Retrofit Underfloor Heating: The Ultimate Guide
Is retrofit underfloor heating a good choice for a renovation project? Energy-efficiency expert Tim Pullen looks at the pros and cons of this popular option
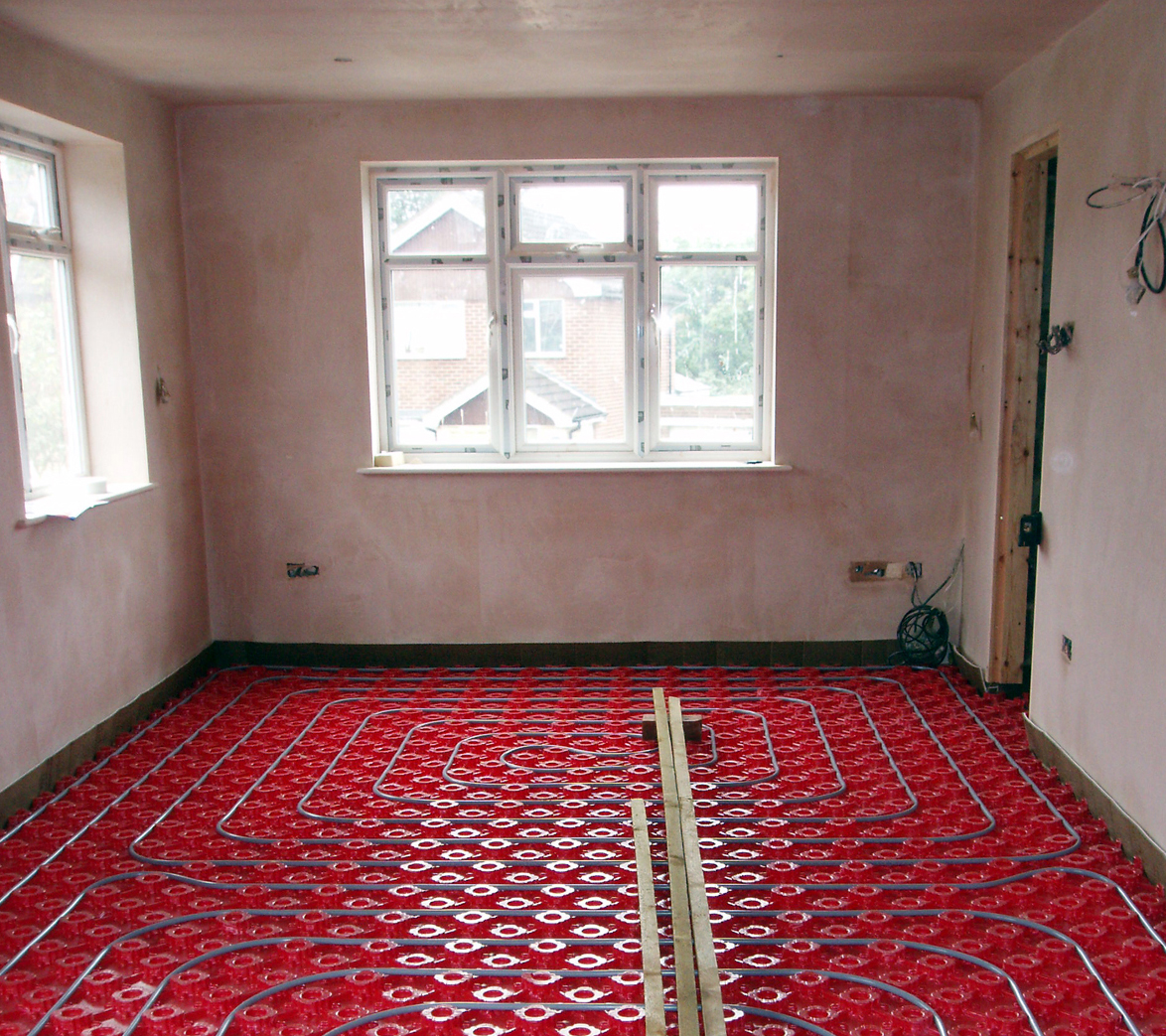
Retrofit underfloor heating can be a good choice for a renovation project but it may not be a simple matter. Underfloor heating (UFH) has become almost the de facto standard for self build projects. Putting it into a new build is simple, effective, relatively cheap and adds a touch of luxury.
Renovating a house does not offer the same blank canvas and there will always be issues and problems to overcome and complications could push the price up. It can be difficult for a renovation to achieve the same level of energy efficiency as a new build and that could cast doubt over the effectiveness of UFH.
But UFH is a choice. There are few situations that dictate that it cannot be installed and fewer that dictate that it must be installed. The only issue that genuinely prevents UFH being installed is cost.
Is Retrofit Underfloor Heating Right for Your Project?
The holistic view of renovation starts with what best suits the house. What the people living in it want obviously counts, but if it feels like a system is being shoe-horned in, then it probably should not be done.
It is a matter of considering the four key issues: the heat source, the hot water cylinder (if present), the existing floor and the level of insulation and airtightness achievable for the house as a whole. Ask yourself these questions:
- If the boiler needs to be replaced, is a heat pump an option?
- Is there budget available for a thermal store?
- Can the existing floor be retained or must it be removed and reinstated?
- Can insulation and airtightness be brought to, at least, current Building Regulations standard?
If all these stars align then retrofit underfloor heating is an option. (If not then choosing radiators may be a better bet for your project.)
Low Profile Underfloor Heating
Conventional underfloor heating systems can be over 125mm thick and that can mean removing and reinstating the floor to maintain a reasonable floor-to-ceiling height. Low profile systems can be as little as 20 or 30mm which usually overcomes the problem but there are, albeit rare, occasions when even that has an impact.
That is not to say that it should be installed. Almost invariably it will be more expensive to install than in a new build, as there will be preparation work and that will have a cost – floor coverings need lifting, skirting boards and doors removing and – a big one, this – floors need excavating.
Another issue is thermal efficiency. UFH operates just a few degrees above the desired room temperature and is therefore best suited to well-insulated properties. Poorly insulated or draughty properties need more heat and therefore a larger UFH system. That not only increases installation cost but also running costs, potentially to the point where radiators would be a better option from a financial standpoint.
It is fair to say that the bigger the renovation project the more likely it is that retrofit underfloor heating will be suitable. If the ‘renovation’ planned is little more than redecoration it is probable that the disruption, installation and running costs would make UFH a poor choice.
Is it Best to Retrofit Electric Underfloor Heating?
Wet and electric underfloor heating systems are distinctly different systems with different applications.
Electric underfloor heating is cheaper and easier to install than wet systems, and much thinner, so there is a role for electric UFH in small, difficult-to-access rooms.
But it is relatively expensive to run. A kilowatt of heat needs a kilowatt of electricity, and electricity is close to three times the price of gas (twice the price of heating oil).
The efficiency of heat pumps mean that they usually cost less than a gas boiler to run. As such, it would make no sense to install electric UFH throughout the house. If that is the only UFH option then radiators would be the better choice.
Choosing a Heat Source That Will Run With Underfloor Heating
Wet UFH will run with any heat source: gas or oil boiler, air or ground source heat pump. Heat pumps work most efficiently when delivering low temperature water and so UFH and heat pumps are well paired.
With retrofit underfloor heating, you may find need to upgrade your boiler or switch to a heat pump to make the most of the installation.
How to Retrofit Underfloor Heating on an Existing Floor
Lifting floorboards to install UFH is expensive but allows opportunity to introduce insulation, which ultimately means lower running costs
Often the big issue for UFH in renovation projects is how to cope with the existing floor. Should you put the UFH on top of the floor, or under it? Or should you rip everything out and start again?
This last option is expensive but allows space for insulation and for the finished floor level to be where it is wanted. If floorboards can be removed then it is entirely possible to suspend UFH between the joists and retain the existing floor level, as would be done for a first floor.
Concrete floors are trickier to deal with, and if the UFH has to go on top there are systems like NuHeat LoPro that will raise the floor level by as little as 20mm.
Screeds and Backing Boards for Retrofitting Underfloor Heating
The point of UFH is that the floor essentially becomes the radiator. Therefore there needs to be something that spreads the heat from the pipes evenly across the whole floor.
The conventional solution to this problem is a sand and cement floor screed, typically 75mm thick. It needs to be that thick to prevent cracking, but consequently it is expensive, it takes weeks to properly cure and it gives a reaction time (that is, the time taken to warm the room) of up to four hours.
It can be argued that every UFH system would be better with a liquid flow screed. These can be as little as 25mm thick (although 30mm to 45mm is more usual), can be walked on 24 hours after laying, have better thermal conductivity and a reaction time as low as 30 minutes.
If the UFH is going on top of a timber subfloor, then there is also a weight issue to consider. In such cases it may be better to use a backing board.
Insulated backing boards, pre-grooved to accept UFH pipes, are readily available and are often used in conjunction with an aluminium spreader plate, which is heated by the pipes so that it can in turn distribute the warmth across the whole floor.
There is some discussion about exactly how efficient aluminium is as a heat diffuser, but the technology has become common and convenient, so for now it’s the best option, especially as it allows the floor finish to be laid directly on top of the original timber floor while applying only a minimal load.
How to Insulate Retrofit Underfloor Heating
In a new build we would be required to install 75mm of rigid foam insulation (Kingspan, Celotex or similar) to meet the Building Regulations’ requirement to achieve a U value in the floor of 0.22W/m2K. In a renovation the regulations are more relaxed, if they apply at all, and less insulation is permissible.
A point to consider is that the ground under the floor will typically be 10°C to 12°C all year round. The lower internal/external temperature difference means that less heat will be lost through the floor than through the walls or roof.
If we assume a 30m2 room, walls and windows to Building Regs standard but an uninsulated floor, the annual heating energy consumption will be around 4,350kWh for that room, at a cost of £235 per year (assuming a gas boiler). If we insulate the floor to Building Regs standard, energy consumption falls to 1,890kWh, and we have a running cost of £102 per year. However, that means installing 75mm of insulation and that may not be possible or practical.
Installing just 25mm of insulation would mean energy consumption rising to 2,160kWh with an annual running cost of around £116 — just £14 more than full Building Regs standard. Obviously, that increase needs to be multiplied by each room on the ground floor but the difference, in running cost terms, between ideal insulation and minimum insulation is not huge.
There are UFH systems that use no insulation at all. These often grind a groove in the existing concrete floor to accept the pipes, allowing the floor finish to go straight on top and not raising the floor height at all.
The reasoning is that only 10% of the heat in the house escapes through the floor so insulation is not really necessary. However, that is 10% of the heat in an uninsulated house.
If the walls, loft, windows and doors are all properly insulated then the proportion of heat escaping through an uninsulated floor will increase to over 50%. As can be seen from the figures above, some insulation is a lot better than no insulation.
Bring your dream home to life with expert advice, how to guides and design inspiration. Sign up for our newsletter and get two free tickets to a Homebuilding & Renovating Show near you.
Tim is an expert in sustainable building methods and energy efficiency in residential homes and writes on the subject for magazines and national newspapers. He is the author of The Sustainable Building Bible, Simply Sustainable Homes and Anaerobic Digestion - Making Biogas - Making Energy: The Earthscan Expert Guide.
His interest in renewable energy and sustainability was first inspired by visits to the Royal Festival Hall heat pump and the Edmonton heat-from-waste projects. In 1979
this initial burst of enthusiasm lead to him trying (and failing) to build a biogas digester to convert pig manure into fuel, at a Kent oast-house, his first conversion project.
Moving in 2002 to a small-holding in South Wales, providing as it did access to a wider range of natural resources, fanned his enthusiasm for sustainability. He went on to install renewable technology at the property, including biomass boiler and wind turbine.
He formally ran energy efficiency consultancy WeatherWorks and was a speaker and expert at the Homebuilding & Renovating Shows across the country.