Comparing Wall System Costs
Trying to choose between timber frame, masonry and SIPs? Comparing the costs of different structural walling systems can be tricky — but it’s well worth delving into the figures and finding ways to balance costs with quality
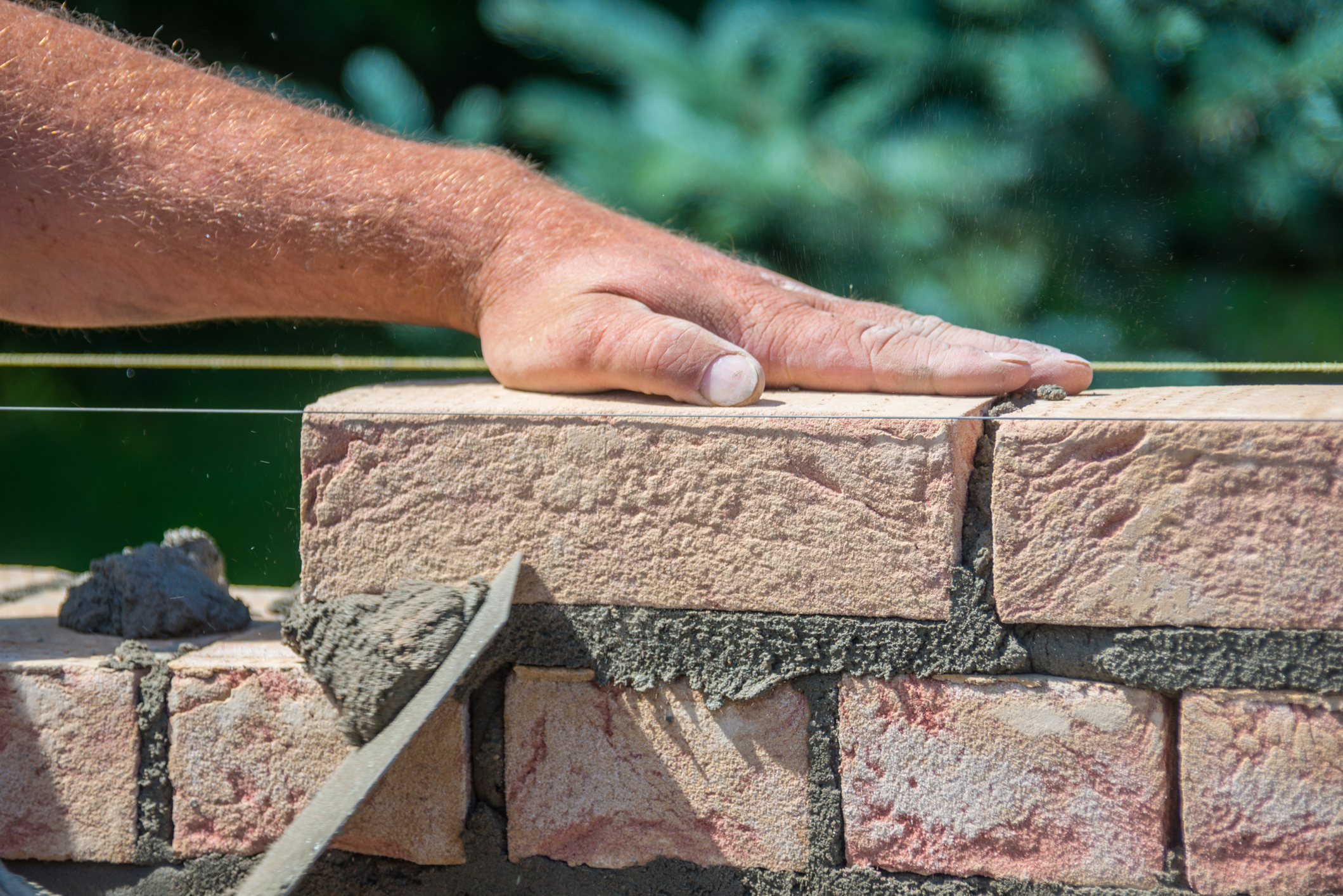
One of the major choices facing the self builder is deciding which structural walling system to use for their new home. In most cases, that will boil down to a choice between three construction methods that compete with each other for viability and effectiveness:
With the latter two options, brick, render, timber, etc, may be the cladding of choice.
Of course, many of the companies working within the self build sector, such as Potton, tend to favour one or two particular systems (in the latter case, timber frame and SIPs). In these cases, the method of building may become a secondary consideration for the self builder who has chosen to build with one of these companies.
Nevertheless, the choice is still an important one and with conflicting information, the first-time self builder may, at times, not know which way to turn.
The plain fact of the matter is that each one of these mainstream wall systems all offer different benefits (SIPs, for instance, offer a much faster build time and an airtight structure, while with masonry, both the materials and labour are readily available). Each one can and will achieve, at least, the minimum requirements of the Building Regulations and be capable of exceeding them in terms of structure, longevity, value and thermal efficiency, with nothing more required than a little tinkering.
So, the final decision may well come down to cost. And what are the costs relative to each other? What are the likely costs you can expect per m2 of walling?
Trying to compare the costs on a like-for-like basis is a bit like comparing a horse with a cow — they’ve both got four legs and are covered in fur, but that’s where the similarities end.
Trying to Compare Labour and Materials Costs
Let’s look at the costs for each method. The cost of blockwork (masonry) for the internal skin is easy to establish, although it must also include the cost of insulation to allow for any meaningful comparisons.
- So one m2 of blockwork equals 10 blocks at a cost of, say, £10*, although you could do better.
- To that, you have to add £12/m2 for the insulation in order to achieve the minimum U value.
- Then there are the extras such as mortar and wall ties, which add a further £1.60.
- And finally there is the labour, which will average around £12.50/m2 — all of these elements add up to £36.10/m2.
- You could amortise those costs over the whole area of the internal leaf of the cavity walling and be just about right with your answer, because any block, in any position in the home, performing any function within the structure, is going to basically cost the same.
If you try to do the same thing with timber frame or SIPs, you’ll come unstuck. And that’s because of the ‘horse and cow’ syndrome. The blockwork prices above don’t account for any openings or the lintels and cavity closers that each of those requires.
Meanwhile, when one receives a price for a timber frame construction, the price is based on the whole structure and typically includes the intermediate flooring, the internal partition walling and the roof structure, with all of it being made away from site in a factory and then brought to site for erection.
How Much Difference is There in Wall System Costs?
Of course, the costs of the factory, the design and the delivery are then amortised over the whole package. Sources within the industry have identified the elements within such a package that go to make up the structural walling and, for that same m2 of walling, they work out at around £72 for timber frame and £82 for SIPs respectively. But to try to work out your probable timber frame or SIPs package cost from those figures would be completely meaningless and a gross distortion of the actual costs and prices.
That is because a disproportionate amount of the overall design and manufacturing costs are reflected within the envelope. The known fact, reflected in HB&R’s Build Cost Calculator and supported by the case histories of readers’ experiences, is that there is little difference in the finished costs when measured over the usable floor areas of new homes.
If anything, brick and block is slightly cheaper per m2 — hardly enough to notice. But brick and block takes longer to build and there are many more uncertainties, not least with workmanship and the unpredictable British weather. Timber frame is in the middle and SIPs is slightly more expensive, but provides greater ability to control airtightness and quality.
SIPs panels consist of an insulating core bonded between two structural facings. Built off-site, the panels are very fast to erect on site and achieve good U values and excellent airtightness. While more expensive than timber frame, assessed across the whole project the additional costs are only around 3 to 5 per cent
Slightly more expensive than masonry and cheaper than SIPs, timber frame offers a swift on-site build (as the panels are manufactured off-site). Shown is an open panel system: insulation and joinery are fitted on site
The least expensive of the three structural wall options, brick and block is a building technique that every builder will be familiar with and has the added advantage that masonry materials are available from every builders’ merchant
Cost, then, is not a major factor and other elements such as aesthetics, build times, airtightness, availability of local skills and personal preference comes into play.
Why it Doesn’t Pay to Cut Costs
This is probably one area where it doesn’t pay to reduce costs by way of cheapening or lessening the wall structure. Nevertheless, there are always going to be differences in price between various companies working in the timber frame and SIPs fields for instance, and if you are not locked into a contract it pays you to shop around.
Those not needing a package deal or hand-holding service could opt to go to a timber frame or SIPs manufacturer for a supply and erect service only. With brick and block, it is simply a question of negotiating the best deals from suppliers and holding down the labour rate.
Get the Homebuilding & Renovating Newsletter
Bring your dream home to life with expert advice, how to guides and design inspiration. Sign up for our newsletter and get two free tickets to a Homebuilding & Renovating Show near you.
David is one of the UK's leading self build and plotfinding experts, and a serial self builder who has been building homes for 50 years. The author of Building Your Own Home, now in its 18th edition, and the Homes Plans Book, David spent decades as a speaker and expert at self build exhibitions such as the Homebuilding & Renovating Show. He also helped countless budding self builders find their dream building plots as part of his long-running Plotfinder Challenge series in Homebuilding & Renovating magazine. He has self built 14 homes.