I'm a builder and this is how to avoid paying too much for materials
If you’re a novice renovator or first-time self-builder, how can you be confident you’re being offered the best price for materials? Our expert builder, Andy Stevens, offers his advice.
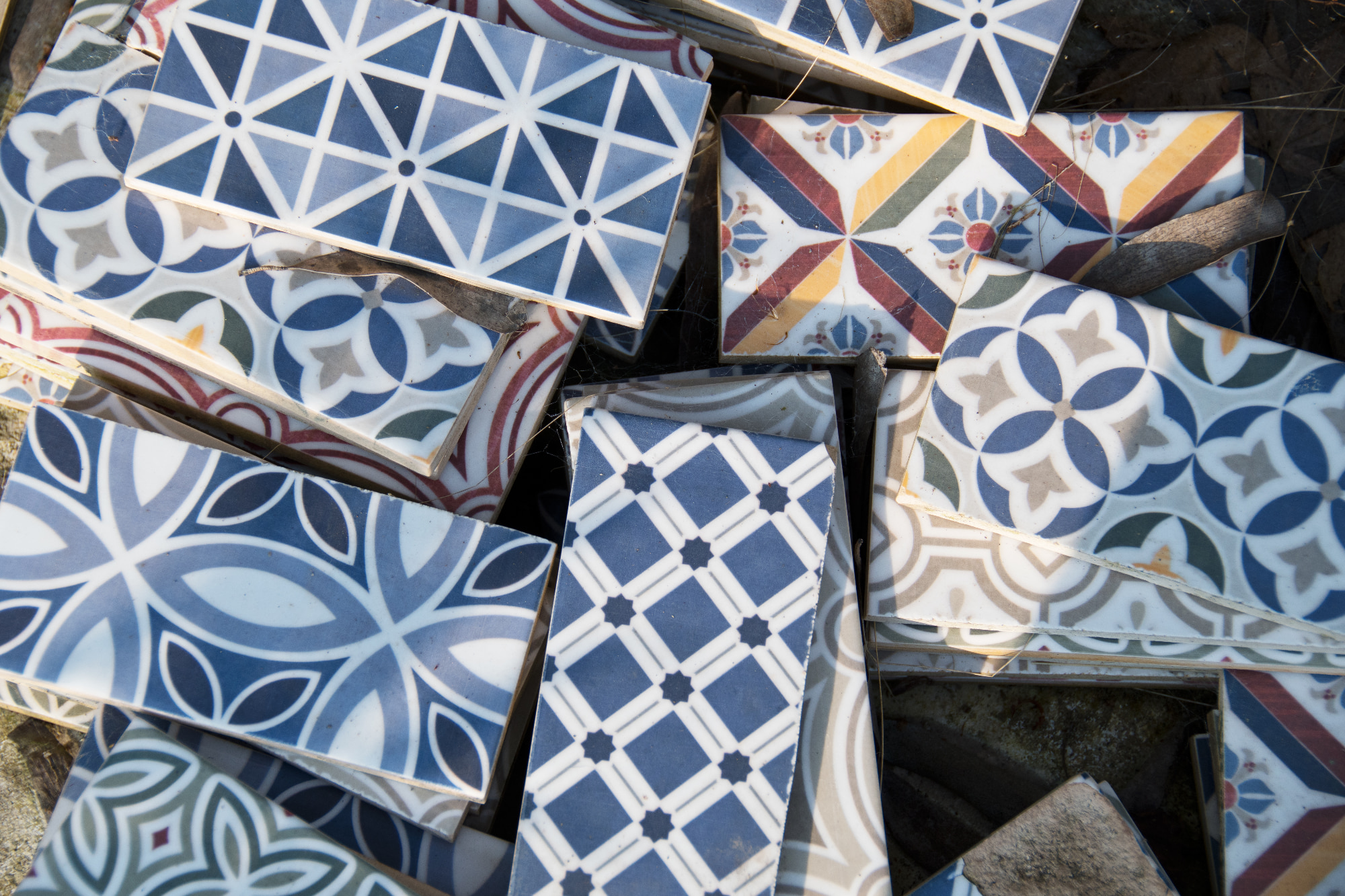
I've been in the building industry for years, and as someone who's navigated the ups and downs of home renovations and self-building, I know how daunting it can feel, especially for beginners.
Understanding how to negotiate prices and where to invest your money can make a huge difference to your build, and with recent material cost increases, getting the best deal is more important than ever.
From decoding industry jargon to developing negotiation skills, this article aims to equip you with the knowledge you need to ensure you aren’t paying over the odds for your materials and building supplies.
What do I mean by 'terms?'
Before Covid, keeping on top of the price of materials was relatively straightforward. Come November, I would sit down with my rep from the suppliers I used, and we would look at my spend and then break it down into sections. I would tell them my predicted spend in each area and we would have a ‘discussion’ over the increases they’d been given by manufacturers and eventually agree on what we call ‘terms’.
The word 'terms' can be a source of confusion and frustration in our industry. Let me break it down for you: 'Terms' used to be our reliable guide for budgeting material purchases, offering predictability and control.
But now, thanks to construction material shortages and a trades shortage, it's a whole different ball game. The price you actually pay for materials can vary based on several factors:
- Who's serving you at the merchant's counter.
- Whether the salesperson correctly applies the terms.
- If the salesperson puts your order under your current trade account, not a cash account you used years ago.
- If your suppliers have a specific offer on or ‘a manager’s special’.
- Your rep leaves and the new rep doesn’t keep your existing terms
All of these points need to be kept on top of. We’ve all been caught out but, now more than ever, it is poignant to manage this correctly.
How to keep the cost of your materials down
If you're relatively new to developing or renovating, use this to your advantage. Either work out your materials list yourself – what you need, quantities etc, or work with a quantity surveyor. Then, take this list to various merchants, both big names and local independents, and ask for their best prices.
Be upfront about shopping around; this transparency can work in your favour. Once you get their quotes, don't hesitate to go back and negotiate. Trust me, with a little effort, you can make significant savings and ensure your project stays within budget.
These are my top 3 tips for keeping the cost of materials down:
1. Specifying quantities
One point which is sometimes overlooked is knowing the right quantity of materials to order. This isn’t as simple as it sounds. Different materials have different calculations, so it's important to correctly measure for building materials.
For example, for tiles and flooring, you would normally order an extra 10-15% on top of what you need. This is to take into account cuts/wastage and some being damaged or unusable. If you order exactly the right amount and a box of tiles arrive broken, it will be your responsibility to get new ones to the trade that is fitting them ASAP. If this takes a while, the trade could ask you for money when they couldn’t work.
For aggregates like soft and sharp sand, ballast etc, over order as these will be coming in bulk bags or off a lorry. You don’t want brickies, landscapers, groundworkers, running out of something close to finishing off. These aren’t expensive items, so don’t be caught short.
Timber is another material which is difficult to order. You can work out a cutting list required for the build, but depending on where you source your timber, the longer lengths (3.6m, 4.2m, 4.8m etc) can often arrive bowed and warped, which makes them largely unusable. I would advise not going with the cheapest supplier as your chippy will want decent timber. If in doubt, ask your builder for advice.
If you do end up with an excess of materials, like offcuts, half a bag of soft sand, bits of plasterboard, they are pretty much worthless. Obviously unopened bags of cement, plaster, uncut timber can be returned, but check with your supplier if there is a restocking charge and if they will charge for picking it up.
2. Build relationships
As with Covid, some things are very difficult or impossible to predict, which can have an impact on the prices you pay. I’ve always said, keep in regular touch with your supplier as they are the ones that will hear first of any impending price rises.
Us trades are in and out of merchants all the time and have built up relationships with our account managers and all the staff, including yard staff, staff behind the counter and managers. In the same way you can get the best from your builder, developing a relationship with these people will go a long way. If they do you a favour, take them something in to say thanks. This doesn’t have to be much, but it will likely pay dividends.
3. Go for reclaimed
Reclaimed materials can help you keep your renovation costs down. But, as I’ve said in previous articles, make sure you research what you are buying properly. Some materials you simply cannot reuse – sand, cement, plaster, tile adhesive – but there are quite a few you can.
The cost of new timber these days is high, so you can save a lot of money by opting for reclaimed wood floors. Older timber is also far better and stronger than the timber we have produced these days. A lot of the new timber is fast grown and a softer, soft wood. Old roof timbers, floor joists and stud walls are also excellent examples of things you can reuse. One thing to bear in mind is the sizing – older timbers are imperial so they will be 4x2 inches whereas newer ones are slightly smaller, so it is difficult to use them together.
Reclaimed bricks are another material you can reuse but the key thing with these is making sure they are the same and have been cleaned, as you don’t want to be paying someone to clear all the old mortar off them. If they won’t be seen, such as coming out of the ground on footings, or a retaining wall in the garden that’s going to be painted/rendered, then it doesn’t matter as much.
Second hand kitchens can be reused and sprayed any colour, maybe just changing the handles for a more modern look. You can even reuse doors if you have a decent carpenter.
Establishing good relationships with your builder and suppliers is key to getting the best prices and hearing of any impending price rises. Get these relationships right, and you could save a lot of money!
Get the Homebuilding & Renovating Newsletter
Bring your dream home to life with expert advice, how to guides and design inspiration. Sign up for our newsletter and get two free tickets to a Homebuilding & Renovating Show near you.
Andy Stevens is a multiple award-winning builder who manages Surrey-based building company Eclipse Property Solutions; he specialises in new builds, extensions and loft conversions.
While he is still on the tools, he is also widely involved in the construction industry. He presents a show on Fix Radio and hosts his own building podcast Build:It, as well as being a speaker at the Homebuilding & Renovating Shows.
Andy has sat on the Board of the Federation of Master Builders (London region) and was previously Vice President. He also works with construction charities and is an advocate for mental health in the industry.
- Gabriella DysonInteriors journalist and contributing editor