The Evolution of Composite Windows
Since the 1970s, the composite window has undergone many technological advancements
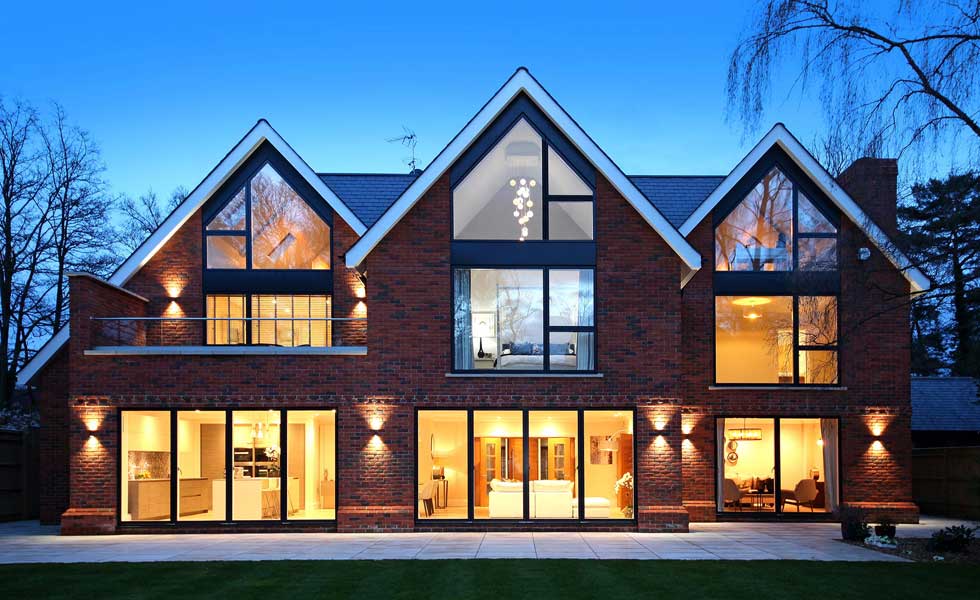
CONTENT SUPPLIED BY IDEALCOMBI
Windows is one area where self builders and renovators can see the most technological advancement, not only meet efficiency standards that all new homes have to meet, but also to ensure that there is a window solution flexible enough to meet requirements and tastes of homeowners.
Here we take a look at how the composite window has changed over the last 50 years.
1970s
In the 1970s a window was mainly made of timber, both the frame and the sash. Timber was (and still is) a fantastic material for windows:
- it’s easy to work with
- has great thermal properties
- lasts for years with the correct maintenance. Maintenance, however, can be quite time consuming.
1980s
In the 1980s aluminium cladding was introduced to protect the timber from the elements. This minimised the need for regular maintenance (in terms of painting the exterior of the window) as powder-coated aluminium lasts much longer than painted timber.
But water still gathered in the frame rebate and caused the timber to rot, if not maintained correctly. Some window manufacturers replaced some of the timber rebate with aluminium to solve that problem.
The extra aluminium, however, acted like a thermal bridge reducing the thermal efficiency of the window.
2000s
In the 2000s thermal breaks were introduced between the timber and aluminium, drastically improving the thermal performance whilst maintaining the durability of the aluminium-clad window.
This was a big step forward for the composite window design and is still widely used to this day.
However, the necessary drainage channels, cavities and ironmongery grooves proved to be perfect nesting places for bugs and dirt to collect. This meant that drainage holes and channels would eventually get blocked and lead to standing water in the window construction.
Over time water will find its way to the timber which will then start rotting.
2010
In 2010 an alternative thermal break, PUR (Polyurethane), found its way to the window market.
PUR is widely used, not only in the construction industry but across all areas of manufacturing. PUR can either be a soft or a rigid foam and, filled with tiny air bubbles, it has twice the insulating properties of timber. It is imperishable, waterproof and does not need any maintenance.
Benefits of polyurethane foam include:
- good insulative properties
- keeps water away from the timber frame
- is solid with no cavities or drainage channels to keep clear (allowing sealant to be applied further to the front of your building, keeping water away)
- is maintenance free (and thereby vastly extends the lifetime of the entire window)
Idealcore
The polyurethane foam used in composite windows is also known as idealcore.
Idealcore was developed by Idealcombi on the Danish west coast, where it rains more, is colder and windier than in the rest of Denmark.
Since 2010 Ideacombi has used idealcore in their contemporary window series Futura+ followed by Futura+i in 2014 and in the traditional window series Frame IC and Nation IC in 2015.
For more information about Idealcombi, visit the website.
Get the Homebuilding & Renovating Newsletter
Bring your dream home to life with expert advice, how to guides and design inspiration. Sign up for our newsletter and get two free tickets to a Homebuilding & Renovating Show near you.