Timber vs masonry: Which building system should you choose?
With timber and masonry the most popular methods for building houses and extensions, how do they compare when it comes to efficiency, safety and environment?
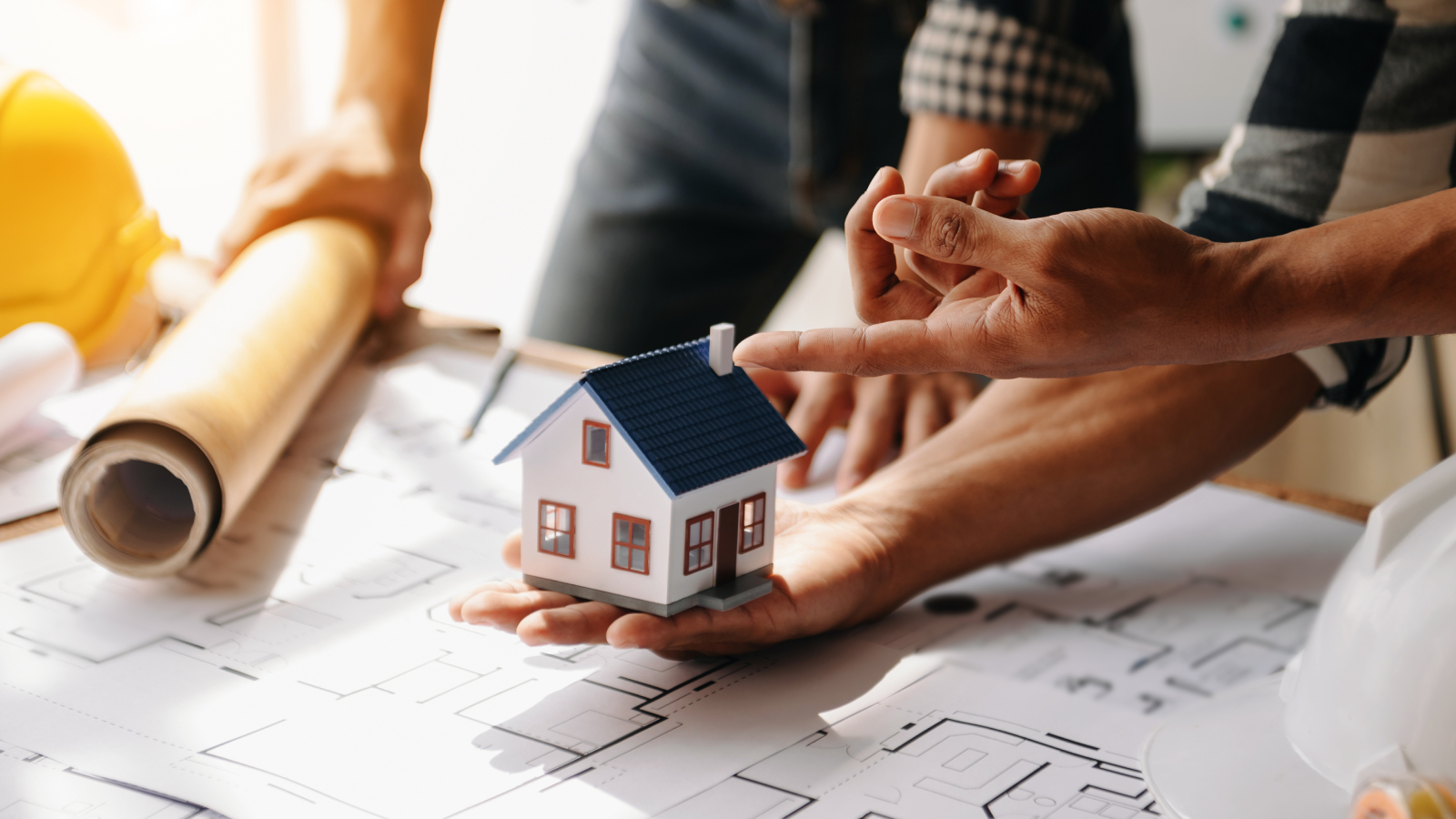
When it comes to creating a superstructure, building a house or extension is typically completed with either structural timber or masonry such as brick and block.
Structural timber is the most popular choice, with a market share of 40%, while brick and block has 30% of the market share, according to the National Custom and Self Build Association.
Masonry-based building systems are popular because of the ease with which they can be used. They are well understood by most designers and building contractors, and have proven reliable over hundreds of thousands of homes and over many decades. While they might be a relatively slow building method compared with timber systems, the materials are cheap and readily available.
Here our expert, Mark Stevenson, compares the two different superstructure build systems: timber vs masonry, looking at the pros and cons of each.
Timber vs masonry
While there are obvious differences between concrete and timber as building materials, the principal difference as a system is in how the materials are used.
Timber frame systems are built off-site, in quality-controlled environments and are therefore away from the critical path of the build programme. The fact that the house comes delivered on the back of a lorry and is rapidly erected on site speeds up the construction process and enables internal trades to start sooner.
In comparison, masonry homes are built on site, literally block by block, and are exposed to the prevailing weather conditions and the skill of the trades involved. This slows down the building process and requires a greater degree of supervision to make sure there aren’t any workmanship issues and keep building inspectors happy.
Below, we compare the two systems in depth looking at the key considerations, including energy efficiency, fire safety and green credentials.
1. Energy efficiency
With the implementation of the new Part L of the Building Regulations, buildings need to have lower U values, reduced thermal bridging and improved airtightness. Self-builders are now typically looking for airtightness levels below 3 m3/(m2·h) @50 Pa.
Whilst timber building systems incorporate membranes to achieve this, blockwork is inherently leaky and will require secondary treatments to reduce air leakage and meet the requirements of the regulations.
If you understand what a thermal bridge is, you'll know it's all about detailing. U values are about thickness and resistance and given the poor thermal resistance of concrete, you can expect walls built from bricks and blocks to be thicker than the comparable timber frame or structural insulated panel (SIP) alternatives.
2. Fire safety
The fire resistance of building systems to prove that they resist the spread of fire and provide the necessary evacuation time is increasingly being questioned by regulators.
Combustible materials such as timber should therefore be subjected to an EN 1365 fire resistance test for load bearing elements. In terms of blockwork, it’s deemed as non-combustible so won’t have to go through the same test.
However, self-builders shouldn’t be lulled into a false sense of security as masonry houses commonly adopt the same joisted intermediate floors, which will need to prove their fire safety to EN1365.
3. Health and safety
Health and safety regulations and in particular CDM (Construction design and management regulations 2015) requires consideration to eliminate or manage the health and safety hazards involved in a construction project.
While concrete blocks, as a non-combustible building material, won’t burn and will easily deal fire in construction risks, the highly repetitive and heavy work of laying blocks along with the risk of breathing in silica dust when cutting them means that there are health and safety concerns.
On top of this, if the home takes more than 500 person days to build, you will have to notify the HSE (Health and safety executive) that your project exists. As masonry takes longer to build, you’re more likely to have to do this.
4. Embodied carbon
House building has a sustainability problem and the materials it consumes makes a significant contribution to global warming. Concrete is one of the main culprits and according to Imperial College London, every tonne of cement emits 622kg of carbon dioxide.
In comparison, for every dry ton of manufactured timber, around 1.8 tons of CO2 is removed from the atmosphere.
While I don’t think the choice between structural timber and concrete blocks is as simple as this stark comparison, it is clear that for the eco-conscious self-builder, timber is a more sustainable choice.
Still searching for inspiration for your self-build or extension project? Take a look at some rear extension design ideas or browse our timber frame homes gallery to see if building with timber could be right for you.
Get the Homebuilding & Renovating Newsletter
Bring your dream home to life with expert advice, how to guides and design inspiration. Sign up for our newsletter and get two free tickets to a Homebuilding & Renovating Show near you.
Mark Stevenson has worked as a construction professional for over 30 years and following an extensive career in housebuilding. He is currently chief operating officer for Custom Build Homes and chair of the National Custom and Self Build Association. He previously worked as managing director for Potton, helping self builders build their own homes.
Whilst Mark describes himself as a ‘professional builder’ as a result of his career in housebuilding and timber building system manufacturing, he has specialist knowledge of timber construction and extensive expertise in finding land and project management.
He regularly shares his knowledge at Homebuilding & Renovating Shows and and coaches self builders about how to build their own homes. Aside from Mark’s professional career, his skills also extend to practical building knowledge as a skilled joiner, hands-on renovator and serial self-builder of his own development projects.
He is also Vice Chair of industry body, the Structural Timber Association.