Timber frame vs SIPs: Weighing up which is best for your build
Looking at timber frame vs SIPs is increasingly common amongst both self builders as well as those looking to extend – but which construction method is best for you? Expert Mark Stevenson is here to explain everything you need to know
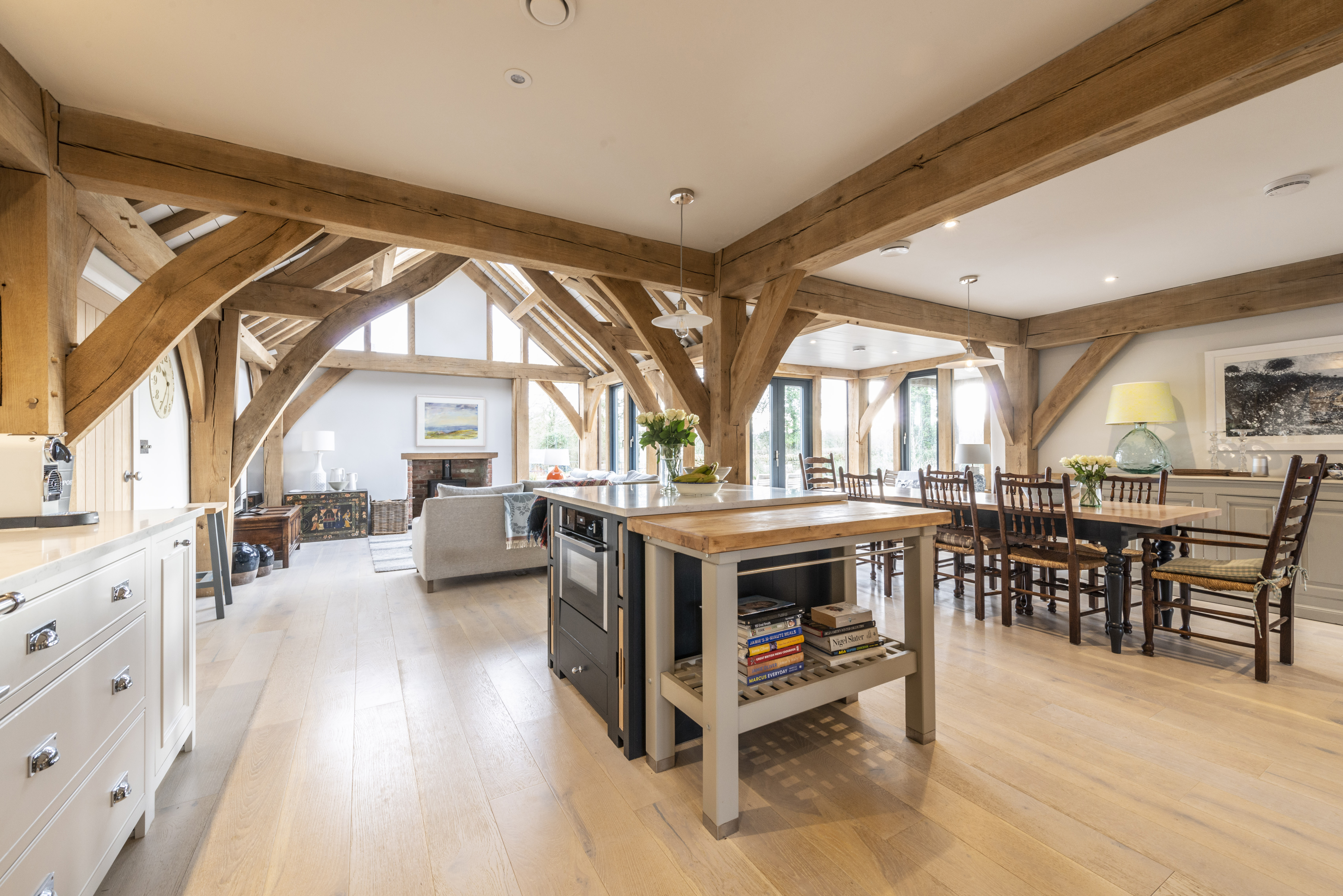
Weighing up timber frame vs SIPs is becoming increasingly popular for self builders to consider when selecting the best construction methods for their new home.
If you are considering the self build option you will probably be aware that there are many ways to build a new home or extension project, but the most popular is to use a timber building system. According to the National Custom and Self Build Association, over 40% of all self builders opt to build with structural timber and as we progress to a ‘low carbon future’, their popularity is set to rise.
SIPs are thought of as the next generation of timber frame, offering improved thermal performance. However, with recent technological advances, timber frames have reduced the performance gap.
In this article, expert Mark Stevenson explains everything you need to know about timber frame vs SIPs, including how each system compares when it comes to cost.
Timber frame vs SIPs means firstly understanding what is a timber building system
When thinking about how to choose a construction system it is useful to know that a timber building system forms the structural chassis for your build. It includes all the building elements – walls, floors and roof, to form a coherent engineered building structure.
Its popularity isn’t just down to its low carbon credentials – a timber building system is affordable, fast and easy to build with, offers high levels of quality and energy efficiency and has the potential to unlock architectural freedom by exceeding regulatory standards.
On face value, they’re the go-to building solution but, dig a little deeper, and you’ll soon find not all timber systems are the same.
The two principal choices are timber frame or structural insulated panels – known as SIPs – and here’s the key differences you need to know when considering timber frame vs SIPs.
What is a timber frame?
Modern timber frames have been around for over 50 years and are made with timber studs that are nailed together with a sheathing of oriented strand board (OSB/3). These walls are commonly manufactured in factories to form a closed panel that includes all the insulation and vapour control layers to meet the energy efficiency requirements.
Subsequently, timber frames are high performance building systems and incorporate insulation liners and airtightness membranes to reduce thermal bridging and control air leakage.
What are Structural Insulated Panels (SIP)?
An evolution of a timber frame, SIPs are constructed from two layers of OSB which are bonded to a core of insulation to form an incredibly strong panel. This can then be used to construct walls and roofs.
SIPs are joined together with a unique joint of either structural timber or insulated splines which improves airtightness and reduces thermal bridging.
How do insulation and energy efficiency compare?
Both timber frame and SIPs offer high levels of thermal performance. With U values typically around 0.15 W/m2k and as low as 0.09 W/m2k, and, depending on the insulation used, both systems easily meet the latest building regulation requirements.
SIPs must have an insulation core with structural properties to bond to the OSB skins and carry imposed loads. Typically these are polyurethane or polystyrene which have a thermal conductivity ranging from 0.024 W/mK. to 0.036 W/mK, with the latter requiring slightly thicker walls to achieve the same U-value.
A particular advantage of SIPs insulation is the closed cell nature of the material which resists moisture penetration and is very durable in wet conditions. With the unique panel jointing system and insulation bonded to the OSB, air gaps are eliminated reducing thermal bridging and the risk of thermal bypass - an issue if insulation is fitted poorly in timber frames.
As the insulation within timber frames is not structural, there’s a greater range of choice. This makes it possible to use higher performing materials or natural types of eco insulation which are purported to be greener, and provide a healthier internal environment.
However, sheep’s wool or recycled newspaper doesn’t have the best thermal properties so expect energy bills to be higher.
In my experience, one of the standout virtues for SIPs is airtightness. Whilst it’s possible to achieve low levels of air leakage with both systems, it’s much easier with SIPs due to the unique jointing methods and the fact that the system is formed with bonded OSB and insulation, removing air gaps.
SIPs are also very robust and resilient during construction and ideal for builds that require Passivhaus performance levels.
How does the carbon footprint of timber frame vs SIPs compare?
Timber is widely considered as the most sustainable mainstream building material with the lowest embodied CO2 of any commercially available products. Compared to the masonry equivalent, the embodied carbon of sustainably sourced timber is up to 82% less.
While the embodied carbon of SIPs and timber frame will be very similar, operational carbon (how energy efficient it will be in use) also has to be considered.
The good news here is that both systems have the potential to offer a very low carbon footprint and, provided they’re complimented with an energy efficient design and high performance products such as different types of energy efficient windows and doors, both have the potential to exceed regulations, achieve Passivhaus standards or even meet the RIBA 2030 climate challenge.
Do both systems meet planning consents and building regulations?
Firstly, let's dispel the notion that planning permission will dictate the build system for your home – it won’t and there isn’t an enforceable planning condition that dictates what you must build with.
Building systems must comply with the building regulations and the underpinning standards and codes. The main ones to consider are Approved Document L, conservation of fuel and power, and Approved Document A, which deals with the structure.
In terms of building structure, both timber frame and SIPs will deliver the required level of structural stability, but as SIPs are novel systems with their own structural performance data, expect a few more questions from building control when they check the structural calculations.
Timber frame vs SIPs - which is quicker to build with?
Timber systems are popular with self builders because of the ease and speed of build and, to be honest, there’s little difference between timber frame and SIPs. Both are manufactured off site and will be rapidly erected on site.
Expect the build of the structure for an average house to take around 4 to 6 weeks. However, throw in a complex architectural design, a complex roof or lots of structural steel, and the build will slow up. Both systems can be manufactured in small panel formats so are suitable for those building an extension where access is tricky.
SIPs are great for forming rooms in the roof, so if your home design includes these, you may shave a few days off the build compared with trussed rafters.
Is a timber frame cheaper than SIPs?
As with all things in life, you get what you pay for and a higher performing building system will cost more.
When timber frame and SIPs are compared, pound for pound, SIPs will cost slightly more, but there are benefits which may be worth paying for – certainly something to consider when looking into how to build a SIPs home.
Commoditisation and competition also plays a part so if you’re prepared to shop around and be a bit more flexible about what you buy, you’ll likely be able to find a supplier of SIPs that’s less expensive than a premium brand, advanced timber frame.
System & Cladding | Per m2 | Per Project |
---|---|---|
Basic timber frame & brick | 100% | 100.00% |
Higher performance timber frame & brick | 107% | 101.40% |
SIPs & brick | 116% | 103.20% |
*Assuming the structure is circa 25% of the project value
When comparing building systems, the choice for the majority of people still comes down to timber vs masonry. Both are still great choices, but for those looking for a more sustainable way of building a house, timber tends to come out as the winner.
Bring your dream home to life with expert advice, how to guides and design inspiration. Sign up for our newsletter and get two free tickets to a Homebuilding & Renovating Show near you.
Mark Stevenson has worked as a construction professional for over 30 years and following an extensive career in housebuilding. He is currently chief operating officer for Custom Build Homes and chair of the National Custom and Self Build Association. He previously worked as managing director for Potton, helping self builders build their own homes.
Whilst Mark describes himself as a ‘professional builder’ as a result of his career in housebuilding and timber building system manufacturing, he has specialist knowledge of timber construction and extensive expertise in finding land and project management.
He regularly shares his knowledge at Homebuilding & Renovating Shows and and coaches self builders about how to build their own homes. Aside from Mark’s professional career, his skills also extend to practical building knowledge as a skilled joiner, hands-on renovator and serial self-builder of his own development projects.
He is also Vice Chair of industry body, the Structural Timber Association.