How to finish a self build to a perfect and professional standard
Our self build expert explains everything you need to know about the finishing stage, installing fixtures and fittings, floor finishes and decorating
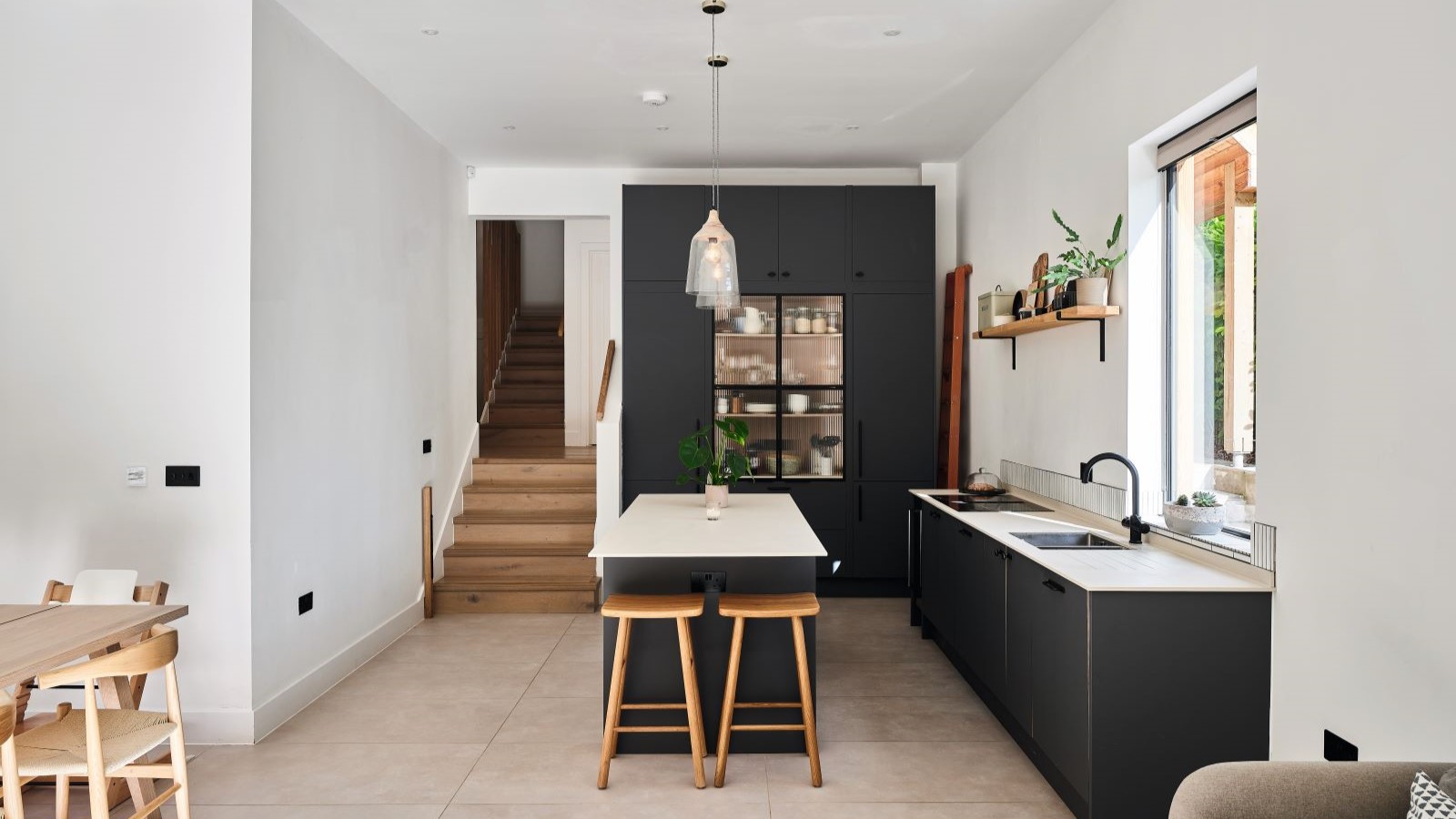
- Decorating your finished self build
- How to achieve a good-quality standard
- Make sure paints are fit for purpose
- Adding your fixtures and fittings
- Installing the perfect kitchen
- Adding your staircase to your build
- Getting a professional finish for your flooring
- Applying sealants
- Don't forget the protection
Building a house is a monumental task and the finishing stages are where it finally starts to feel like a home.
The finishing includes the decorations and flooring as well as the fitting out of expensive fixtures and fittings such as kitchens and staircases. But to get these things right, it is all about paying attention to the detail – not just the positioning, but also in the installation too.
Here, self build expert, Mark Stevenson talks about how to do this to give you the perfect home to enjoy after all the hard work is complete.
Decorating your finished self build
The interior decoration of a home personalises the spaces we live in and, depending on your choices, can cost a small fortune. The options are endless, from bespoke wallpaper to modern cladding ideas as well as simple painted surfaces, which are easier to live with, in my opinion.
As we all have distinctive design aspirations and different budgets, what’s involved will vary from self build to self build, but from a builder’s point of view, in the first instance and until the shrinkage has stopped, it’s best to keep things simple.
As a rule of thumb, complex painting techniques and expensive wallpaper is best avoided for at least a couple of years as this will prove impossible to repair when the inevitable cracks in walls appear. The most popular choices are emulsioned plaster surfaces, which are low cost and easy to repair. Don’t let this stifle your creative aspirations, though. With a carefully chosen colour scheme, achieving the look you are after is still possible.
How to achieve a good-quality standard
Lots of self builders decide to take on the decorating themselves either because they’re able or have run into budget pressures. Others opt to work with professional designers and contractors.
Whichever of these approaches you decide to take, before cracking out the paintbrushes and rollers, the build must be made ready for painting to begin. To achieve any kind of quality standard, the plaster should be dry and dust free and everything that’s going to receive a coat of paint must be fitted and finished.
This sounds obvious, but it’s common to find that in the rush to make a personal statement, self builders make decorating mistakes, such as starting painting too early, resulting in a poor-quality finish. Before starting to paint, it’s best to carry out a room-by-room pre-paint snag.
The purpose of the pre-paint snag is to check that everything’s ready and identify any remedial work that might be needed. Ideally, the joinery work should be finished, and any gaps made good or professionally filled with filler or caulk.
The electrical and plumbing fittings should also be installed so you know there’s no risk of damage caused by leaks, or fishing for cables. If the trades have done their jobs well, there should be little to find other than minor surface defects, which are easily made good with fine surface filler and a good deal of sanding.
The key to achieving a high-quality standard is good preparation and correctly following the application process advised by the manufacturer. If you’re using a painting contractor, they’ll have the necessary expertise, but if you’re decorating yourself take time to read the back of the paint tins and understand the prep work needed, as well as the drying times between coats.
Before popping the paint lids, a big thorough clean-up is needed to remove all the dust and debris that might contaminate the paint and ruin the finish of the final decorations. It’s also a good idea to give the decorators the run of the house, so plan for the other trades to be finished and out of the way.
Make sure paints are fit for purpose
It’s essential that the paint being used is suitable for the job and will prove durable in use. There’s lots to consider here, but for me the key is to ensure the paint will stick and last as long as possible before needing to be redone.
When painting new plaster for example, new plaster should be ‘sized’ (sealed) and is best painted with specialist emulsion designed for the purpose. In high-humidity rooms such as bathrooms and kitchens, it’s best to use vinyl paints with mould inhibitors, which will be more durable.
In high-traffic areas, opt for paints that provide resistance to scuffing or that can be easily cleaned when marked. When it comes to woodwork, gloss is the go-to solution, but these days, there’s lots of alternatives such as satinwood or eggshell, which will not discolour with age.
For those in the trade, the type and specification of paint is very important, and most contractors would prefer to use professional paints, which are more expensive but offer better performance. When choosing paint, it’s a good idea to ask for advice by visiting a specialist decorating centre that supplies specialist materials and offers free advice.
Tools and paint you need to add a mist coat
A water-based emulsion ideal for mixing as a mist coat and as a top coat
Adding your fixtures and fittings
Kitchens and staircases are a key design feature of modern self builds, and you only have to look at some of the fantastic projects featured in Homebuilding & Renovating to realise that they’re a design statement costing tens of thousands to buy and install. As with anything worth a small fortune, installation is best left as late as possible to avoid irreparable damage.
In a perfect world, the house should be completely decorated before fitting those expensive fixtures and fittings, the theory being that you don’t want cupboards used as ladders or paint splashes down your expensive pre-finished furniture. In reality, installing a staircase or fitting a kitchen will cause damage to finishings so it’s best to get the majority of the decoration done, leaving just a final coat where making good will be needed.
Kitchens and staircases are technical installations and must be designed and installed to comply with Building Regulations. As a manufactured item, provided the design is right, the components will be supplied in kit form to suit your home and in full compliance with regulations. The architect, being the principal designer, should check the design for compliance, so before signing off the design for manufacture, make sure this has been done.
Installing the perfect kitchen
In one sense, kitchens are easy to install in new builds as they’re designed to perfectly fit the space, and walls and floors are presumably plumb and level, which should make installation easy.
Unfortunately, kitchen installations involve a variety of trades, from carpenters to plumbers and electricians, as well as specialist worktop installers.
All of which means lots of coordination is involved, so it’s worth double checking who will be doing what to make sure nothing is forgotten. To make your life a little easier, kitchen companies can take on the whole package but remember, convenience costs money, so be prepared to pay a premium for this service.
Adding your staircase to your build
These days, staircases are expensive pieces of furniture and to avoid damaging them, you don’t want trades dragging materials over them, so leave the installation as late as possible.
Staircases design must comply with Building Regulations, which have strict limitations on tread dimensions, handrail and head heights and flight pitch. Make sure these are all achieved by carrying out a site survey.
Don’t forget to allow for floor finishes and remember to double check the proposed design proposals before allowing manufacture to proceed. Handrails are a key part of the staircase and extend across flights and landings to prevent falls from height.
While they’re commonly made from timber to match the staircase, glass and metal are popular options. These involve additional trades so will require greater coordination, with multiple site visits to take templates and fit the finished product.
Getting a professional finish for your flooring
When it comes to floor finishes, much of the same advice applies, and achieving a good-quality standard requires thorough preparation and proper selection and use of materials. Hard flooring needs to be fitted below skirtings to hide cut edges.
What’s left are soft floor coverings such as vinyl and carpet, which are installed after decorations to prevent damage. A common complaint with flooring is squeaks, and anyone that’s had them knows there’s nothing worse.
At this stage it’s worthwhile carrying out a thorough check to make sure there’s nothing untoward that will either create an unwanted noise, or a lump or bump once the final flooring is fitted. If you find something, get it fixed, as this will be your last chance.
Applying sealants
One of the last jobs on a self build is the sealing of gaps in bathrooms and kitchens, as well as around flooring and windows. Applying silicone sealant is a skilled job, but with the correct tools, like this Amazon Basics 3-IN-1 Caulk Tool for Removal and Application, some soapy water, and loads of paper towels, most DIYers can do a good job.
If you don’t fancy having a go, get the professionals in, but be careful to make sure they don’t seal up everything in sight, as they charge by the metre.
Don't forget the protection
At this stage of the build, the house is gradually filling up with expensive pre-finished items which are all at risk of damage, so make sure there’s loads of protection available to cover areas that are prone to damage.
Hardboard and Correx sheeting, which can easily be bought on Amazon, may be inexpensive, but surplus cardboard from unwanted packaging is free – and much more sustainable.
Once you have finally finished your self build, it's still important to carry out your snagging or extension snagging checks. You may need to wait a few weeks for everything to settle, but this is an important task that mustn't be forgotten to ensure you have the perfect finish to your home, as well as avoiding potential costs further down the line.
Get the Homebuilding & Renovating Newsletter
Bring your dream home to life with expert advice, how to guides and design inspiration. Sign up for our newsletter and get two free tickets to a Homebuilding & Renovating Show near you.
Mark Stevenson has worked as a construction professional for over 30 years and following an extensive career in housebuilding. He is currently chief operating officer for Custom Build Homes and chair of the National Custom and Self Build Association. He previously worked as managing director for Potton, helping self builders build their own homes.
Whilst Mark describes himself as a ‘professional builder’ as a result of his career in housebuilding and timber building system manufacturing, he has specialist knowledge of timber construction and extensive expertise in finding land and project management.
He regularly shares his knowledge at Homebuilding & Renovating Shows and and coaches self builders about how to build their own homes. Aside from Mark’s professional career, his skills also extend to practical building knowledge as a skilled joiner, hands-on renovator and serial self-builder of his own development projects.
He is also Vice Chair of industry body, the Structural Timber Association.