Cavity wall insulation — the pros, cons, types and regulations
For a warm and energy efficient home, cavity wall insulation is a must. We take a look at the options available and offer advice on how to make sure you pick the right type to suit your project – and adhere to the current regulations
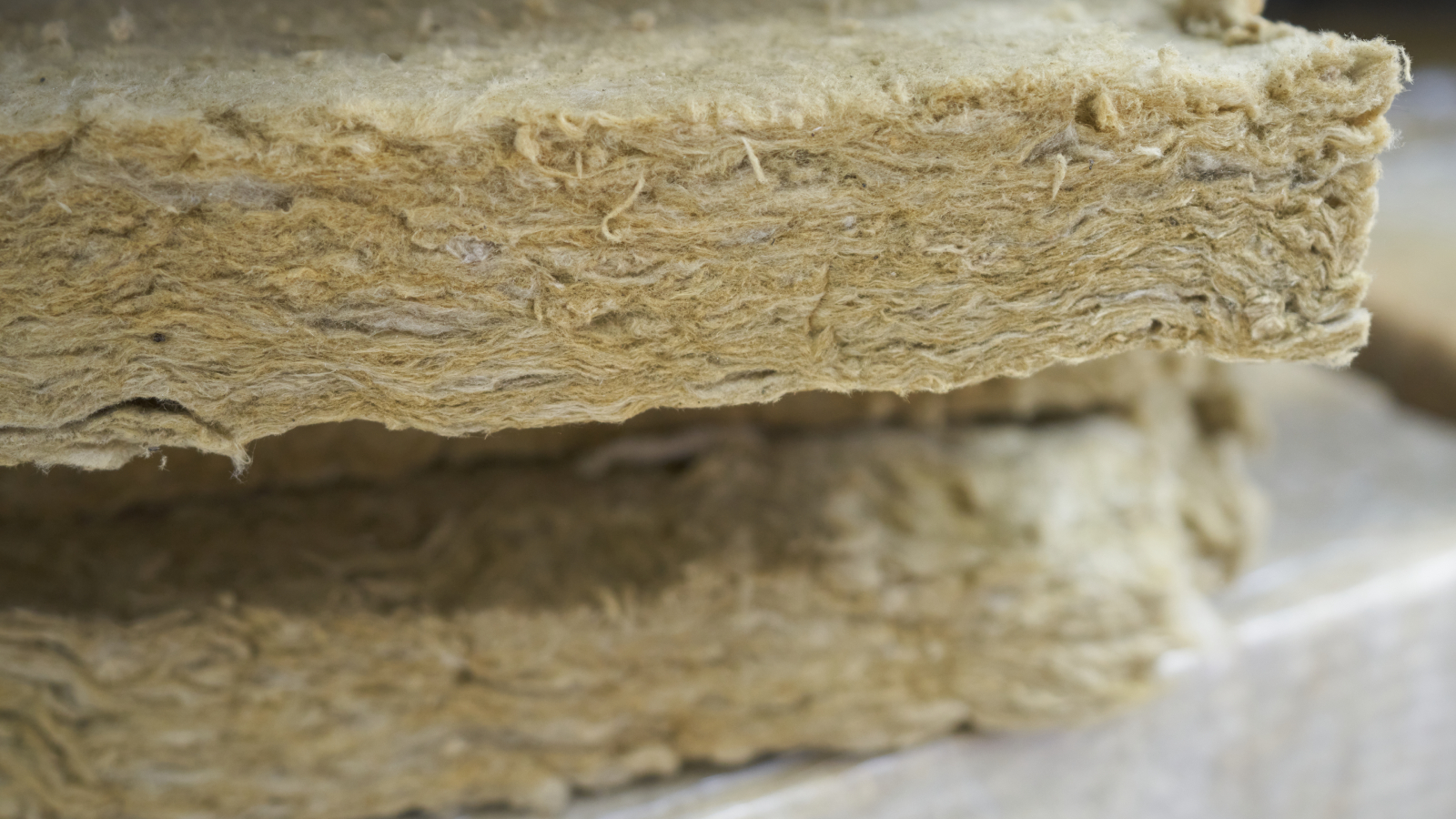
Insulating your home has never been more important. With rising energy costs and the global drive to reduce carbon emissions, making your home energy efficient helps both the environment and your pocket.
Cavity wall insulation plays a key role in this, offering lower heating bills and better indoor comfort. Whether you’re insulating a wall when building a new home, renovating, or adding an extension, it’s essential to understand the ins and outs of what's involved.
Self build expert, Mark Stevenson explains the basics of cavity wall insulation, its pros and cons, current UK building regulations, and the materials that are available, so you can you choose the best option for your new or existing home.
What is cavity wall insulation and why do you need it?
Cavity walls are external walls made up of two layers or 'skins' with a gap, or cavity, in between. This design became common in the UK from the 1920s, as it offered better weather protection and reduced damp issues.
Insulating cavity walls involves filling this gap with materials like mineral wool or rigid foam batts during construction. Alternatively, existing walls can be retrofitted by blowing in materials such as mineral wool, polystyrene beads, or expanding foam.
In poorly insulated homes, heat escapes easily, leading to wasted energy and money. About 25% of heat loss in a house happens through external walls. Insulating these walls is one of the most effective ways to reduce energy consumption. Beyond savings, it also lowers carbon emissions and improves indoor comfort by stabilising temperatures and reducing draughts and cold spots.
Pros and cons of cavity wall insulation
Cavity wall insulation is an effective way to improve energy efficiency. It reduces heat loss, lowers bills, and cuts carbon emissions. In new builds, high performance materials like PIR (polyisocyanurate) insulation boards can meet strict building regulations. For renovations, retrofitting insulation can significantly improve comfort and make systems like heat pumps more effective.
However, there are challenges. In new builds, ensuring high construction quality is vital to accommodate full-fill insulation. For renovations, issues like damp or poorly maintained walls can lead to cavity wall insulation problems. Using the wrong insulation or disrupting ventilation can also lead to condensation problems.
Poor workmanship when installing cavity wall insulation can be a costly problem. Since the insulation is hidden inside the walls, fixing defects can be difficult and expensive. To avoid issues, choose the right materials and follow proper installation practices to meet building regulations.
Ventilation and moisture management are key areas of concern as adding insulation can reduce air permeability and ventilation must be adequate to prevent condensation risk. To prevent defects, ensure vents and air bricks are not blocked by insulation, and add extra ventilation where needed, especially in high-humidity areas like kitchens and bathrooms.
Cavity wall insulation and building regulations
All cavity wall insulation must comply with Approved Document Part L (Conservation of Fuel and Power) of UK building regulations. This document sets energy efficiency standards for new and existing buildings. Updates introduced in 2022 made the standards even stricter, with ambitious targets to reduce carbon emissions by 31% in new homes compared to previous regulations.
The latest regulations require new walls to achieve a U-value of 0.18 W/m²K or better. However, in the case of new dwellings the actual U value will depend on the overall SAP assessment and the required U value could be much lower. U values measure how well a wall retains heat – the lower the U-value, the better the insulation.
Rigid PIR boards (thermal resistance: ~0.022 W/mK) require about 100mm thickness. Mineral wool (thermal resistance: ~0.034–0.040 W/mK) requires 170mm thickness to achieve the same U-value. Using thermal aggregate blocks in the inner layer of the wall can slightly reduce the required thickness.
To meet building regulations, masonry cavities are typically fully filled with insulation to maximise thermal performance. You have two main options when building new walls:
Install insulation during construction. Rigid boards are fixed to the inner skin as the wall is built.
Retrofit insulation after construction. This involves blowing materials like mineral wool or polystyrene beads into the cavity.
Cavity wall insulation in existing walls
For older homes with uninsulated cavity walls, retrofitting insulation is a great way to improve energy efficiency. However, not all walls are suitable. Before starting to retrofit insulation, it’s vital that the wall’s condition is assessed to have clear cavities.
This means the cavity must meet the minimum width (usually 50mm) and the gap must be free of debris to prevent damp bridging or cold spots. Walls should also be free from cracks and sealed against water ingress.
Make sure you choose the right material when adding cavity wall insulation to existing walls. In exposed areas, use water-resistant options like polystyrene beads or foam.
It's also important to note that if retrofitting is classified as a major renovation, regulations require a U-value improvement to 0.55 W/m²K or better.
Best insulation for cavity walls
When it comes to the best types of insulation for cavity walls, there are several materials to choose from, each with its own set of pros and cons.
Mineral wool is popular for its fire resistance and offers both a good acoustic and thermal performance, but it requires a thicker cavity to achieve the latest U values. Whilst mineral wool is popular, it may absorb moisture and could settle over time, leading to poor energy efficiency.
PIR boards are moisture resistant and offer excellent insulation with less thickness, making them ideal for reducing the footprint of cavity walls to maximise internal floor space, however they’re pricier and can be tricky to install, especially in irregular cavities.
Polystyrene beads are great for filling irregular cavities and resist moisture well and so are great for insulating walls subject to damp. However, they are more expensive than other options and questions are being raised about their combustibility.
Foam insulation (like polyurethane) has high thermal resistance and is easy to apply, even in narrow gaps, but it’s more expensive and can restrict cavity ventilation.
Sheep wool is highly sustainable and eco friendly and offers a natural defence to moisture. Unfortunately, its more expensive than synthetic alternatives and is not suitable for retrofit projects.
Choosing the right cavity wall insulation depends on your budget, wall type, and project needs. Whether you opt for mineral wool, PIR boards or foam, proper installation ensures long-term comfort, energy savings, and reduced carbon emissions.
The key to getting it right is to invest in quality materials and to use competent installers and with a high-quality install, cavity wall insulation will pay dividends for years to come.
For more information on insulating your home, follow our guides to the different types of roof insulation and make sure you know the main areas in a home never to insulate.
Get the Homebuilding & Renovating Newsletter
Bring your dream home to life with expert advice, how to guides and design inspiration. Sign up for our newsletter and get two free tickets to a Homebuilding & Renovating Show near you.
Mark Stevenson has worked as a construction professional for over 30 years and following an extensive career in housebuilding. He is currently chief operating officer for Custom Build Homes and chair of the National Custom and Self Build Association. He previously worked as managing director for Potton, helping self builders build their own homes.
Whilst Mark describes himself as a ‘professional builder’ as a result of his career in housebuilding and timber building system manufacturing, he has specialist knowledge of timber construction and extensive expertise in finding land and project management.
He regularly shares his knowledge at Homebuilding & Renovating Shows and and coaches self builders about how to build their own homes. Aside from Mark’s professional career, his skills also extend to practical building knowledge as a skilled joiner, hands-on renovator and serial self-builder of his own development projects.
He is also Vice Chair of industry body, the Structural Timber Association.