A guide to prefab extensions — a quick and often easy way to add space to a home
Considering a prefab extension? This is a great way to add space and value, and can often be carried out in three weeks or less
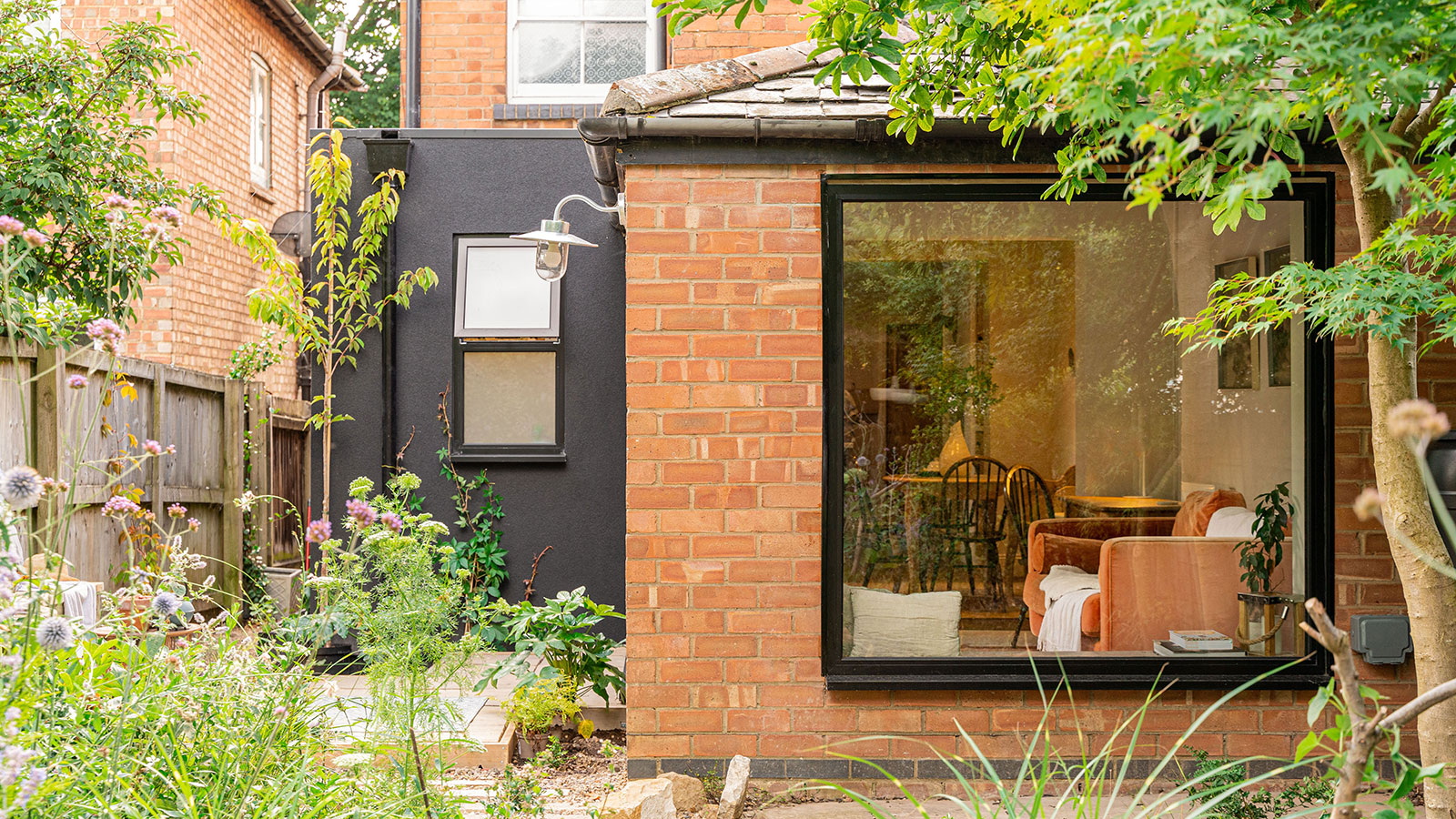
Prefabricated extensions these days are a long way from the prefab structures that were often seen in the past. Not only are they affordable, quick to construct and available in all kinds of designs, they are also built to last – making them a great option for all kinds of homeowners building an extension.
If you want to avoid the mess and disruption that usually accompanies brick and block extensions, it really is well worth considering a prefab design instead, as not only is most of the construction work done off-site, but they can be put into place much quicker.
Here, we explain everything you need to know about building a prefab extension so that you can decide whether it will be the right choice for you.
What are prefab extensions?
There are several different types of prefab extension – from those that are suitable for homeowners after rear extension design ideas to people after simple lean-to structures. That said, they all have certain things in common.
"Prefab extensions are a type of extension that is pre-fabricated off-site and delivered ready for installation," explains Sean Bunyan, head of commercial operations at Eurocell. "This means that much less time is spent on site and the construction process is often much quicker as a result."
"Essentially, a prefab extension is a structure that’s mostly built in a factory, then delivered to your property for quick assembly," adds Myles Robinson, CEO and specialist at UK Composite Doors. "It’s a much faster, more streamlined alternative to a traditional extension."
"As they are manufactured off-site in ‘kit form’, prefab extensions are usually constructed by a build team that will oversee the entire construction, including the roof, windows and doors." says Sean Bunyan.
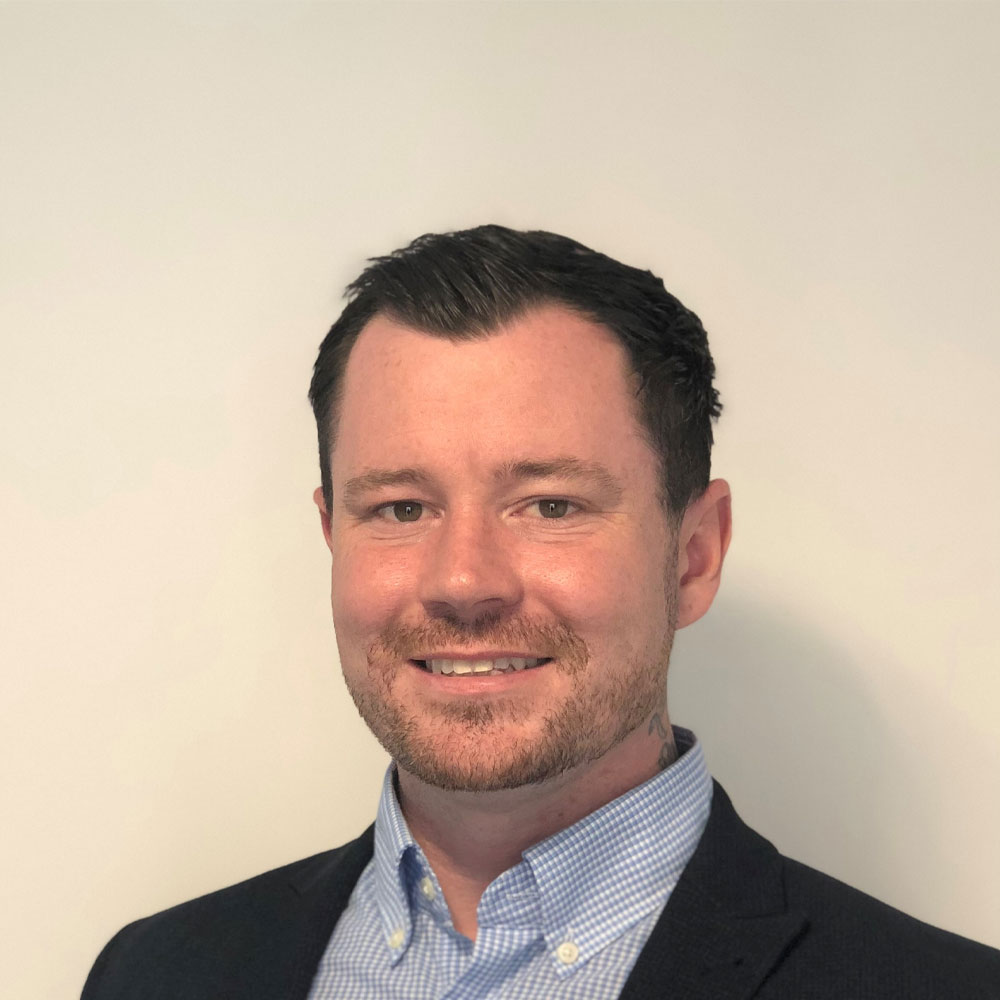
Sean Bunyan is head of commercial operations and a garden room specialist at Eurocell.
What different types of prefab extension are there?
While the term prefab extension is broadly used to describe any kind of structure that is made off-site before being delivered to be attached to an existing house, the way in which they are constructed can differ.
Construction options include timber frame, SIPs, light gauge steel framing or heavy steel. The way in which they are delivered to site will differ too. Some arrive fully-formed, ready to be craned into position, while others are only partially constructed off-site and finished off on arrival.
"Options vary from smaller build components that are manufactured in factories, delivered ‘flat packed’ and constructed on-site, to fully finished extensions that arrive completely assembled and are craned into place," confirms Sean Bunyan. "Whatever type of installation method you choose, structurally insulated panels, or SIPs, are often considered the industry-leading and most efficient method for prefab extensions."
"SIPs are a popular choice because they’re strong, lightweight and energy-efficient, perfect for the UK’s varying climate," picks up Myles Robinson. "These panels are made of insulation sandwiched between two layers of board, which keeps the structure solid and well-insulated. There are also modular builds, where entire sections are preassembled and simply connected on-site, and timber frame options that are ideal for those who want a more eco-friendly build.
"While SIPs are great for energy efficiency, timber frames give a classic look with a lower environmental footprint," continues Myles. "Each type has different advantages, so it comes down to what suits your home best."
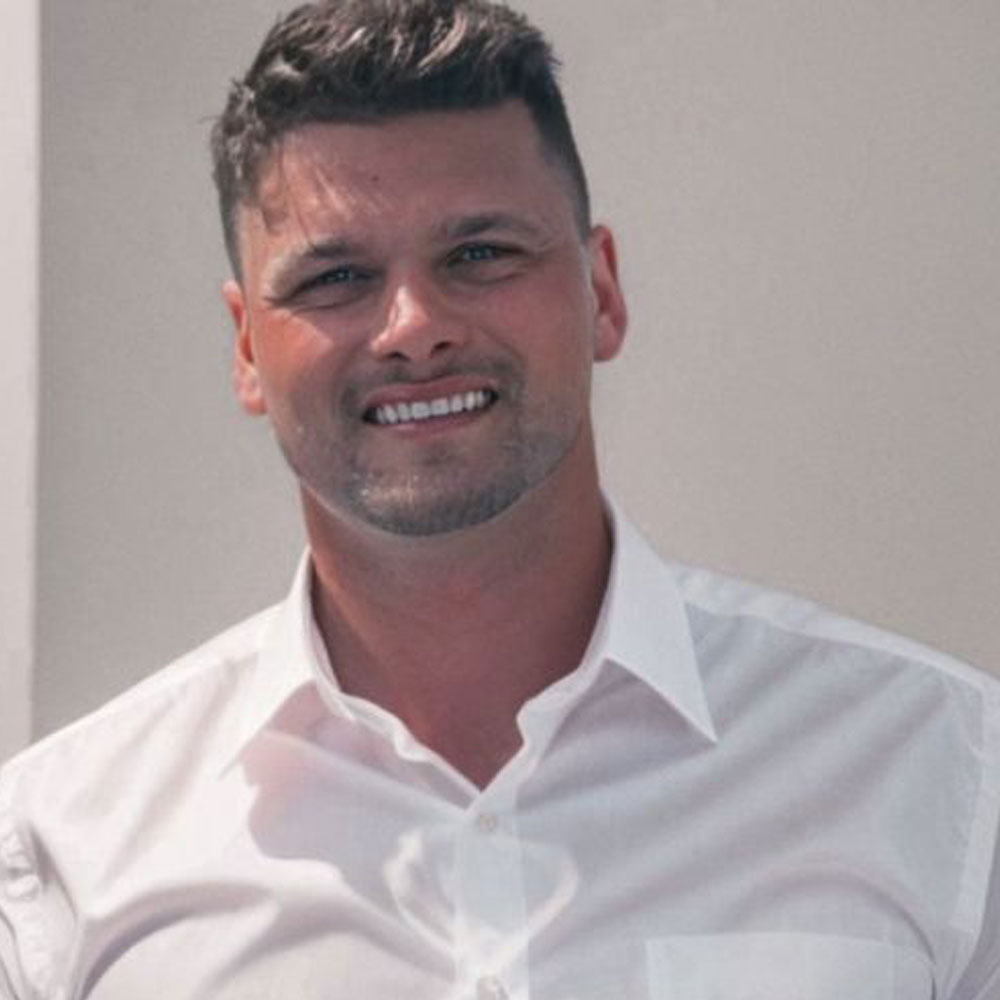
Myles is CEO and specialist at UK Composite Doors, a company that makes it possible to order, buy and have doors installed all online. He also offers a wealth of knowledge on prefab structures.
Who designs a prefab extension?
The most common route to having a prefab extension designed and constructed is to use a specialist company who offer a complete service.
"Eurocell’s prefab extensions are designed on industry-leading software by experts who consider the complete performance of the build," explains Sean Bunyan. "Designing a bespoke extension is complex, and considerations for structural details, compliance and insulation, all while maintaining an attractive design must be taken into account."
In some cases, for example with two storey extension ideas, homeowners choose to consult with an architect for the design of their extension.
"If you want something very unique, with an unusual form, then you would be better off having the extension designed by an architect with a bespoke build," advises architect Graham Ford, of Graham Ford Architects.
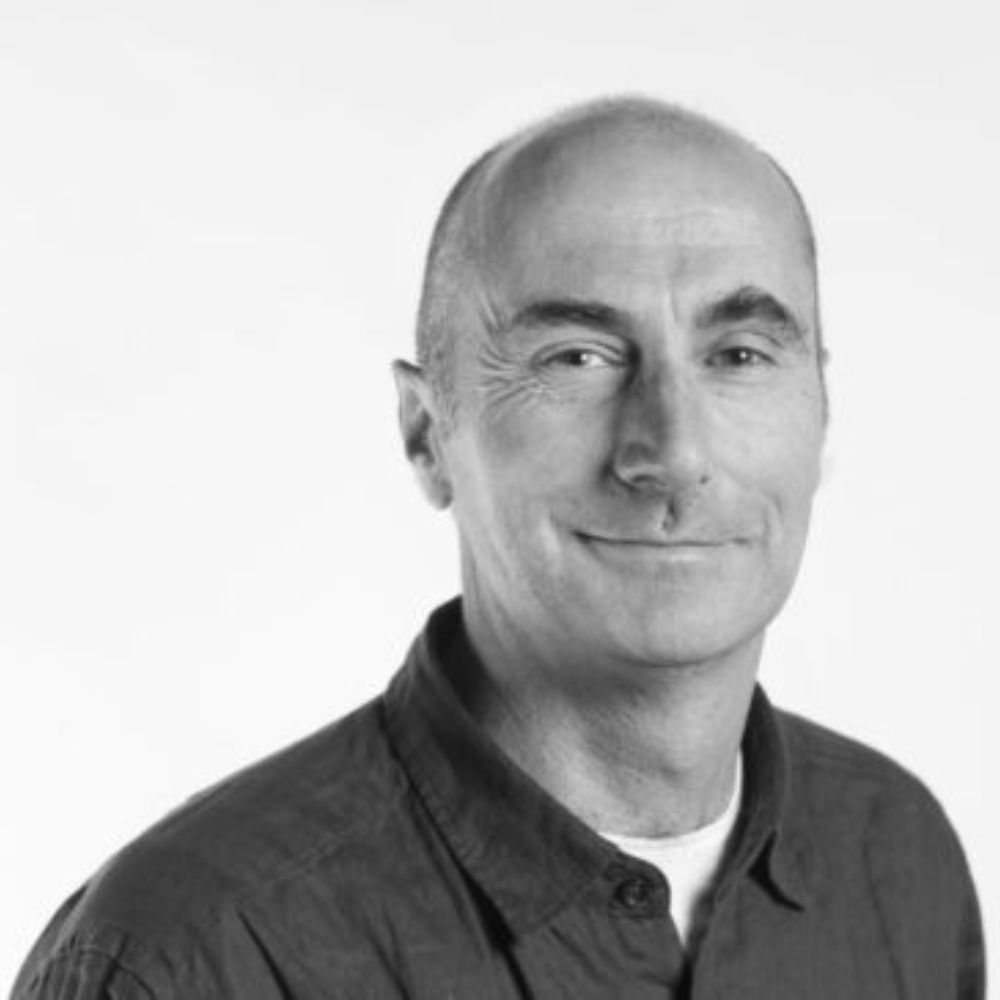
Graham is the founder of Graham Ford Architects and has over 22 years experience working on residential, academic, sustainable and commercial projects including the London 2012 Olymplic Games. He's the author of "The Total Environment Masterplan" and has lectured at the Universtity of Manchester, Reading and Portsmouth.
What is included in a prefab extension?
Any kind of extension costs can soon spiral so when you start getting quotes in for your prefab extension, it is really important that you double check exactly what those quotes include.
"Most prefab extensions come with windows and doors pre-installed, interior walls, and even basic finishes in some cases," explains Myles Robinson. "They’re designed to sit on a prepared foundation, usually a concrete base or specific footings suited to your site. Foundations are an essential part, and it’s worth chatting with your provider about what’s required. Some prefab packages also offer internal finishes like plastering or flooring, so there’s less left to do once it’s in place."
"Generally, prefab extensions are bespoke to the needs of the customer," adds Sean Bunyan. "They can be designed to complement or contrast, with brick slips, render or cladding finishes, choices in window and door styles and colours, as well as options of pitched roofs with rooflights or flat roofs with lanterns.
"Internally, the finish will depend on the customer's requirements," continues Sean. "Before all this though, it’s important to consider the foundations, electrical and plumbing routes."
How are prefab extensions delivered?
One of the main considerations homeowners opting for a prefab extension need to bear in mind is access when it comes to getting the structure onto site. Some prefab extensions arrive fully-constructed and are designed to be craned into place. However, in the case of modular extensions, they tend to come in sections, much like modular loft conversions.
"The extension components will be delivered to the site, often on the back of a lorry," explains Sean Bunyan. "Due to their modular nature, sections are designed to be modular enough for transport but sturdy enough to make the journey.
"Before being loaded onto transport, they are packaged into kits which the installation team use to put the pieces together."
How long does it take to build a prefab extension?
One of the most attractive aspects of prefab extensions is the speedy build times they offer.
"Once design work has been completed and signed off by the customer, building the pieces of prefab extension usually takes between two to three weeks," says Sean Bunyan. "During this time, the site can be prepared for the installation. Once the extension is in place and watertight, it’s time for those interior touches and decorations."
"It’s a fraction of the time you’d spend on a traditional extension, which can drag on for months," adds Myles Robinson.
What are the benefits of a prefab extension?
Just what advantages can homeowners expect if they opt for a prefab extension over a more traditional route or an oak frame extension?
"One of the biggest draws for UK homeowners is the speed, since most of the construction happens off-site, once the prefab extension arrives, it’s often ready in a week or less," says Myles Robinson. "This reduces disruption and, since you’re spending less time on-site, it can be more cost-effective, too.
"Prefabs are also highly energy-efficient, with insulation built into the panels and designs to ensure airtightness, so they perform well in our colder months," adds Myles.
"The main advantage for customers is that the timeframe from start to finish is controlled and substantially quicker," picks up Sean Bunyan. "Pricing is also more controlled than a traditional build, which can move in cost through the project. With a prefab extension, you’re much less likely to run into issues during the build which can delay a project or increase its budget.
"Taking the EurXtension system from Eurocell as an example, the construction itself is seven times stronger than timber frame and three times stronger than brick and block," continues Sean. "With a combination of high-performance SIP panels and A-rated double or triple-glazed windows and doors, it delivers excellent thermal efficiency and can help to save money on energy bills too."
What are the disadvantages of prefab extensions?
Just as with everything, from flat roof extensions to fully-glazed structures, there are also a few disadvantages to be aware of when considering a prefab extension.
"Design flexibility can sometimes be limited to standard layouts or styles, so if you’re after something very bespoke, prefab might not tick all the boxes," points out Myles Robinson. "Site access is another thing to think about, since these structures are pre-built or arrive in large sections, you’ll need clear access for delivery, which isn’t always easy if you’re in a tight urban area or on a small plot."
"Fortunately, there are relatively few challenges associated with prefab extensions," says Sean Bunyan. "The only real ones to consider are whether or not it’s possible to get site access to where the extension will be constructed, and creating a design that fits harmoniously with the existing structure."
"You want to avoid having to use a crane to lift parts of your extension over your house to the rear of your site," adds Graham Ford.
How are prefab extensions attached to a house?
Unlike extensions that are constructed on-site, where they are built off the existing building, how are prefab extensions connected to a house?
"This depends on the scenario," begins Sean Bunyan. "Any base work will be tied into the existing foundations, just like a traditional extension would be, through a range of foundation options, but the walls and roofs are bolted into the property. All of this means the extension is as weather-resistant and watertight as any brick and block construction."
"Once on-site prefab extensions are securely attached to your home’s main structure, weatherproof seals are added to protect against moisture," adds Myles Robinson. "They're usually designed to look seamless, blending in with your home’s style."
Early on in the design stage your architect or chosen specialist will take precise measurements to make sure that the new structure will fit the existing house perfectly. In cases where the modular addition is being made from a material that is different to that used for the original building, movement gaps will be incorporated to account for the fact that the two materials are likely to expand and contract differently. A stainless steel channel tie system is usually used for this.
How much do prefab extensions cost?
While there is no set price for a prefab extension, it is possible to give an idea of costs which tend to be in line with standard extension costs but less than glass extension costs.
"Generally, prefab extensions in the UK can range from around £1,500 to £2,500/m2, although prices vary depending on your chosen materials, finishes and any customisations," says Myles Robinson. "While they’re usually cheaper than traditional builds, do budget for any additional groundwork or custom features."
Graham Ford, whose practice is based in London, estimates this type of extension to cost a little more, however.
"It varies considerably depending on the finishes and company you choose, where you live and access," he begins. "However, as a rough budget figure, allow between £3,000 and £4,500 per m2."
"It’s difficult to say how much a prefab extension costs, as there are lots of factors to consider," explains Sean Bunyan. "Every design is bespoke and there are numerous options to choose from. Of course, one of the main advantages here is that once your design is locked in, it’s unlikely you’ll see any spiralling build costs afterwards."
FAQs
How long will a prefab extension last?
There was a time when some people believed that prefab extensions were more of a temporary solution – but that is no longer the case.
"The extension should be just as durable and last just as long as a traditional option," reassures Graham Ford. "Like all construction, this depends on the quality of the construction and installation."
"With correct maintenance, prefabricated extensions can have a lifespan of up to 50 years," adds Sean Bunyan.
Are prefab extensions well insulated?
One of the main benefits of prefab extensions is that the way in which they are usually constructed makes them inherently energy efficient, meaning that adding one could actually help when insulating your house.
"Prefab extensions are often built with high insulation values in mind, thanks to SIPs or other energy-efficient materials," explains Myles Robinson. "Joints are sealed, and any windows and doors are typically double- or triple-glazed, which makes them airtight and energy-efficient. This reduces drafts and keeps the space warm – especially handy in winter."
Interested in finding ways to add space without adding to the footprint of your house? Loft conversions can add lots of useful space and often won't require planning permission.
Bring your dream home to life with expert advice, how to guides and design inspiration. Sign up for our newsletter and get two free tickets to a Homebuilding & Renovating Show near you.
Natasha was Homebuilding & Renovating’s Associate Content Editor and was a member of the Homebuilding team for over two decades. In her role on Homebuilding & Renovating she imparted her knowledge on a wide range of renovation topics, from window condensation to renovating bathrooms, to removing walls and adding an extension. She continues to write for Homebuilding on these topics, and more. An experienced journalist and renovation expert, she also writes for a number of other homes titles, including Homes & Gardens and Ideal Homes. Over the years Natasha has renovated and carried out a side extension to a Victorian terrace. She is currently living in the rural Edwardian cottage she renovated and extended on a largely DIY basis, living on site for the duration of the project.