Do you need building regulations approval for installing a log-burning stove?
Our expert explains how to comply with building regulations when it comes to installing a log burner
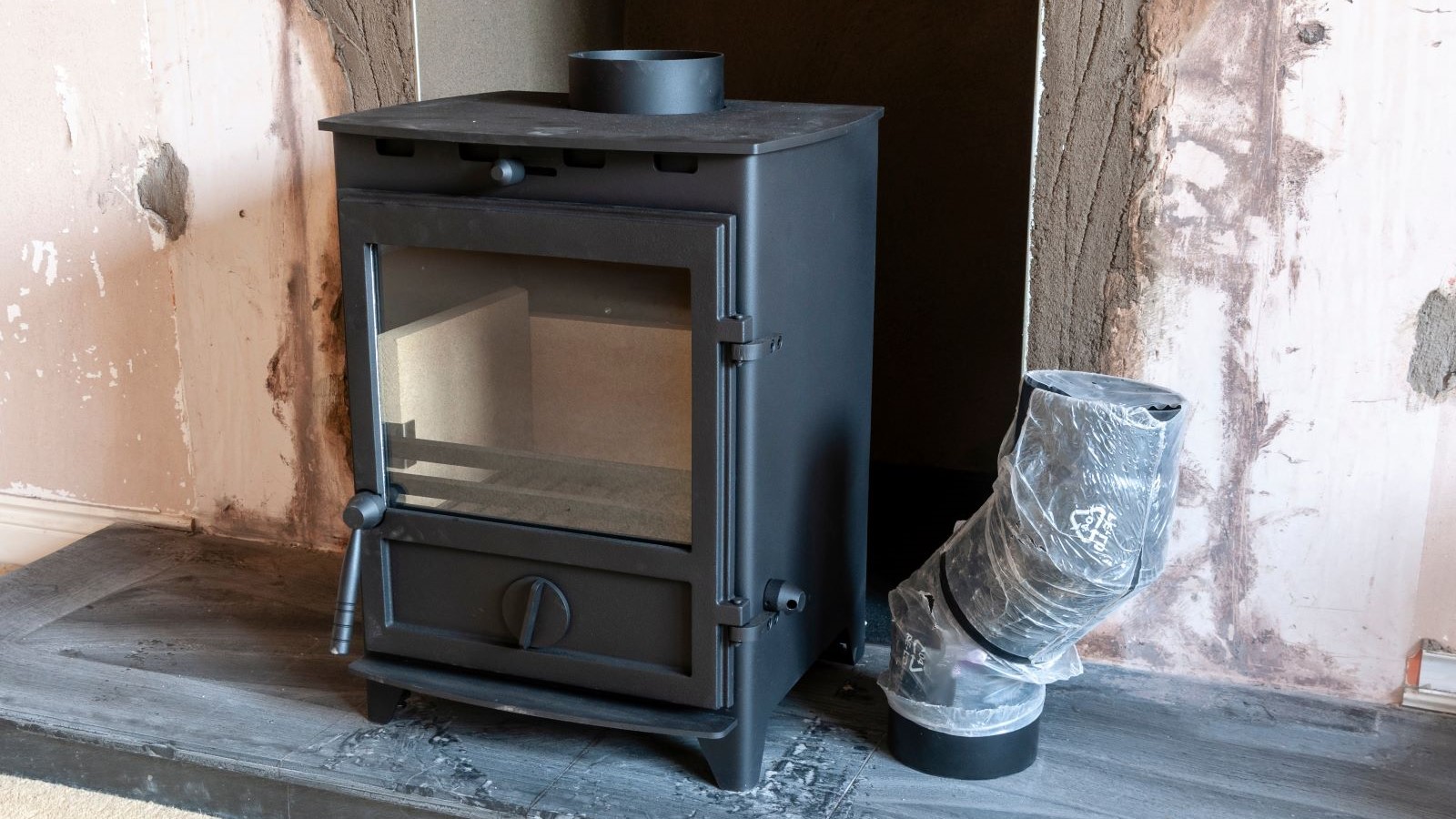
If you’re thinking about installing a log-burning stove, you’ve likely wondered, “Do I need building regulations approval?”
The answer is yes, and complying with these regulations ensures your log burner is installed safely and correctly. But it isn't quite as simple as a check-list that you need to run through with your unit. Satisfying building regulations can start before you've even purchased your log burner, in terms of where you hope to put it and whether the space is suitable.
Here our self build expert takes a deep dive into the building regulations for installing log burners, as well as looking at whether you can get approval if you install a log burner yourself, or if you should stick to paying a professional to do this for you.
Building regulations for installing log burners
The installation must comply with Part J of the Building Regulations, which covers combustion appliances and fuel storage. These regulations are crucial for fire safety, preventing carbon monoxide buildup, and ensuring proper ventilation.
The main requirements in this area of the building regulations are broken down below.
1. Part J1 – Combustion
Appliances must be installed to ensure there is an adequate supply of air to ensure they don’t overheat and work efficiently.
Proper ventilation is essential for a stove to burn efficiently and to prevent dangerous build-up of carbon monoxide. If your stove has a heat output of 5kW or less, it usually doesn’t need any additional ventilation. However, If the stove is being fitted in a new ‘airtight’ home, the lack of background ventilation means that it is unlikely to work properly and so a directly connected external air supply will be needed.
If your stove is rated at over 5kW, you’ll need to provide additional log burner ventilation.
This can typically be achieved by installing a permanently open-air vent or air brick in the same room as the stove. The size of the vent will depend on the stove’s output, and the amount of free air required will be stipulated in the stove manufacturer’s installation instructions. Alternatively, opt for a stove with a directly connected external air supply which will comply with the ventilation requirements but will limit heat loss from cold drafts.
Ventilation systems such as MVHR (mechanical, ventilation, heat, recovery) can force the spillage of fumes and gases from appliances because they pressurise rooms and adversely affect how flues operate. It’s therefore essential that homes with this ventilation system are professional assessed to ensure that installations operate correctly and are safe.
2. Part J2 – Discharge of products of combustion
Appliances must adequately discharge fumes to outside air.
The flue is a key part of any log burner installation because it’s what safely channels smoke and gases out of your home. The regulations around flues can get pretty technical, but in short, a flue should be designed for its purpose and should be made from materials that are suitable for high temperatures, such as stainless steel, pumice or concrete. You can buy flue kits or individual chimney parts from websites such as Direct Stoves.
To make sure everything works efficiently, the flue should be at least the same diameter as the flue outlet on your stove and meet the manufacturer’s requirements. Try to avoid bends in the flue as much as possible, since these can make it harder for smoke and gases to be extracted. Ideally, the flue should extend at least 4.5 metres from the top of the stove to where it exits the roof. It’s recommended that the flue comes out near the roof ridge, and to create a good draw, it needs to stick up at least 600mm above the roof or any nearby structures.
The top of the flue should have a terminal (like a chimney cap) that keeps rain out but still lets smoke escape freely. If you’re using an existing chimney, make sure it’s properly lined for the stove. Older chimneys might not be suitable for modern stoves and could leak harmful gases back into your home.
3. Part J3 – Warning of release of carbon monoxide
A carbon monoxide alarm must be installed in any room where a solid fuel appliance such as a log-burning stove is fitted. This requirement is designed to ensure that occupants are alerted if carbon monoxide is produced and escapes the stove or the flue system. Carbon monoxide is an invisible, harmful gas and the alarm provides an essential early warning to keep occupants safe.
Shop carbon monoxide alarms
4. Part J4 – Protection of the building
Log burner installation should be completed in such a way to prevent the risk of buildings catching fire.
Fire safety is one of the most important things to think about when installing a log burner. To avoid any risks, you need to make sure there’s enough space between the stove and anything that could catch fire, like walls or furniture. The general rule is that the stove should be at least 150mm away from combustible materials, but this can vary depending on the size and type of stove. It's therefore essential that you read the manufacturer's instructions which will specify the clearances required.
If the wall behind the stove is made from non-combustible materials, like brick or stone, you can reduce the separating distance. Just make sure you still leave enough room for maintenance and cleaning. One common issue is timber mantels, like these oak beams from Direct Stoves, above the fireplace. While these were used a lot in the past, today they’re considered combustible, so you’ll need to ensure there’s enough separation to prevent any fire hazards.
You also need to keep safe distances around the flue pipe, especially where it passes through walls, ceilings, or roofs with insulation or timber. In these cases, special collars are used to keep combustible materials at least 50mm away from the flue.
The stove will sit on a hearth, which needs to be non-combustible to protect the floor from heat and stray embers. The hearth should extend at least 300mm in front of the stove’s door and 150mm on either side, so any sparks won’t land on flammable flooring or carpets. If your stove keeps the hearth below 100°C, the hearth needs to be at least 12mm thick, but if it gets hotter, you’ll need a thicker base.
Remember, the exact separating clearances can vary from stove to stove, so always double-check the manufacturer’s instructions for your specific model and requirements.
5. Part J5 – Provision of information
When a new hearth, fireplace, flue, or chimney is installed, the installer must provide a durable notice that contains key information about the installation.
This notice should be placed in a suitable, visible location within the building. Its purpose is to inform anyone who may later install a combustion appliance about the specifications and limitations of the system, so they can ensure any new appliance is compatible with the existing setup.
Shop log burners and hearths
FAQs
What’s the easiest way to get building regs sign-off?
The simplest and most hassle-free way to get building regulations sign-off is to hire a HETAS-registered installer. HETAS is a recognised certification body for solid fuel and biomass heating systems in the UK.
A HETAS-registered installer will be able to self-certify the work, meaning you won’t need to apply separately for building regulations approval. After the installation is complete, they will provide you with a certificate of compliance, which shows that your stove installation meets all the necessary safety standards and regulations.
How do I get Building Regulations sign-off if I install a log burner myself?
Despite what you might read online, it’s perfectly fine to install a wood-burning stove yourself. However, the catch is that the installation must be signed off by a qualified person to ensure it meets building regulations.
If you’re installing the stove in an existing home, you’ll need to get Building Regulations approval from your local authority before starting the work. This means submitting an application with details about the stove, the flue system you’re planning to use, and how you’ll comply with the relevant regulations (specifically Part J of the Building Regulations). Once the installation is done, a building control officer will come out to inspect the work. They’ll not only check what you’ve installed but will also carry out a smoke test to make sure there are no leaks and that fumes are properly vented. They’ll review things like the distances between the stove and other materials, the hearth size, and ventilation. You’ll also need a carbon monoxide detector, and there should be an information plate outlining the details and specification of the installation.
If everything meets the necessary standards, they’ll issue a completion certificate. For new builds, this process is a little simpler, the application can form part of the full regs application, and the installation can be checked and signed off as part of the final completion inspection.
When installing a log-burning stove it’s essential that you understand and comply with the building regulations. Whether you choose to work with a HETAS-registered installer or go the DIY route, understanding the key regulations around clearances, hearth size, ventilation, and flues will ensure your installation is compliant with the regs and safe to use. For more advice, follow our guide to planning permission for log burners.
Bring your dream home to life with expert advice, how to guides and design inspiration. Sign up for our newsletter and get two free tickets to a Homebuilding & Renovating Show near you.
Mark Stevenson has worked as a construction professional for over 30 years and following an extensive career in housebuilding. He is currently chief operating officer for Custom Build Homes and chair of the National Custom and Self Build Association. He previously worked as managing director for Potton, helping self builders build their own homes.
Whilst Mark describes himself as a ‘professional builder’ as a result of his career in housebuilding and timber building system manufacturing, he has specialist knowledge of timber construction and extensive expertise in finding land and project management.
He regularly shares his knowledge at Homebuilding & Renovating Shows and and coaches self builders about how to build their own homes. Aside from Mark’s professional career, his skills also extend to practical building knowledge as a skilled joiner, hands-on renovator and serial self-builder of his own development projects.
He is also Vice Chair of industry body, the Structural Timber Association.