise at 4-5% per year due to persistent skilled workforce shortages, though training programmes are helping to address these gaps. Brexit-related supply chain issues have largely been resolved through new processes, and international shipping costs have normalised. Energy costs, whilst still high, have stabilised compared to the 2022-23 spike, making manufacturing costs more predictable.
For current projects, it's advisable to add a 5% contingency for material price fluctuations. The market now offers more reliable delivery schedules and stable tender prices, making project planning more manageable than during the turbulent 2021-2022 period. Whilst overall costs remain about 15-20% higher than pre-pandemic levels, the improved predictability allows for better forward planning and more accurate budgeting.
The above costs are all a great starting point when planning your self-build journey, but do keep in mind that building a house is a unique process and every plot and project is different.
Ensuring your new home is tailored to your exact needs means you may choose to spend more money on certain elements than others, but that's all part of the process when managing a self-build. What's more, the quality of fixtures and fittings you choose will be a major factor in the final cost.
Bring your dream home to life with expert advice, how to guides and design inspiration. Sign up for our newsletter and get two free tickets to a Homebuilding & Renovating Show near you.
Michael is Homebuilding & Renovating's Director of Content, Vice Chair of the self build industry body, the National Custom and Self Build Association (NaCSBA), presenter of multiple property TV shows and author of Renovating for Profit (Ebury). He also runs an architectural and interior design practice, offering design and project management services. He is one of the country's leading property experts and has undertaken over 30 building projects including two self-builds and the renovation of a Grade-II listed farmhouse.
Michael has presented over 150 property shows for BBC, ITV1, Channel 5, UK TV Style, and Discovery RealTime, including I Own Britain's Best Home; Don't Move Improve; Trading Up; Good Bid, Good Buy; Build, Buy or Restore?; How to Build A House; and Hard Sell.
Michael is also a regular expert at the Homebuilding & Renovating Shows. He has written for leading British newspapers, including The Daily Telegraph, Sunday Times, Daily Express and The Independent and has appeared on news programmes such as BBC Breakfast.