Soundproofing Regulations: Part E
If you’ve ever experienced the stress of domestic noise pollution, you’ll understand why the Building Regs set out clear requirements for soundproofing. We look at what you need to know to keep you (and your neighbours) happy
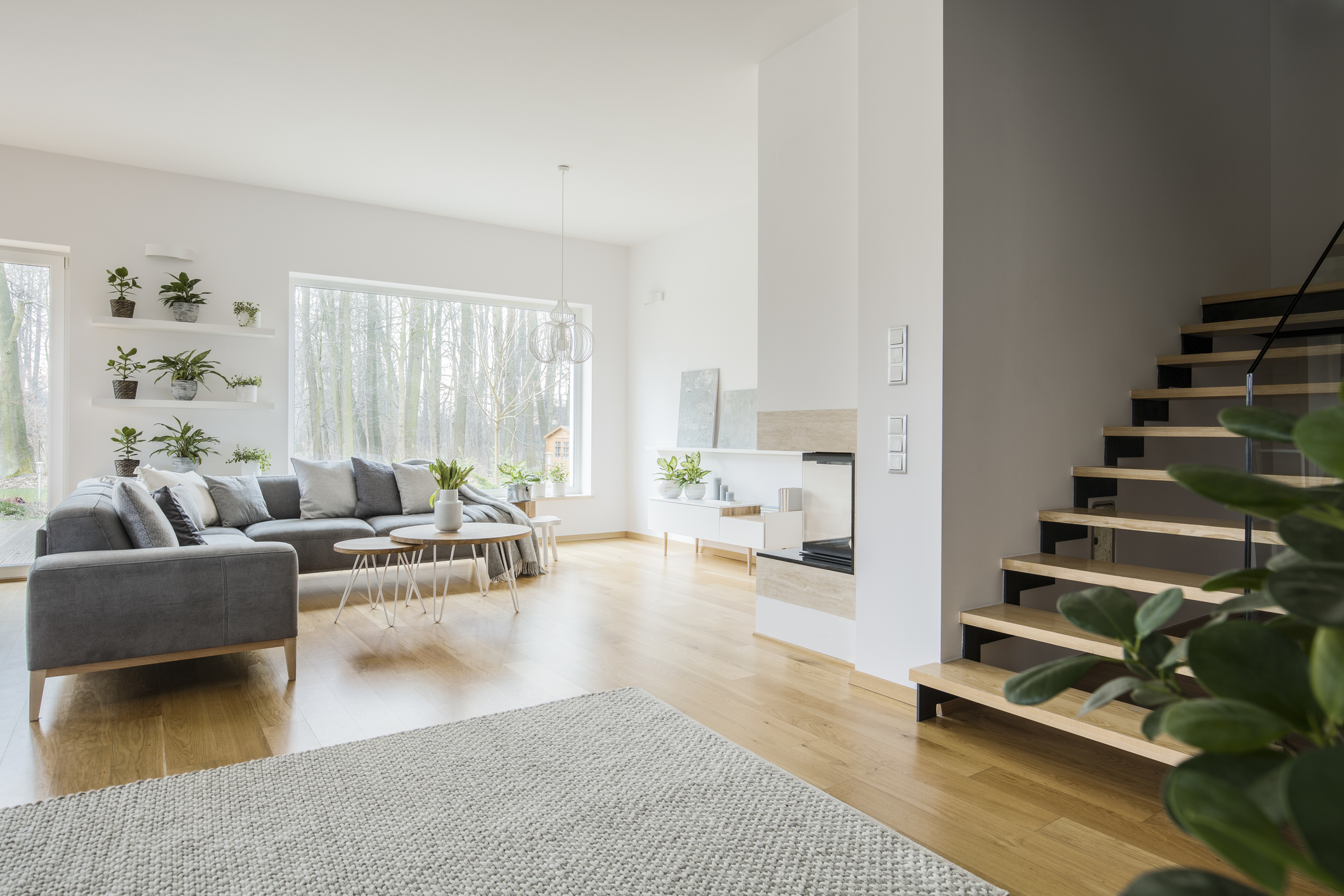
Part E (Resistance to Sound) of the Building Regulations sets out the soundproofing standards for new homes and conversions. It deals with dividing walls and floors, and also requires some sound insulation internally to protect bedrooms from noise.
The Regs, which cover England and Wales, are split into two sections:
- E1 looks at protection from noise from adjoining buildings including flats, terraces and semis
- E2 deals with sound transmission within the home itself
The Regulations also divide sound into airborne sound and impact sound:
The minimum level of airborne sound resistance for dividing walls or floors between homes is 45dB (decibels) in new builds and 43dB in conversion projects. This level should easily cut out normal levels of speech, TV and music playing.
Under the regulations, the internal airborne sound resistance inside any dwelling must be a minimum of 40dB. It applies to walls and upper floors between bedrooms and other rooms.
There is one exception: any wall that has a door in it and walls to en suite bathrooms.
For impact sound such as footsteps, jumping and dropped objects, a maximum impact sound transmittance level of 62dB is set for floors and stairs in new builds. A maximum of 64dB is set for conversion projects.
What if the Property is Detached?
New detached homes do not need to meet the more stringent Building Regs acoustic standards set for new attached homes such as semis, terraces and flats.
For attached homes, developers have the choice of following Robust Standard Details (a set menu of compliance standards) or carrying out on-site sound tests on dividing walls between homes.
Why is Sound a Problem?
Sound looks for the path of least resistance. It can leak unexpectedly though tiny gaps and holes (such as service entry points for plumbing and electrics) or vibrate along fixing screws, bolts and nails. They are all pathways for sound transmission.
Even when you build a sound-resistant wall or floor, noise can find a route around it. Sound can bypass a sound-resistant wall or floor via an adjacent one and this is known as flanking transmission. It’s more common than you might think.
Common Paths for Noise
- Chimneys (where flues serve open fireplaces between sound-resistant floors)
- Service entry holes, for example, for plumbing pipes and wiring
- Cutting in socket outlets back to back on walls, reducing the structure between them
- Un-pointed mortar joints with gaps and holes
- Lack of an isolating void between ceiling boards and floor joists
- Hard floor coverings without an isolation material between them and floor boards.
How to Combat the Problem
Given our fondness for timber frame and lightweight block walls for thermal insulation, the inner leaf of a cavity wall is an easy route for flanking transmission to bypass a sound-resistant wall or floor.
Overcoming it in timber frame homes usually means double lining the walls with heavier plasterboards internally. The same process can also be needed for the super light blocks used on inner leaves.
The size and position of window and door openings can also add inadvertently to flanking transmission. Vibrations can be sent through the masonry wall between them, passing across the abutting sound-resistant wall. To tackle this, ensure the wall is short, no more than 700mm between the openings, because short walls don’t vibrate as much.
How to Soundproof Upper Floors
The traditional upper floor structure, consisting of timber joists covered by chipboard boarding and a thin layer of plasterboard ceiling, offers little sound resistance. By itself, it won’t achieve the minimal standard requirement of the Building Regulations for bedrooms, of 40dB.
For that, you can either:
- Add insulation material between the joists — 100mm of mineral wool of at least 10kg/m3 density
- Upgrade to a heavier plasterboard of at least the same mass.
It’s a minimum for bedrooms only, but upgrading the whole floor structure is the easiest and most effective choice. It is possible to improve it more to achieve a desirable standard that will cut out airborne sound from a TV or music with just a bit more expense.
Unlike walls, floors can transmit impact sound as well as airborne sound. Although there is no requirement to deal with this under Building Regs, the best way to deal with it is to provide some isolation between the joists and floor boarding.
For instance, resilient layer materials that come on a roll can be pinned to the joists before flooring is laid. They simply float on top with the tongued joints glued into each board — no other fixing is required. To screw or nail it down would actually create a sound path!
These resilient layers are usually between 6mm and 12mm, depending on the material. Often it is foam plastic or rubber based. The skirting boards will pin it in place via an acoustic flanking strip, and this will avoid direct contact between the skirting and the floor boarding.
With the insulation between joists being denser than the thermal insulation quilt, it should tackle airborne sound.
To upgrade the performance, resilient layer materials can be supported on sound-quality plasterboard planks that are themselves laid as shelves on battens fixed to the side of joists. The more you use in thickness terms of both plasterboard and insulation, the greater the density and the better the resistance to airborne sound.
If you can afford the headroom, a secondary suspended ceiling formed beneath the floor joists is ideal. This ceiling, supported by new timber joists that span from wall to wall, is not in contact with the joists above. A minimum gap of 25mm is advisable.
Two layers of 15mm sound-quality plasterboard can amount to 26kg/m2, so check the joists’ size and spans. Use acoustic silicone sealant or tape to seal around the perimeter edges to achieve airborne resistance of 45dB or more.
How to Soundproof External Walls
Typically timber frame homes are insulated with PIR insulation foam boards between the timber studs for thermal insulation but these are poor sound insulators.
If you value your privacy or your sleep, you might consider building in some external sound insulation, although this isn’t a requirement of the Building Regs.
To upgrade the external walls:
- use dense mineral wool slabs to insulate between the studs and an inner layer of thermal multi-foil laminate for thermal insulate
- then double board with a sound or fire-rated plasterboard lining.
This will achieve high levels of both sound and thermal insulation, as well as great fire resistance.
Meanwhile, the Building Regulations’ Part Q security standards for windows and external doors can be met using laminated glass outer panes. Luckily, these also provide better sound insulation by having a thicker outer pane than inner pane in double glazing, displacing sound waves.
Soundproofing Masonry Dividing Walls
Two skins of pointed-up dense blockwork in a 100mm cavity wall filled with mineral fibre will usually meet the airborne sound insulation requirement. Adding a sound grade plasterboard will improve sound resistance to over 50dB. To achieve thermal insulation requirements, apply a soft thermal layer before plasterboarding.
Soundproofing Internal Stud Walls
Stud walls seem to be the exact opposite of what you’re striving to achieve: a solid and robust separation with high levels of fire and sound resistance.
- Thermal relies on soft and squidgy insulation with air pockets to trap the heat in
- Sound relies on dense materials to add mass to the wall and air separation to keep airborne sound out.
If you have room for a double timber stud compartment wall, use at least a 240mm cavity width. That is measured between the inner faces of plasterboard on both sides. So if you’re using 100mm deep timber studs, the distance between the studs will reduce the cavity here to 40mm.
Semi-rigid mineral wool insulation can then be installed between each stud and covered by two layers of plasterboard to each face:
- The first is a 19mm thick plank
- The second is a 12.5mm sound-resisting plasterboard.
With attention to detail and good workmanship, such constructions should offer good airborne sound insulation.
Get the Homebuilding & Renovating Newsletter
Bring your dream home to life with expert advice, how to guides and design inspiration. Sign up for our newsletter and get two free tickets to a Homebuilding & Renovating Show near you.
Paul is a Chartered Building Engineer and has been a building control officer since 1984. He has written eight books on home improvements and building homes, including the Complete Handbook of Home Extensions and Creating an Eco-Friendly Home & Workplace. He provides his insight and knowledge on Building Regulations with Homebuilding & Renovating.