Insulating concrete floors: Why and how to do it — plus retrofit options
Insulating concrete floors to the required standard will help cut your energy bills as well as make your home feel more comfortable overall — but how is it done? We asked the experts
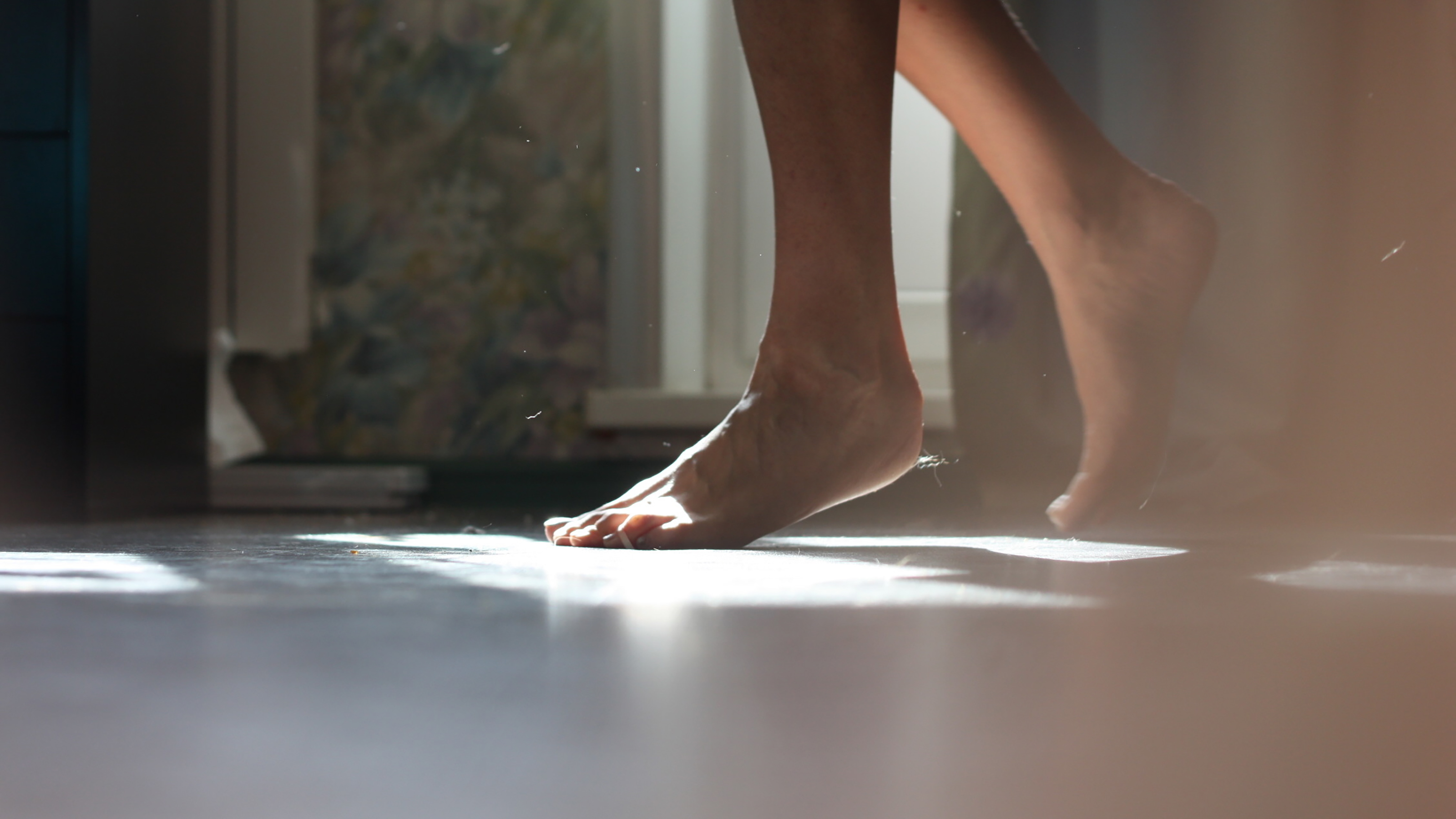
While the job of insulating concrete floors tends to be a little more involved than when insulating suspended timber floors, it is most certainly a job well worth doing. And choosing the right insulation and knowing the best way of installing it is key to an energy efficient home, helping to cut bills and warm up a chilly house.
“Concrete ground floors became commonplace in the 1950s, many being installed without an effective damp proof membrane,” explains Rob Bohm, Heating and Energy Consultant at CLPM Construction Consultancy. “As the building regulations changed, effective dampproof membranes were fitted, but only since the 1990s have building regulations required that new ground floors be insulated in order to conserve energy.”
Of course what all this means is that if you are renovating a house built before these new regulations were introduced and have solid concrete floors within your property, they are very unlikely to be insulated.
Here, we take a look at the methods used to insulate both new and existing concrete floors and how much this job is likely to cost.
Why is insulating concrete floors important?
Before you start looking at how to insulate your house, it is always important to understand what benefits you can expect in order to justify the costs that inevitably ensue.
“Insulating a building is important to reduce overall energy usage,” explains Rob Bohm. “Around 15% of heat loss from a building can be through the floor. Houses with concrete floors built prior to 1990 would certainly benefit from having insulation fitted.”
Concrete can be very cold underfoot, so not only will adding insulation to your solid floor reduce the amount of heat lost, but it will also save you from having to endure freezing cold toes as temperatures fall.
Energy Saving Trust estimates that, based on fuel prices as of October 2022, by insulating the floor of an average detached house, homeowners could save £180 per year.
How much floor insulation do I need?
"All new solid floor installations need to meet the building regulations and standards," says Jonathan Ducker, Head of Regulatory Affairs at Kingspan Insulation GB. "These differ depending on whether your property is located in England, Scotland or Wales. In England, they’re contained in Approved Document L1 2021 of the Building Regulations, in Wales they are within Approved Document L1 2022 to the Building Regulations (which come into force on 23rd November 2022) and in Scotland they’re contained in Technical Handbook Section 6 (Energy) 2022 to the Building Standards (which come into force from 1st February 2022).
"In each case, these documents set target insulation (thermal performance) levels that you should look to achieve depending on the work you’re carrying out. The U-value you need to achieve will depend on where your property is located, and whether you are retaining the existing floor slab (and installing the insulation above it) or digging it out entirely. If these are not achievable, the Approved Documents and Technical Handbooks set out some specific scenarios where you can target a worse U-value."
According to Energy Saving Trust, to meet building regulations when installing a new floor, in England or Wales, the floor should achieve a U-value of 0.25 W/m2K or less, if possible, and in order to achieve this standard, you will normally need at least 70mm of high-performance foam insulation, although this will vary depending on floor type, shape and size.
If you are insulating floors in a renovation project, they go on to say: “if you are replacing more than half of a floor then you have to insulate to these standards whether you planned to or not.”
"A good way to find the thickness of insulation you need is by using a U-value calculator such as: www.u-valuecalculator.com/gb," says Jonathan Ducker.
How are new concrete floors insulated?
Fitting floor insulation tends to be far more straightforward when starting from scratch in a new build or extension. In this case, it is preferable to fit insulation below the concrete slab, where it helps the concrete absorb heat.
During the construction process, a damp proof membrane will be laid over a layer of sand, before insulation is placed on top, and finally the concrete is poured. If you are fitting a wet underfloor heating system, it will now be laid on top of the concrete sub floor with a thin screed layer poured over the top.
"For solid concrete floors, make sure that if they need to be replaced, your builder puts in insulation — you have to insulate a floor when it is replaced in order to comply with building regulations," say Energy Saving Trust. "Solid floors are insulated using rigid insulation foam, which can be fitted either above or below the concrete. If the concrete is above the insulation it can sometimes store heat during the day, which helps keep the room warm at night. If the insulation is below the concrete the room will heat up more quickly in the morning."
How do I insulate an existing concrete floor?
So how about existing concrete floors? Adding insulation beneath, as is commonly the case with a new concrete floor, can be costly and disruptive, but there are alternatives.
Although adding insulation on top of the floor is the most common method used when renovating old floors, in some cases renovators will find it necessary to dig out a solid floor completely, perhaps where damp may have become an issue, or where a new floor level is required to blend in with an extension.
"There are three common options for insulating an existing solid floor," says Jonathan Ducker. "Remove the original floor slab and dig down to provide additional space for the insulation; strip the layer of screed above the floor slab and install highly efficient rigid insulation boards with a liquid screed; or install vacuum insulation panels (VIPs) above the existing floor screed with a liquid screed."
But as Rob Bohm points out, digging up the floor is not always ideal.
“Unfortunately digging up the floor can be very expensive and will be very disruptive indeed,” Mr Bohm explains. "Concrete also hardens with age, so old concrete can be very hard.
“I would recommend that if a floor is to be replaced and insulated, that a test hole is cut initially so that an assessment can be made which will result in a more accurate cost estimate. It would actually be rare for a house built post 1990 to have the concrete floor replaced as the cost involved will most likely outweigh the value of the energy reduction.”
The alternative to a test hole is to contact a retrofit coordinator to have your property assessed, says Jonathan Ducker.
"This includes a risk assessment of the property to assess potential issues which may prevent the installation of floor insulation such as shallow foundations, external ground conditions and external drainage. They will then develop an improvement plan for your property," Mr Ducker explains.
What other alternatives are there to avoid disruption?
"You can still insulate your solid floor even if it doesn’t need replacing," say the Energy Saving Trust. "Rigid insulation can be laid on top of the original floor, then chipboard flooring can be placed over it. This will raise the level of the floor, so you will need to make sure doors are trimmed shorter to make room for the insulation. Skirting boards and some electrical sockets may need to be moved too."
“It is possible to add a thin layer of high-performance insulation on top of an existing floor, although this will raise the floor height, which could cause an issue with door and head heights and threshold heights,” says Rob. “There is, unfortunately no simple answer, and investigation is likely to be required to determine the best solution.”
"Installing insulation on top of the floor can present problems with ceiling, door and window cill heights,” agrees Tim Pullen, expert in sustainable building methods and energy efficiency in residential homes. "You could try a product such as Kingspan’s range of Vacuum Insulated Panels (VIPs) which offer a solution for those needing an ultra-thin build-up. They feature a microporous core, which is evacuated and sealed in a thin, gas-tight membrane, achieving a performance similar to the thickness of traditional insulation but at levels of just 26mm.”
If you feel you can accommodate the extra height that laying insulation over an existing concrete floor will bring with it, experts recommend first laying a DPC. The insulation board will be laid on top of this, before a moisture-resistant chipboard, or a concrete screed, is installed above. This can then be covered by the final type of flooring.
“Insulating an existing concrete floor is difficult,” explains Tim Pullen, who has oone more solution. “I generally suggest painting on a coat of insulating paint, with a thin insulation board on top. Something like Prowarm XPS Board or similar.
“Used together they do a reasonable job of reducing the U-value and this solution is way cheaper than digging the floor up yet it still makes the floor feel warmer.”
Are there any tips when installing a concrete floor?
Once you have decided on the right route for you, how can you ensure the disruption is minimised and that the work and expense is worth it?
"Whichever approach you take, it is important to properly prepare the surface before fitting the insulation," says Kingspan's Jonathan Ducker. "Start by removing any existing flooring to reveal the ground slab, confirming it is level, clean and in good condition. As part of this process, you should carefully check the slab and perimeter walls for signs of moisture or damp.
"Concrete is a fairly porous material which can easily suffer from rising damp if the damp proof membrane (DPM) has failed or was never installed. In cases where the slab has been incorrectly laid above the level of the damp proof course in the walls, it can also act as a bridge — potentially leading to rising damp in the walls," he continues.
"It is worth noting that in humid environments such as kitchens, it is sometimes possible for condensation to become trapped under vinyl flooring, giving the impression of rising damp. This can be rectified by improving home ventilation within the space with an extraction fan.
"Even in cases where you are planning to re-lay the slab, if any signs of damp are identified, it is a good idea to get a retrofit specialist to assess the issue and to determine the cause and solution. For example, in cases where the damp proof membrane beneath the slab is damaged, it may be possible to address the issue by fitting a membrane above the slab (in cases where the slab is being retained).
"As with all insulation retrofits, it is also important to consider the existing ventilation levels within the space, how the new insulation layer may affect this and consequently whether additional ventilation is needed. This can be supported through air-leakage testing."
How much does it cost to insulate a concrete floor?
As with so many things in the world of self build and renovation, giving exact costs for this job is tricky.
"The cost of this job could vary by quite a margin and will depend on the floor area, the thickness of the concrete, and how hard it is, which can depend on the mix used at the time," says Rob Bohm.
"A typical suspended floor installation could cost you between £1,600 and £2,900 depending on the circumstances," say Energy Saving Trust. "Solid floor insulation could cost considerably more." It is wise to budget between £60-70/m2, plus the cost of labour.
If you were to take the insulating paint route, you could make significant savings. "Costs for this job would be around £10/m2 for both paint and board and this task is easily doable by a DIYer," says Tim Pullen.
Get the Homebuilding & Renovating Newsletter
Bring your dream home to life with expert advice, how to guides and design inspiration. Sign up for our newsletter and get two free tickets to a Homebuilding & Renovating Show near you.
Natasha was Homebuilding & Renovating’s Associate Content Editor and was a member of the Homebuilding team for over two decades. In her role on Homebuilding & Renovating she imparted her knowledge on a wide range of renovation topics, from window condensation to renovating bathrooms, to removing walls and adding an extension. She continues to write for Homebuilding on these topics, and more. An experienced journalist and renovation expert, she also writes for a number of other homes titles, including Homes & Gardens and Ideal Homes. Over the years Natasha has renovated and carried out a side extension to a Victorian terrace. She is currently living in the rural Edwardian cottage she renovated and extended on a largely DIY basis, living on site for the duration of the project.