How to Insulate a Loft
If you would like to turn your loft into habitable space, it must be insulated to current Building Regulations. Here we explain how to insulate a loft
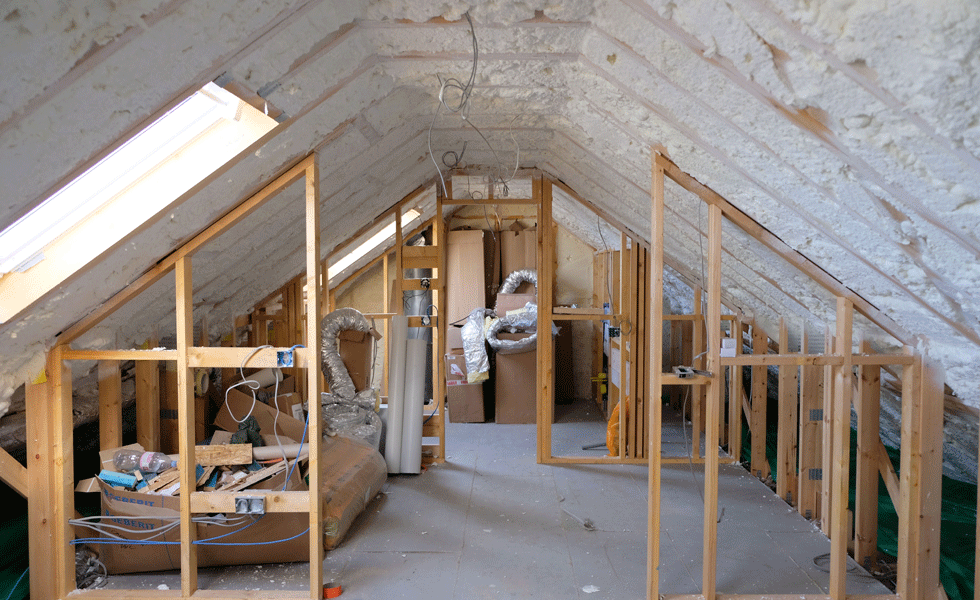
Creating extra storage or a new habitable space by insulating a loft and transforming it into something more usable is a smart way to ease pressures on the rest of your home. But first, you will need to ensure you’re insulating in line with guidance laid out in the Building Regulations, taking material and fire-resistance into account.
Here, in our beginner’s guide on how to insulate a loft, you’ll find expert advice on which type of insulation would work best, where to put it and a practical step-by-step guide on how to fit roof insulation.
Where Should I Fit the Insulation When Insulating my Loft?
There are actually three levels where you can fit the insulation, and the choice will depend on what the loft will be used for, but a combination of two could be needed to meet requirements. If the loft is going to be used as living space, then the insulation should be placed at rafter level to create a warm roof.
But if you plan to use your loft for storage only, then a conventional cold roof option (where the mineral wool insulation rolls are placed in-between the ceiling joists above the top floor).
If insulation is placed exclusively between the rafters, they will have to be very deep to ensure you can fit the required depth of insulation (the very best phenolic foam insulation will have to be 125mm deep to meet Building Regs requirements). With this installation method, there is a danger of minor condensation caused by cold bridges at the position of the rafters. This moisture could lead to discolouration of the internal decoration.
Fitting a continuous layer of insulation over the rafters will solve the issue of cold bridging, but is only an option on new builds or renovations where the roof tiles are being stripped and relaid. Even then, the depth of insulation now required to meet the Regulations means that very large fascia boards and wide soffits are required.
This loft insulation method also solves the issue of cold bridging, but can restrict headroom. This problem can usually be designed out in a new build, but may cause an issue when an existing roof is to be converted.
When insulating a loft, the most practical solution is to place most of the insulation between the rafters, with a smaller additional layer fixed to the underside of the rafters. Insulated plasterboard is useful for this purpose. Plasterboard is available with a wide variety of rigid insulation products bonded to it.
For applications where the roof is not being completely stripped, a combination of between- and under-rafter insulation with a 50mm ventilated airspace between the upper surface of the between-rafter insulation and the traditional sarking felt is best.
What Material is Best for Loft Insulation?
There a numerous options when choosing the material with which to insulate a loft and they all differ from one another. Firstly, materials have three different types of stiffness: they can be rigid (e.g. polystyrene boards), semi-rigid (e.g. mineral wood boards), and soft (such as the familiar rolls of loft quilt that can be stuffed into voids between rafters). There are also loose-fill materials like cellulose and polystyrene beads that can be blown-in.
If space is at a premium, there are a number of plastic foam, polyurethane-type materials that are gas based. The best known are Celotex and Kingspan. While they tend to be expensive, these are considerably better than air-based insulants such as mineral wool.
This is denser than the expanded version and is widely specified under floors and where there is contact with the ground. Suppliers include Dow Styrofoam and Knauf Polyfoam.
The wool-type insulations (often sold in rolls) are the cheapest. The polyurethanes and polystyrenes are usually sold as boards: these can be used in any application, but are particularly good under floors. Boards are often fitted in sloping roofs but this requires a lot of cutting. Walls can be insulated with boards or slabs, a semi-rigid format which stiffens wool-based insulation.
Insulating the floor can be achieved by a mineral fibre quilt laid between the joists. Use the heavier, denser sound insulation quilt.
For many houses, it is often necessary to insulate party walls — both against heat loss and noise. Introducing timber studwork with mineral fibre insulation will allow you to achieve both and it can be covered with sound-rated plasterboard.
Multifoils use thin rolls of aluminium foil alternated with layers of foam padding. They promise good insulation levels, way better than expected by their 25mm width. They are a popular way of insulating sloping roofs.
The use of natural insulation materials is becoming popular. Sheep’s wool is a wonderful material to use in place of the synthetic wools (that are made of glass fibre and mineral wool which are cheap but not pleasant to work with). Look out for Thermafleece. We are also beginning to see wood fibres and hemp being used in both roll and slab format, useful for insulating timber walls and roof spaces. Look for products such as Homatherm and Thermo-Hemp.
Insulation doesn’t have to be dry fixed. Wool, fibres and plastics can all be blown into position via a nozzle. This is a widely used technique under roofs. Warmcel is a popular form of insulation, used mainly in timber frame houses and lofts. It is comprised of cellulose fibre, made from recycled newspaper.
How do you Fix Insulation Between Loft Rafters: How To Guide
By Ben Fields
Partially-filled rafters:
- To maintain the required void above the insulation and to ensure the boards are flush with the bottom of the rafters, sidenail battens to the rafters in the appropriate position to provide a stop
- The void must be 50mm deep and ventilated for constructions not using a breathable sarking membrane. Ventilation should be provided in accordance with Approved Document F, F2 (Condensation in Roofs) of the Building Regulations or Technical Standard K (Ventilation of Buildings, Regulation 23) of the Building Standards (Scotland)
- Measure the space between the rafters before cutting the boards, as spacings will vary slightly
- Cut the insulation boards to size using a sharp knife or fin-toothed saw. We used Kingspan Thermapitch TP10 zero ODP which is a 100mm-thick rigid board
- Install the insulation flush with the bottom of the rafters, making sure that it does not fill the entire rafter depth. Ensure that the insulation boards fit tightly between the rafters
- Fill any gaps with expanding urethane sealant
Fully-filled rafters:
- Measure the space between the rafters before cutting the boards, as spacings vary
- Cut the insulation boards to size using a sharp knife or fine-toothed saw
- Install the insulation so that it is flush with the bottom of the rafters but does not fill the rafter depth
- In all cases, ensure that insulation boards between rafters are fitted tightly
- Fill any gaps with expanding urethane sealant
- Measure up before cutting the boards
- Cut the insulation boards to size using a sharp knife or fine-toothed saw.We used Kingspan Thermawall TW56 zero ODP
- Where board dimensions allow, fix the boards at right angles to the underside of the rafters
- Boards should be fixed with galvanised clout nails or drywall timber screws, long enough to allow 25mm penetration of the timber. These should be placed at 150mm centres and not less than 10mm from the edges of the board along all supporting edges
Remember
- Ensure accurate trimming to achieve close butting joints and continuity of insulation
- Ensure the continuity of the insulation at the ridge
- To prevent a cold bridge, tightly pack flexible insulation material between the rafters and the cavity closer
Get the Homebuilding & Renovating Newsletter
Bring your dream home to life with expert advice, how to guides and design inspiration. Sign up for our newsletter and get two free tickets to a Homebuilding & Renovating Show near you.
Tim is an expert in sustainable building methods and energy efficiency in residential homes and writes on the subject for magazines and national newspapers. He is the author of The Sustainable Building Bible, Simply Sustainable Homes and Anaerobic Digestion - Making Biogas - Making Energy: The Earthscan Expert Guide.
His interest in renewable energy and sustainability was first inspired by visits to the Royal Festival Hall heat pump and the Edmonton heat-from-waste projects. In 1979
this initial burst of enthusiasm lead to him trying (and failing) to build a biogas digester to convert pig manure into fuel, at a Kent oast-house, his first conversion project.
Moving in 2002 to a small-holding in South Wales, providing as it did access to a wider range of natural resources, fanned his enthusiasm for sustainability. He went on to install renewable technology at the property, including biomass boiler and wind turbine.
He formally ran energy efficiency consultancy WeatherWorks and was a speaker and expert at the Homebuilding & Renovating Shows across the country.