Embodied carbon: Why new construction proposals could impact self builders
Architect Paul Testa explains the problem of embodied carbon within construction and why self builders should be aware of potential new limits
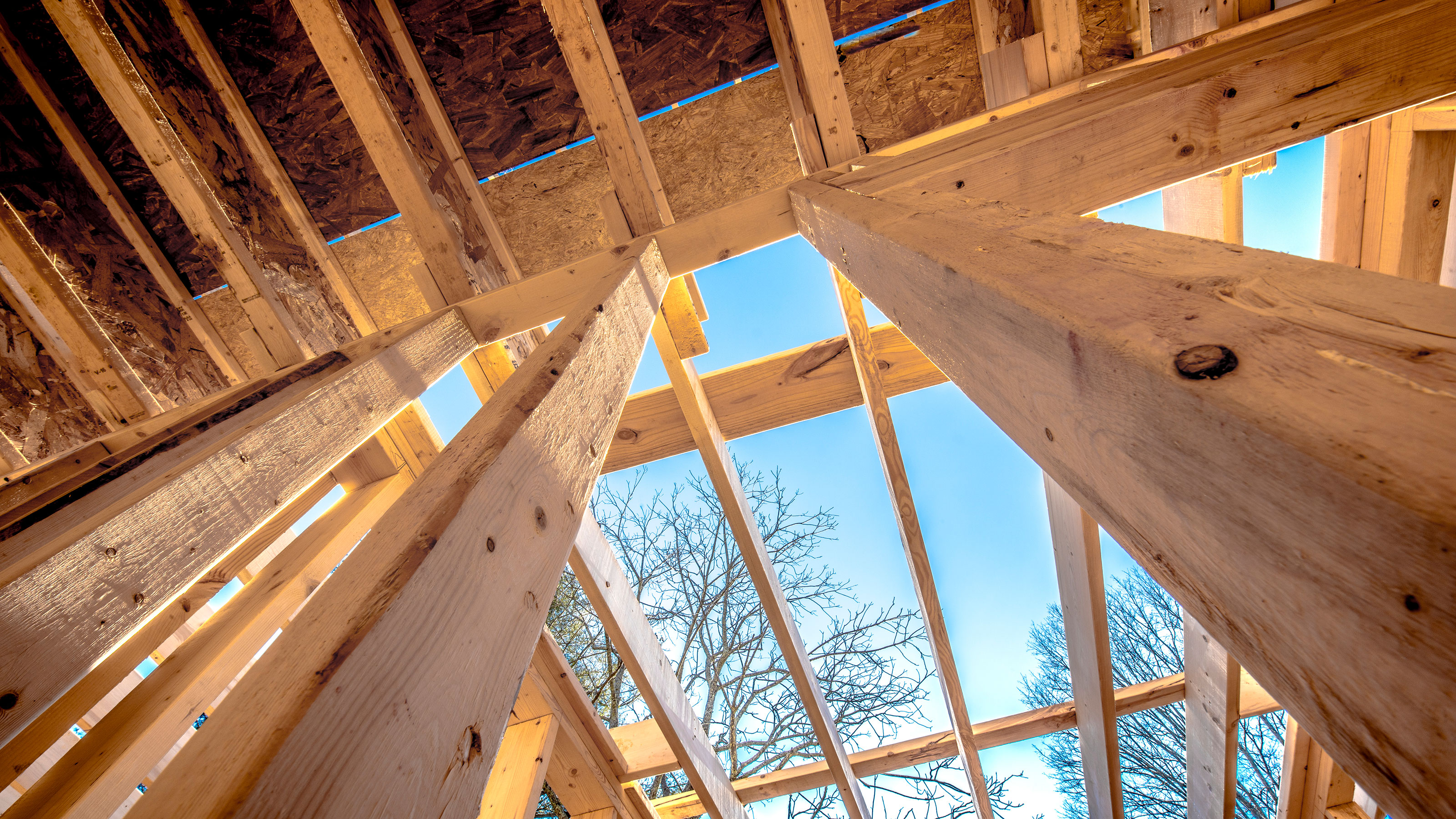
Embodied carbon is the amount of carbon emitted during a building’s construction.
The government and construction industry are under increasing pressure to lower these levels in new homes, with the net zero drive meaning cutting carbon emissions from building work is now a priority.
It isn't an easy task either. UK Green Building Council research from November 2021 showed that embodied carbon emissions from the construction, maintenance and demolition of buildings, creates 40-50 million tonnes of CO2 each year. This is more than shipping and aviation combined.
It's an issue that could become very pertinent to those building a house, especially with industry groups proposing new limits on embodied carbon for building projects. These could eventually become part of the Building Regulations.
Here’s everything you need about why embodied carbon is such a problem within the construction industry and how it could be regulated in the future.
What is embodied carbon within buildings?
Buildings emit carbon in all parts of their life: materials, construction, operation, demolition and removal. This is their whole life carbon emissions.
While operational carbon refers to the amount of carbon emitted once a building is in use, embodied carbon refers solely to its construction, generated through production, transport, use, and disposal of a material.
The construction industry has got its head round operational carbon and there's generally a good understanding of reducing operational energy demand and using lower carbon energy sources.
However, there is work to be done and those planning a self build may need to become aware of embodied carbon in the future. According to data from the United Nations Environment Programme, the manufacturing of building materials makes up 11% of global greenhouse gas emissions.
How is embodied carbon measured?
Most embodied carbon is expressed as "cradle to gate" - the emissions caused by extraction (the cradle), transport and processing of raw materials, and manufacturing of the product, up to the point it leaves the factory (the gate). Building materials, transport and construction activities are very carbon intensive. We also call these upfront carbon emissions.
Embodied carbon is usually expressed as kg CO2 per kg of material. This isn't the easiest format to get to grips with, as materials have very different densities and are used in significantly different quantities in a building.
The highest carbon intensity materials are steel and concrete (cement). Materials such as timber and other bio-based materials are typically much lower in carbon.
There has always been an argument that many high carbon materials are very durable, so they spread this carbon over a very long life, and while this is true, the immediate carbon impact is so critical right now, this needs to be a secondary consideration.
New proposals could regulate embodied carbon
There are no current legal limits for embodied carbon, but industry proposals are in place for a new Building Regulations document Part Z, which would provide mandatory assessments and reporting of whole life carbon.
Under the proposal, construction firms would need to assess and report on whole life carbon on all non-residential projects over 1,000m2 from 2023 and residential projects from 2025.
It is not totally clear what this would mean for self builders, but I would expect, when any limits are then set, that most self builders will be able to comfortably adapt their designs to achieve these limits without significant compromise.
It may make slightly more carbon-intensive construction approaches such as Insulated Concrete Formwork (ICF) more tricky, but there will still be lots of flexibility.
How can self builders lower their embodied carbon?
The best approach is to calculate the embodied carbon of your project and do what you can to minimise this. Not many consultants do this, and the data isn't always easy to obtain, but it is worth trying if you can.
You can take a simple best practice "rule of thumb" approach for designing buildings with low embodied carbon:
- Use as little of anything as is required to fulfil its role - this includes timber
- Reduce steel and concrete to the minimum you can
- Use bio-based materials where you can; timber, straw, wood fibre and clay are all low-carbon and easy to work with
- Try to use products that have dual (or more) functions to reduce the number of materials.
You could also consider reducing the complexity in your home's design (structural complexity, especially, tends to push concrete or steel solutions) and consider how big you really need to build.
Is carbon sequestration valuable?
When they're grown, bio-based materials absorb atmospheric carbon. This is called sequestration.
Designers often like to include the negative carbon balance of the carbon sequestered in their embodied carbon calculations as it can lead to projects being described as carbon negative. However, if you ask yourself if there's less carbon in the atmosphere because a material has been used in a building, the answer will always be "no".
Ultimately, at the end of the material's life, the carbon will be re-emitted into the atmosphere when the product is burnt or rots. So it's much better to take the figures where this isn't included.
Get the Homebuilding & Renovating Newsletter
Bring your dream home to life with expert advice, how to guides and design inspiration. Sign up for our newsletter and get two free tickets to a Homebuilding & Renovating Show near you.
Architect Paul is the director of HEM Architects and a specialist in low-energy design. HEM Architects are well-versed in designing sustainable, energy-efficient new builds and extension schemes. He has also just completed an eco retrofit to his family home.
He taught the technology course for the MArch in Architecture at Sheffield University, and is a tutor for the Sustainable Architectural Studies Masters course.